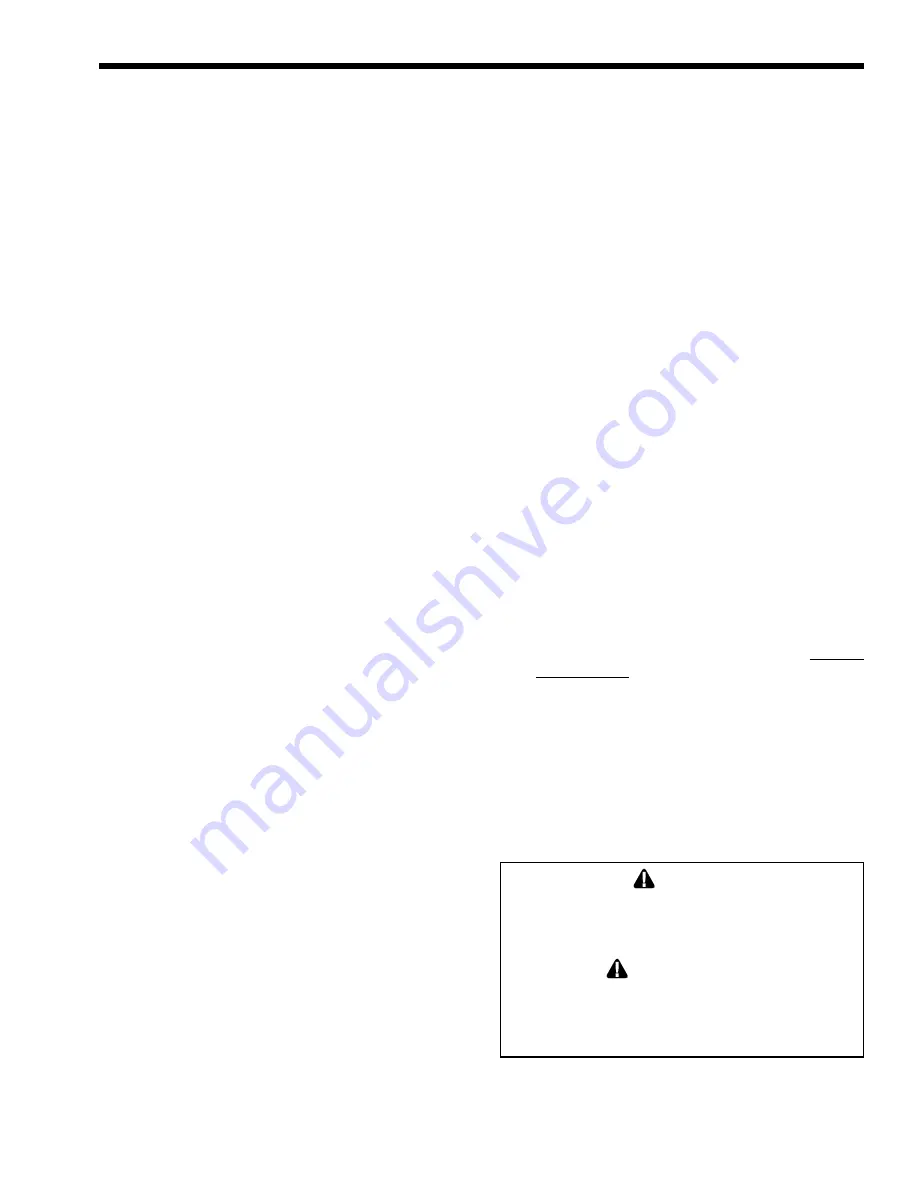
Mini-Therm JV
Page 29
when the draft inducer starts (depending on
the boiler size, swing may be as little as 30°).
Remove any obstructions and clean around the
pivot rod (handle) holes.
5. Inspect the venting system for obstruction,
leakage or corrosion at least once a year.
6. Keep the boiler area clear and free from
combustible materials, gasoline, and other
flammable vapors and liquids.
7. Be sure that all combustion air and ventilation
openings are unobstructed.
8. Upon completion of the installation, inspect
the external surfaces of the heat exchanger for
fouling based on the following schedule:
24 hours - 7 days - 30 days - 90 days
Once every six months thereafter.
9. If the boiler is not going to be used for long
periods of time in locations where freezing
occurs, it should be completely drained of
all water. To accomplish this, there is a drain
valve on the right side of the boiler which can
be opened. This will drain the right side of the
boiler. There are two plugs located on the left
side of the heater which must be removed to
drain that side. Both sides must be drained.
10. The gas and electric controls on the boiler
are engineered for long life and dependable
operation, but the safety of the equipment
depends on their proper functioning. It is strongly
recommended that the basic items listed below be
inspected by a qualified service technician every
year.
a. Water temperature controls.
b. Pilot safety system.
c. Automatic gas valves.
d. Fan proving switch.
e. Inducer/Blower assembly.
f.
Mechanical flue damper operation.
WARNING
The Warranty does not cover damage caused by
lack of required maintenance, lack of water flow,
or improper operating practices.
AVERTISSEMENT
La garantie ne couvre pas les dommages causés
par l'absence d'entretien, absence de débit d'eau,
ou pratiques de fonctionnement irrégulières
Fouling on the external surfaces of the heat exchanger
is caused by incomplete combustion, and is a sign
of venting and/or combustion air problems. The heat
SECTION 9.
9A. Maintenance
1. Lubricate the water circulating pump per the
instructions on the pump.
2. If a strainer is employed in a pressure reducing
valve or the piping, clean it every six months.
3. At start-up, and periodically thereafter, the
burner and pilot flames should be observed. If
the flame has the appearance of “sooting” tips,
check for debris near the orifices and call the
service technician.
4. Ensure proper operation of the mechanical
damper, mounted in the flue collar, by observing
the damper handle. Be sure the handle swings
HEAT and the control is in WWSD the HEAT call will
be ignored. When there is a call for DHW and the
control is in WWSD the DHW call will be satisfied.
WWSD LED turns on when control detects WWSD.
Summary of Dip Switch Settings:
#1 Two Stage (Off) / Single Stage (On)
#2 (Off) / Outdoor Reset (On) (Note: Outdoor
Reset is required for residential operation)
#3 WWSD Inactive (Off) / Active 70°F (On)
#4 Boiler Maximum 210°F (Off) / 190°F (On)
#5 Pump Post Purge Inactive (Off) / Active 3 min.
(On)
LEDs State Description
1. Power
2. Heat – On = call for heat; Flashes for Boiler
sensor error
3. DHW – On = call for DHW; Flashes for
outdoor sensor error
4. WWSD – On = Outdoor Reset AND WWSD
Active AND control in WWSD; Flashes for
outdoor sensor error, operation continues with
fixed boiler target of 140°F.
Summary of Input Sensors:
1. Outdoor sensor - monitors the outside air
temperature for outdoor reset mode
2. Boiler outlet sensor -monitors the water
temperature of the boiler outlet supply
3. System Supply sensor - monitors the water
temperature of the system supply
The boiler outlet sensor is required at all times. If
the boiler outlet sensor has any fault then the control
will flash an error and turns all stages off. The
system supply sensor is optional and utilizes primary
/ secondary piping. If the system supply sensor has
a fault then the control flashes an error message and
operates using the boiler outlet sensor (system supply
= boiler outlet).