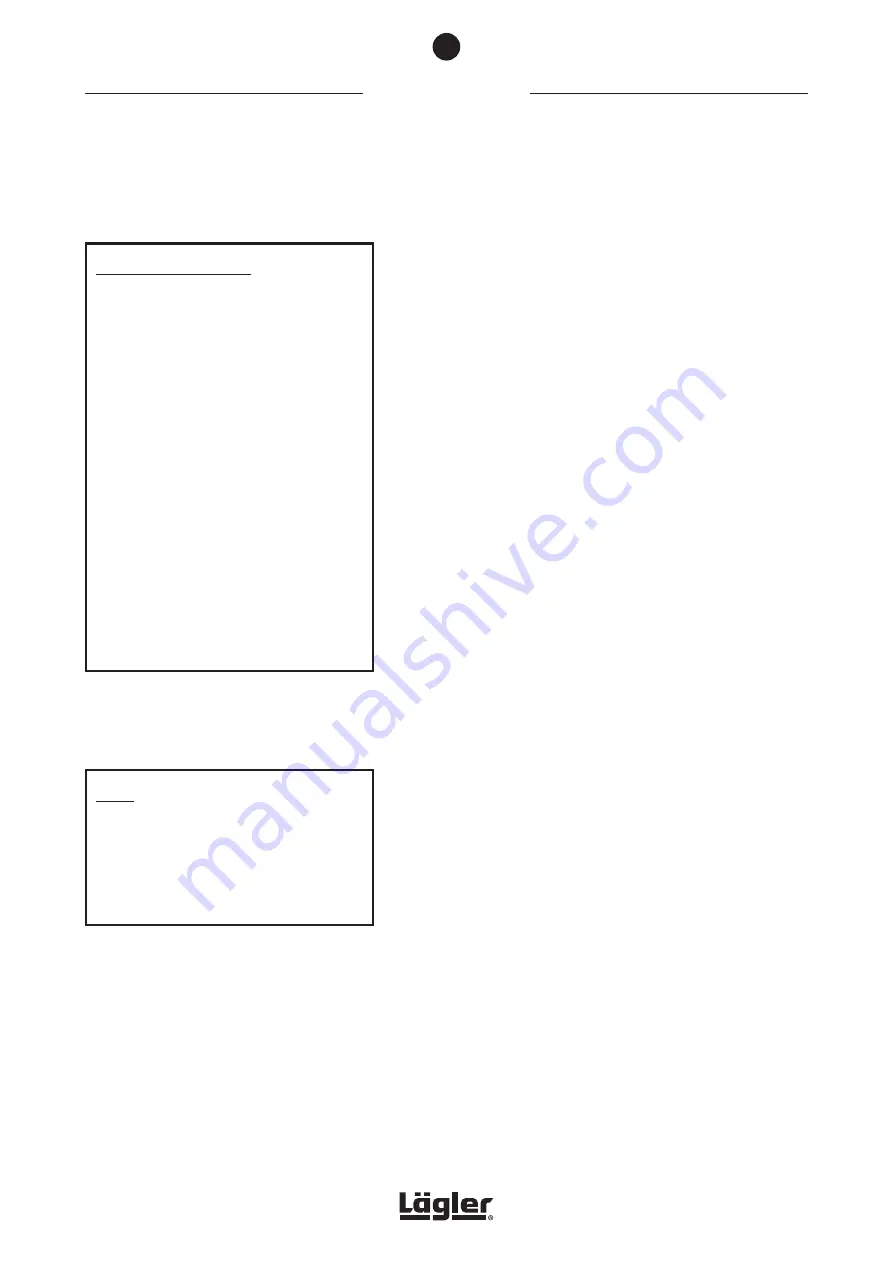
FLIP
®
01.12.2012
English / Englisch
TECHNICAL DATA
Technical data
Manufacturer ....................................................... Eugen Lägler GmbH
Machine type ..................................................edge-sanding machine
Serial number ................................................................ see type plate
Year of manufacture ..................................................... see type plate
Motor type .................................................................. universal motor
Voltage .......................................................................................... 230 V
Frequency ..................................................................... 50/60 Hz (CPS)
Output ........................................................................................1.35 kW
Fuse protection ...............................................................................10 A
Insulation class ................................................................................... F
Protection class ............................................................................IP 22
Protection system ............................................................................... 2
Safety devices ......................................................no-voltage release,
thermal overload protection
Sanding disc diameter ................................................ 150 mm (~ 5.9”)
Sanding disc diameter, corner attachment ................ 61 mm (~ 2.4“)
Sanding disc speed under load ................. approx. 3100 1/min (rpm)
Sanding disc speed under load,
corner attachment .................................... approx. 7750 1/min (rpm)
Attachment height without wall-protecting roller ..... 44 mm (~ 1.7”)
Attachment height with wall-protecting roller .......... 58 mm (~ 2.3”)
Corner attachment height ............................................ 51.5 mm (~ 2”)
Attachment length, short version .............................. 155 mm (~ 6.1”)
Attachment length, long version ............................. 315 mm (~ 12.4”)
Corner attachment length .......................................... 225 mm (~ 8.9”)
Overall height without dust bag ............................... 460 mm (~ 18.1”)
Overall length without dust bag
- with short attachment .......................................... 460 mm (~ 18.1”)
- with long attachment............................................ 620 mm (~ 24.4”)
- with corner attachment ....................................... 530 mm (~ 20.9”)
Overall width .............................................................. 260 mm (~ 10.2”)
Total weight ................................................................. 9.8 kg (21.6 lbs)
Dust emissions at workplace .............< 0.2 mg/m³ (0.0024 gr./cu.yd.)
(measured as per the testing requirements GS-HO-15 of
German lumber industry professional association)
Workplace-related noise emission values ..........................86 dB (A)
Measurement uncertainty constant of the
noise emission values ...........................................................4 dB (A)
Vibration total value a
hv
........................................................ < 2.5 m/s²
(measured at the handle)
3
NOTE on noise emission:
The values indicated are emission values
and must not represent safe workplace
values as well.
Although a correlation exists between emis-
sion levels and immission levels, it is not
always possible to determine whether addi-
tional precautionary measures are required.
Factors that can have an effect on the
immission level existing at the workplace
include the duration of the effects, the
characteristics of the work area and other
sources of noise, e.g. the number of ma-
chines and processing operations in the
vicinity. The permissible workplace values
may also vary from country to country.
This information, however, is intended to
enable the user to better estimate the dan-
gers and risks.
NOTE:
The motor data indicated here refers to
machines used in the Federal Republic of
Germany. Exported machines may have
other data that can be seen on the motor
type plate.
10
Summary of Contents for Flip
Page 48: ...FLIP 01 12 2012 English Englisch SPARE PARTS 48 11...
Page 50: ...FLIP 01 12 2012 English Englisch SPARE PARTS 50 11...
Page 52: ...FLIP 01 12 2012 English Englisch SPARE PARTS 52 11...
Page 54: ...FLIP 01 12 2012 English Englisch SPARE PARTS 54 11...
Page 56: ...FLIP 01 12 2012 English Englisch SPARE PARTS 56 11...