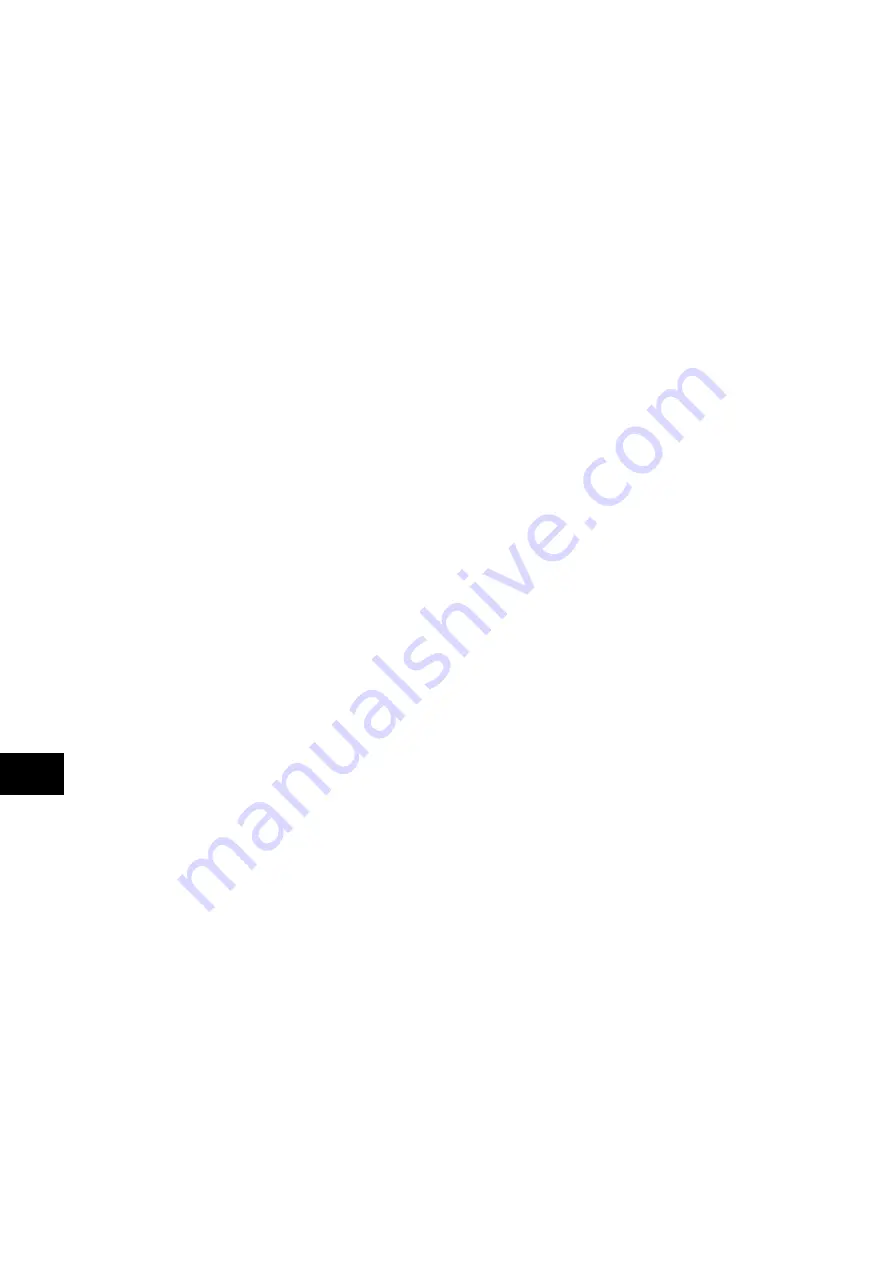
18
| HPI Combi Flow User Guide |
Version 3.11
www.lafert.com
4.2. Protective Earth (PE) Connection
4.2.1. Grounding Guidelines
Adequate safety earthing must be provided in accordance with local wiring rules and codes of practice. The ground terminal of each
HP Combi Flow should be connected back to the common safety earth bar to maintain touch potentials within safe limits. The ground
terminal of each HP Combi Flow should be individually connected DIRECTLY to the site ground bus bar (through the EMC filter if
installed). HP Combi Flow ground connections should not loop from one drive to another, or to, or from any other equipment. Ground
impedance must conform to local industrial safety regulations and/or electrical codes.
To meet UL regulations, UL approved ring crimp terminals should be used for all ground wiring connections.
The integrity of all ground connections should be checked periodically.
4.2.2. Protective Earth Conductor
The Cross sectional area of the PE Conductor must be at least equal to that of the incoming supply conductors.
4.2.3. Motor Ground
The driven motor must be locally connected to a suitable ground location to maintain touch potentials within safe limits. In addition, the
motor ground must be connected to one of the ground terminals on the drive.
4.2.4. Ground Fault Monitoring
As with all inverters, a leakage current to earth can exist. The HP Combi Flow is designed to produce the minimum possible leakage
current whilst complying with worldwide standards. The level of current is affected by motor cable length and type, the effective
switching frequency, the earth connections used and the type of RFI filter installed. If an ELCB (Earth Leakage Circuit Breaker) is to be
used, the following conditions apply:
A Type B Device must be used.
Individual device should be used for each HP Combi Flow.
The device must be suitable for protecting equipment with a DC component in the leakage current.
The device should not be sensitive to high frequency leakage current.
4.2.5. Shield Termination (Cable Screen)
The safety ground terminal provides a grounding point for the motor cable shield. The motor cable shield connected to this terminal
(drive end) should also be connected to the motor frame (motor end). Use a shield terminating or EMI clamp to connect the shield to
the safety ground terminal, refer to section
4.4. EMC Compliant Installation on page 19
.
4.3. Incoming Power Connection
Power should be connected to the L1 and L2 terminals for single phase drives, L1, L2 and L3 for three phase drives. Phase
sequence is not important.
For compliance with CE and C Tick EMC requirements, a symmetrical shielded cable is recommended.
A fixed installation is required according to IEC61800-5-1.
For units without an internal isolator / disconnect, a suitable disconnecting device should be installed between the HP Combi
Flow and the AC Power Source. The disconnecting device must conform to the local safety code / regulations (e.g. within Europe,
EN60204-1, Safety of machinery).
The cables should be dimensioned according to any local codes or regulations.
Suitable fuses to provide wiring protection of the input power cable should be installed in the incoming supply line, according to the
data in section
11.5. Output Power and Current ratings
. The fuses must comply with any local codes or regulations in place. In general,
type gG (IEC 60269) or UL type J, T or CC fuses are suitable; however in some cases type aR fuses may be required. The operating
time of the fuses must be below 0.5 seconds.
Where allowed by local regulations, suitably dimensioned type B MCB circuit breakers of equivalent rating may be utilised in
place of fuses, providing that the clearing capacity is sufficient for the installation.
When the power supply is removed from the drive, a minimum of 30 seconds should be allowed before re-applying the power.
A minimum of 10 minutes should be allowed before removing the terminal covers or connection.
The maximum permissible short circuit current at the HP Combi Flow Power terminals as defined in IEC60439-1 is 100kA.
4
Elec
trical Installation