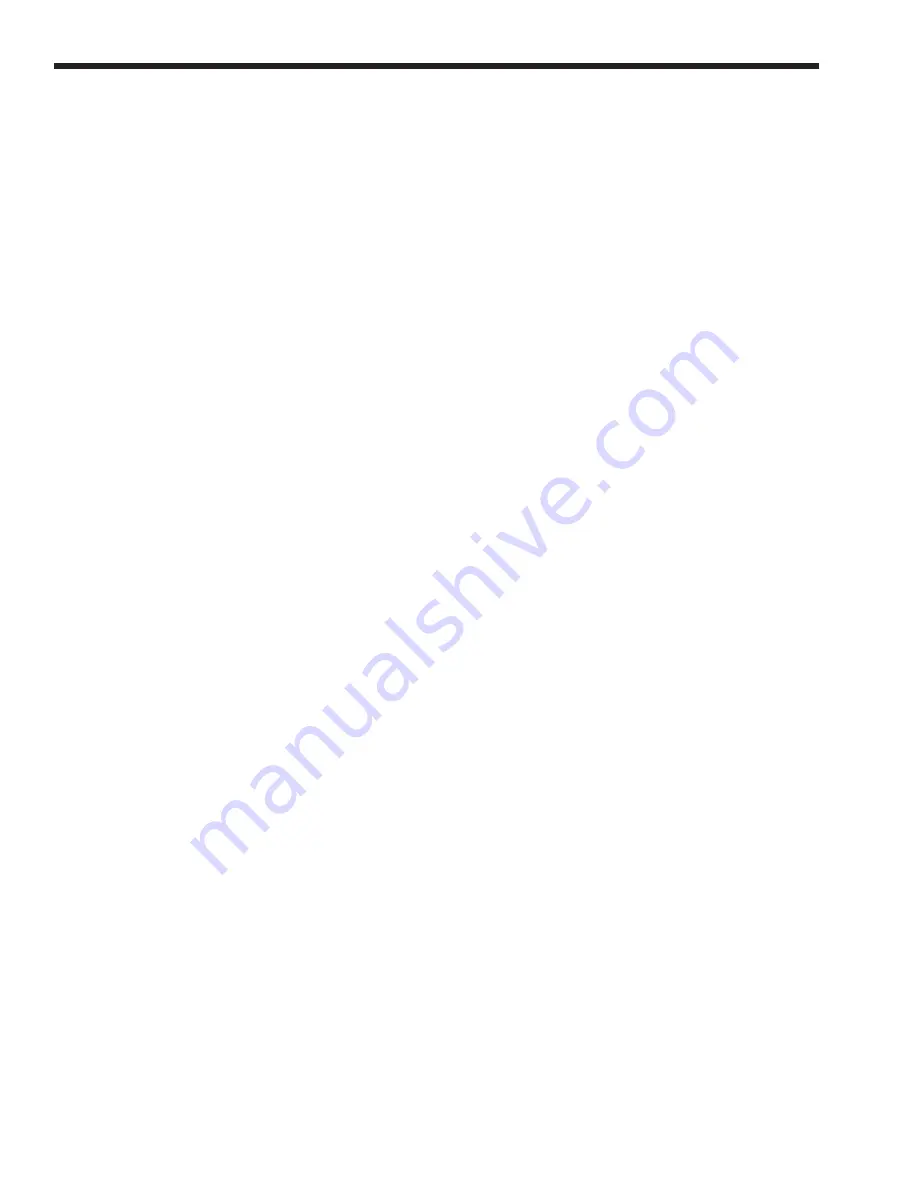
LAARS Heating Systems
Page 36
the setpoint of the boiler operating control. If the set
points are correct and the system design, controls
scheme, etc. are fixed, the temperature differentials
may be increased to reduce short cycling. If desired
temperature response is not achievable without short
cycling it may be necessary to install a buffer tank
in the system. Contact your Laars representative to
discuss possible remedies.
8.4 Short Cycling — Water Heater
Short cycling will generally occur only in
combination space heating and water heating
applications when the water heater is operating in the
space-heating mode. If the heating load drops below
the minimum input of the water heater for an extended
period, the water heater will have a tendency to short
cycle. If short cycling is frequently experienced,
regardless of the control’s attempt to limit it, the
heating load should be redistributed to control it.
If short cycling occurs in a water heater
application, it is probably caused by undersized
piping between the water heater and the storage tank
or by some other factor that restricts proper water
flow through the water heater. The cause should be
determined and corrected.
8.5 High Gas Consumption
Appliances operating with an improper air/
fuel ratio are very inefficient and consequently, have
very high gas consumption. Because efficiency is
high when the CO
2
is high (or O
2
is low), appliances
operating with low CO
2
or high O
2
(especially LP
appliances) consume more gas. Adjust the CO
2
or O
2
for optimum efficiency. If no combustion analyzing
equipment (CO
2
or O
2
) is available then a proper
adjustment of the air/fuel ratio (CO
2
or O
2
) cannot be
accomplished. The CO
2
should be 8% at high fire for
natural gas and 9.2% at high fire for LP. To check the
CO
2
, first verify that the supply gas pressure is within
5 to 13 in. w.c. (1.2 to 3.2 kPa). With the Pennant
running, set the air box pressure to 1.5 in. w.c. (0.37
kPa) (as a starting point), by adjusting the air shutter(s)
at the intake of the fan(s). Check the CO
2
, and adjust
the air shutters if further adjustment to the CO
2
is
needed.
8.6 Troubleshooting Pennant Controls
A diagnostic panel, that includes test points, as
well as diagnostic lights, is provided in the control
module. It is located on the right side of the module,
behind the display. To access, remove the retaining
screws from the display cover panel and remove
it. Grasp the control module at its base and pull it
outward.
Pennant ladder diagrams are shown in
Figures
12 and 13
. The wiring connection diagrams are shown
in
Figures 14 through 16.
The blower is energized
directly through the “inducer” terminals F1 and F2 of
the (Fenwal) ignition module. The 24V power to the
T’STAT terminal of both ignition modules is routed
through the safety interlocks.
All 24V wiring is routed through the diagnostic
PC board. Wiring harnesses connect between the
diagnostic PC board and the control components,
indicator board, or field wiring terminal strip. The
diagnostic board contains LEDs that indicate open
status of the safety interlocks, and quick-connect
terminals that provide tests points for checking
voltage/continuity at various points in the control
circuit.
Line-voltage connections are routed via the
line-voltage terminal buss. Certain control elements
that may need to be rewired in the field are connected
via the field wiring terminal strip rather than to the
diagnostic PC board. These include the low-water
cutoff (LWCO), water flow switch, and inlet/outlet
water temperature sensors.
SECTION 9.
Replacement Parts
Only genuine Laars replacement parts should be used.
9.1 General Information
To order or purchase parts for the Laars Pennant,
contact your nearest Laars dealer or distributor. If
they cannot supply you with what you need, contact
Customer Service (see back cover for address,
telephone and fax numbers).
9.2 Parts List
See next page for the list of available replace-
ment parts. See
Figures 19-21
for exploded views
of the boiler's component systems to help identify
replacements parts.
Summary of Contents for Pennant PNCH
Page 23: ...Low Temperature Pennant Page 23 Figure 12 Ladder Diagram Sizes 500 1000 ...
Page 24: ...LAARS Heating Systems Page 24 Figure 13 Ladder Diagram Sizes 1250 2000 ...
Page 25: ...Low Temperature Pennant Page 25 Figure 14 Wiring Diagram Sizes 500 1000 ...
Page 26: ...LAARS Heating Systems Page 26 Figure 15 Wiring Diagram Sizes 1250 1500 ...
Page 27: ...Low Temperature Pennant Page 27 Figure 16 Wiring Diagram Sizes 1750 2000 ...