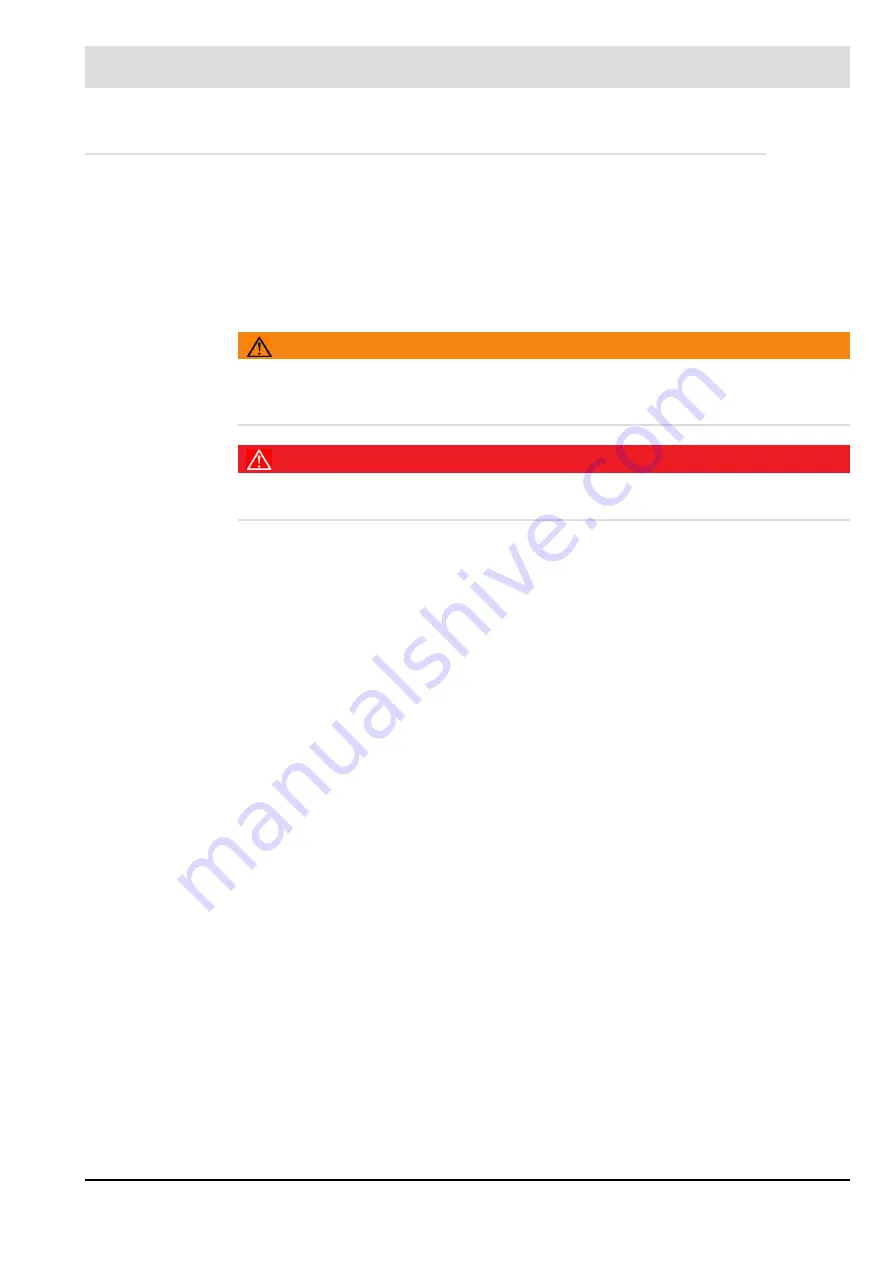
14
4 Operation
4.3
Proof Test Execution
To execute a proof test, the following test equipment is needed:
– Continuity tester with test current <= 50mA
– LAMTEC proof spotlight FFP30 (659M5000) or any suitable flame simulation
– LAMTEC operation manual F200K DLT7620
For the proof test of the F200K, the flame states ON and OFF must be stimulated. During the
test, the F200K is connected to the operating voltage.
WARNING!
The proof test is done with a continuity tester at the connecting cables oft the flame relay. To
protect the environment and to guarantee the correctness oft the test, the cables of the flame
relay (BN, GN, WH) must be disconnected before starting the test sequence.
DANGER!
If the cables of the flame relay (BN, GN, WH) are not disconnected completely, dangerous
voltages can be applied at the cable contacts.
To execute a basic proof test with a PTC of 70% for the F200K series, the following test steps
must be executed and approved.
– Disconnect cables BN, GN, WH (see operation manual DLT7620 chapter Circuit
Diagrams).
– Simulate state flame OFF.
– LED OFF (red) lights up (see operation manual DLT7620 chapter Appendix ‘Layout of the
Operational Controls‘).
– The flame relay opening contacts must be closed (cables BN and WH connected).
– The flame relay closing contacts must be open (cables BN and GN disconnected).
– Simulate state flame ON.
– LED ON (green) lights up and pulses (see operation manual DLT7620 chapter Appendix
Layout of the Operational Controls).
– The flame relay opening contacts must be opened (cables BN and WH disconnected).
– The flame relay closing contacts must be closed (cables BN and GN connected).
– Connect cables BN, GN, WH and check the proper operation of the device in the applica-
tion.
Summary of Contents for F200K2 IR-1
Page 1: ...www lamtec de Sensors and Systems for Combustion Engineering Safety Manual F200K...
Page 2: ......
Page 18: ...17 7 Appendix 7 Appendix 7 1 T V Confirmation...
Page 19: ...18 7 Appendix...
Page 21: ...20 8 EU Declaration of Conformity 8 EU Declaration of Conformity...
Page 22: ...21 8 EU Declaration of Conformity...