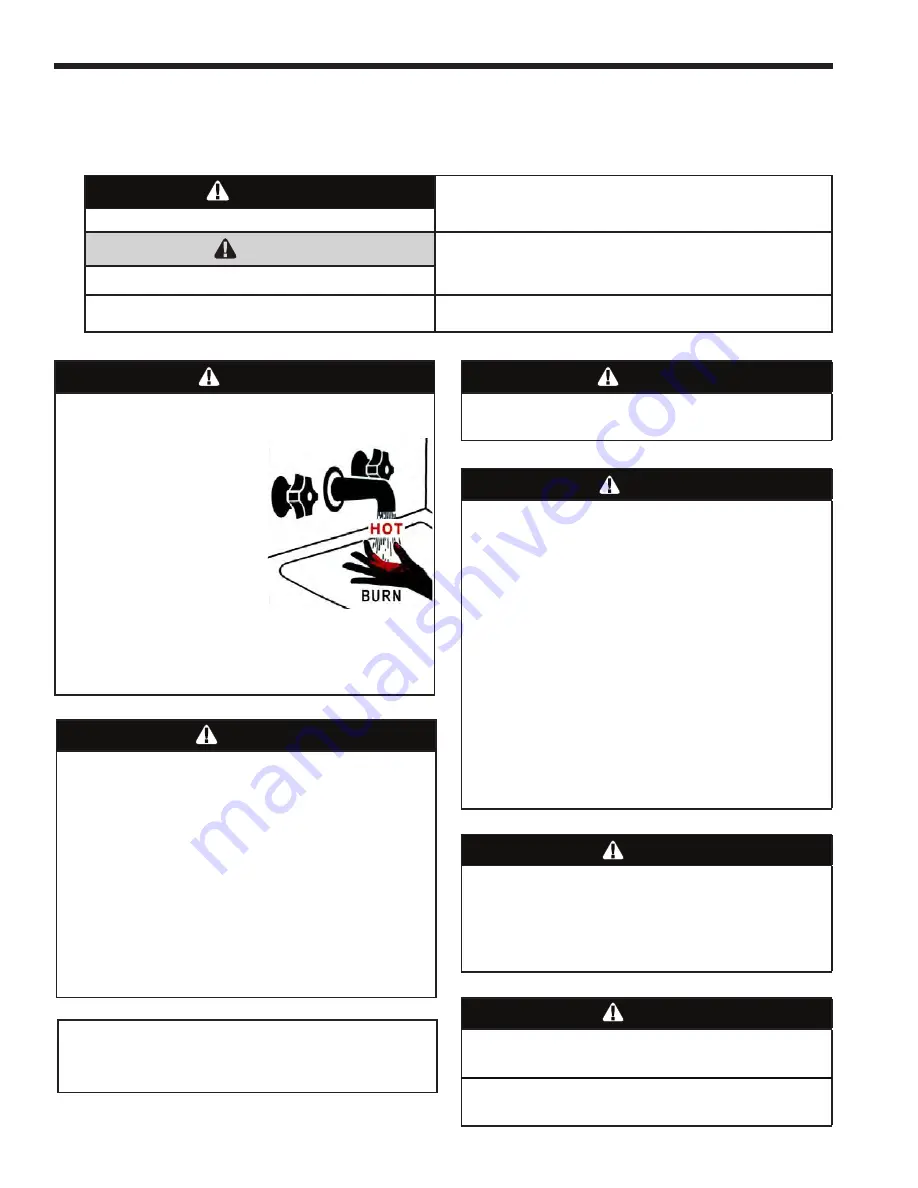
Page 6
LAARS Heating Systems
1.D Safety Notes
WARNING
Carbon Monoxide Hazard
Improper adjustment of the burners may lead to poor
combustion quality, increasing the amount of carbon
monoxide produced. Excessive carbon monoxide
levels may lead to personal injury or death.
WARNING
This unit must be installed in accordance with the
procedures detailed in this manual, or the manufacturers
warranty will be voided. The installation must conform
to the requirements of the local jurisdiction having
authority, and, in the United States, to the latest edition
of the National Fuel Gas Code, ANSI Z223.1/NFPA54.
In Canada, the installation must conform to the latest
edition of CSA B149.1 Natural Gas and Propane Gas
Installation Code, and/or local codes. Where required
by the authority having jurisdiction, the installation of
these units must conform to the Standard for Controls
and Safety Devices for Automatically Fired Boilers,
ANSI/ASME CSD-1. Any modifi cations to the boiler, its
gas controls, or wiring may void the warranty. If fi eld
conditions require modifi cations, consult the factory
representative before initiating such modifi cations.
WARNING
• Water temperature over 125°F (52°C) can cause
severe burns instantly or death from scalds.
• Children, disabled and
elderly are at highest
risk of being scalded.
• See instruction manual
before setting temperature
at the unit.
• Feel water before bathing
or showering.
• If this unit is used
to produce water that could scald if too hot, such
as domestic hot water use, adjust the outlet control
(limit) or use temperature limiting valves to obtain a
maximum water temperature of 125°F (52°C).
WARNING
The inlet gas pressure to the unit must not
exceed 13” W.C. (3.2kPa).
WARNING
Fire or Explosion Hazard
Improper confi guration can cause fuel buildup and
explosion. Improper user operation may result in
property loss, severe physical injury, or death.
Any changes to safety-related confi guration
parameters must only be done by experienced and/or
licensed burner/boiler operators and mechanics.
If any odor of gas is detected, or if the gas burner does
not appear to be functioning in a normal manner, close
the main gas shutoff valve. Do not shut off the power
switch. Contact your heating contractor, gas company,
or factory representative.
NOTE: This unit is protected against hydronic
over-pressurization. A pressure relief valve is included
with each unit.
WARNING
Indicates an imminently hazardous situation which, if not
avoided, can or will result in death or serious injury and can
or will result in catastrophic property damage.
CAUTION
Indicates a potentially hazardous situation which, if not avoided,
may result in moderate injury and/or property damage.
NOTE:
Indicates instructions that are important to that topic but not
related to personal injury or property damage.
Safety Notes are used thoughout this manual to bring attention to the presence of hazards with various risk
levels and to off er important information concering the life of this product. There are 3 basic types.
WARNING
CANCER AND REPRODUCTIVE HARM.
WWW.P65WARNINGS.CA.GOV.
AS REQUIRED BY THE STATE OF
CALIFORNIA PROPOSITION 65.
1
2
3
Summary of Contents for NEOTHERM NTH Series
Page 4: ...LAARS Heating Systems...
Page 24: ...Page 24 LAARS Heating Systems Figure 9 Hydronic Piping Single Boiler Zoning with Circulators...
Page 33: ...Page 33 NEOTHERM Residential Boilers Figure 16 Control Panel Layout...
Page 38: ...Page 38 LAARS Heating Systems Figure 19 Ladder Diagram 7 H Ladder Diagram...
Page 67: ...Page 67 NEOTHERM Residential Boilers Figure 44 Heat Exchanger Components 68A 65 67 60 66 63 64...
Page 68: ...Page 68 LAARS Heating Systems Figure 45 Electrical Components...
Page 82: ...LAARS Heating Systems Notes...