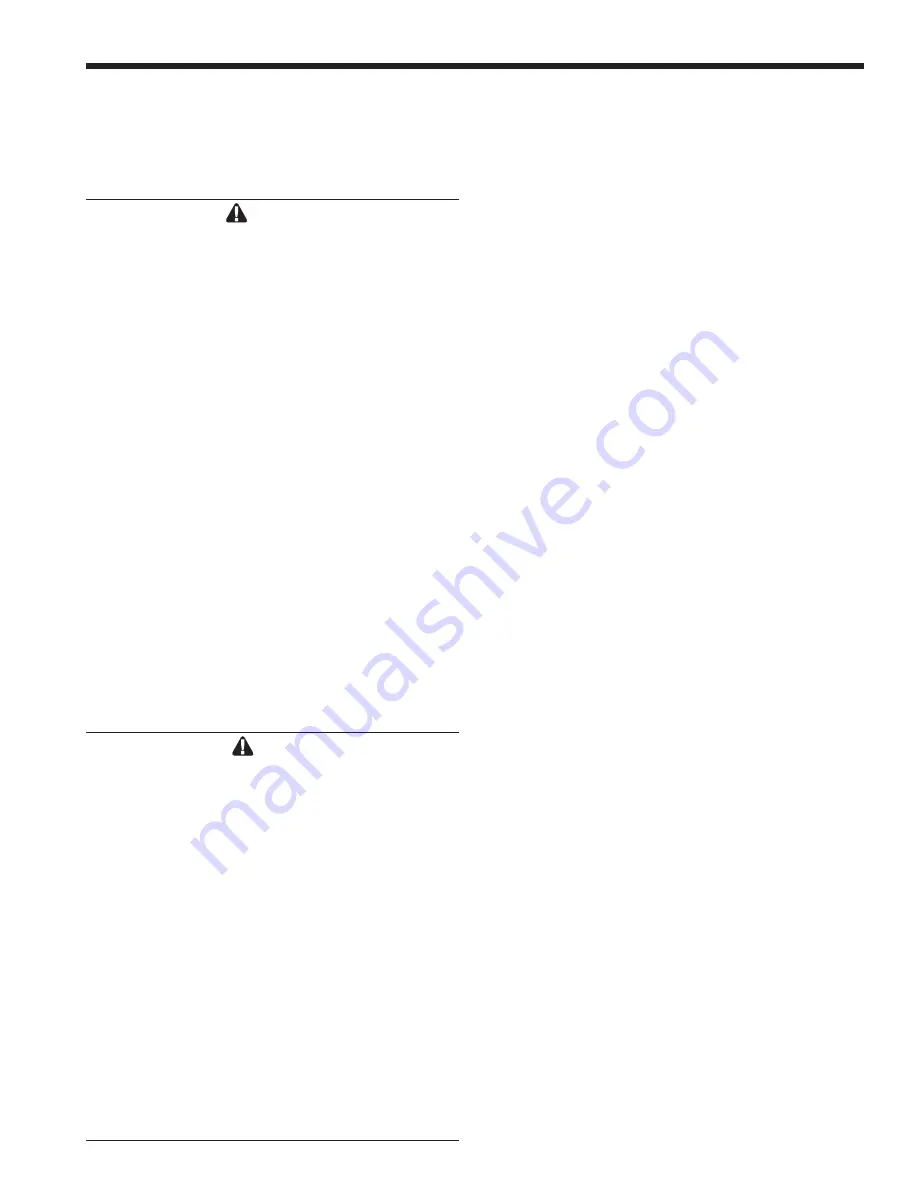
Page 45
SECTION 7
INSTALLATION AND WIRING
7.A Installation Warnings
WARNING
The appliance must be electrically grounded in
accordance with the requirements of the authority
having jurisdiction or, in the absence of such
requirements, with the latest edition of the National
Electrical Code, ANSI/NFPA 70, in the U.S. and with
the latest edition of CSA C22.1 Canadian Electrical
Code, Part 1, in Canada. Do not rely on the gas or
water piping to ground the metal parts of the boiler.
Plastic pipe or dielectric unions may isolate the boiler
electrically. Service and maintenance personnel, who
work on or around the boiler, may be standing on wet
floors and could be electrocuted by an ungrounded
boiler. Electrocution can result in severe injury or
death.
Single pole switches, including those of safety
controls and protective devices, must not be wired in
a grounded line.
All electrical connections are made on the terminal
blocks that are located inside the control panel.
Wiring connections are shown in Figure 34.
All internal electrical components have been
prewired. No attempt should be made to connect
electrical wires to any other location except the
terminal blocks.
Caution
The supply voltage to the unit must not be
disconnected, except for service or isolation, or
unless otherwise instructed by procedures outlined
in this manual. To signal a call for heat, use the 24V
field interlock, as shown in the wiring diagram.
DO NOT MAKE AND BREAK THE LINE VOLTAGE
TO THE UNIT TO SIGNAL A CALL FOR HEAT.
A call for heat/ end call for heat MUST be connected
to the field interlock terminals. Some components
are designed to have constant voltage during normal
operation. If the units’s supply voltage is toggled
as a call for heat signal, premature failure of these
components may result.
The unit does not recognize 4mA as a call for heat.
If the call for heat is not connected between the
field interlock terminals, the unit will remain in low
fire when it sees 4mA as a modulating signal. See
Section 7.4 for more details.
7.B Main Power Connections
The size of the main power supply should be
determined by Table 16 and Table 17 on page 47
These tables indicate the unit’s maximum overcurrent
protection (MOP) and Minimum Circuit Ampacity (MCA).
An overcurrent protection value should be selected
based on these numbers.
Please note that all units with Laars supplied pumps
399 and greater, it is necessary to use two circuits.
One circuit is to feed the boiler/water heater while
the other is for the pump. Again, MCA and MOP are
provided for both the unit and Laars provided pump.
7.B.1
Pump Connections and Operation
The unit energizes the boiler pump contacts (dry) when
it receives a call for heat. Once the call for heat is
satisfied, the pump will remain on for the defined pump
overrun time.
The contacts for the system and DHW pump are dry
contacts. Appropriate voltage must be supplied to the
system and DHW pumps or relay controlling the pumps
for proper operation.
All pump connections are located on terminal block
5 (TB5) in the control panel (See Figure 33 on page
46).
Any pump using the unit’s control relay may not
exceed 7.4 amps as governed by the integrated control
board. If more current is required, and additional pump
contactor must be installed.
Pump contactors are not included, unless the unit was
ordered with a pump, and its FLA exceeds 7.4 amps.
Included pump contactors are rated for 3hP. Power for
the coil may be supplied by TB5. TB5 is a dry contact,
and will accomodate low voltage, as well as 120V.
When units are purchased with a pump, the unit and
the pump may be powered with a single circuit. See
Table 16 and Table 17 on page 47
for electrical data.
When using one circuit, review the available MCA
and MOP. If the appropriate over-current protection
exceeds 18 amps, the circuits should be separated. In
this case, additional 120VAC circuits will be required
for the pump(s) and potentially for a separate pump
contactor.
N
EO
T
HERM
Commercial Boilers and Water Heaters
Summary of Contents for NEOTHERM NTH
Page 4: ...LAARS Heating Systems ...
Page 36: ...Page 36 Figure 22 Hydronic Piping Single Boiler Zoning with Circulators LAARS Heating Systems ...
Page 52: ...Page 52 Figure 36 Ladder Diagram 7 H Ladder Diagram LAARS Heating Systems ...
Page 100: ...Page 100 Parts Illustration 4 Internal Components Sizes 750 850 LAARS Heating Systems ...
Page 102: ...Page 102 Parts Illustration 6 Gas Train Components Sizes 600 850 LAARS Heating Systems ...