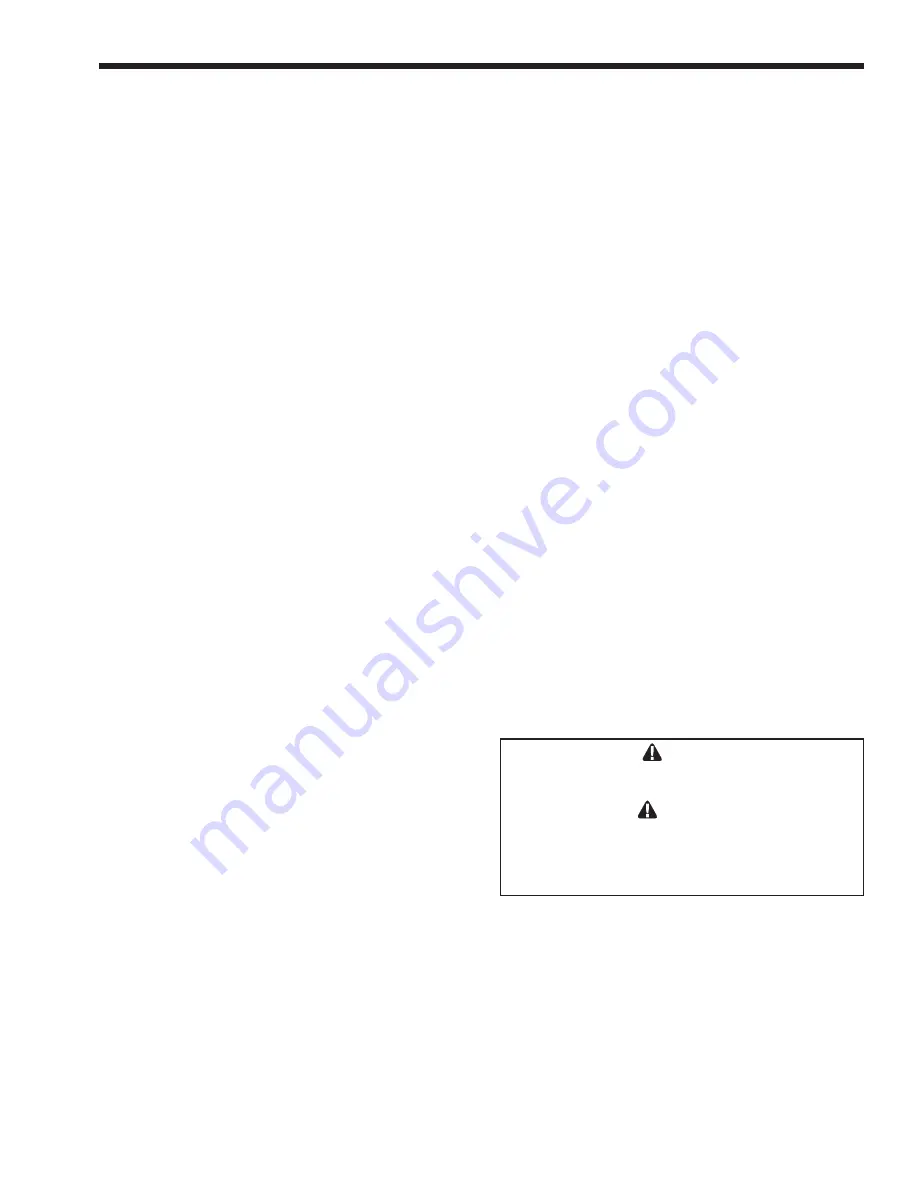
Mighty Therm
2
(200, 300, 400)
Page 31
h. Pump (if required)
i.
Relays
j.
Flow switch
k. Gas train
l.
Control components
7.2.1 Burners
Close main manual gas valve before proceeding.
Checking the burners for debris - Remove the ignitor/
burner access panel and ignitor, and inspect the
burners through the ignitor hole using a flashlight to
illuminate. If there is any indication of debris on the
burners that is visible, all the burners will need to be
inspected more thoroughly. Remove the gas manifold
assemblies and the burner assemblies. Inspect the
burners. Clean burners, if necessary, by blowing
compressed air from the outside of the burners into
the center of the burner. A dirty burner may be an
indication of improper combustion or dirty combustion
air. Determine the cause, and correct. Replace the
burners in the reverse order.
7.2.2 Filter
The filter used in the Mighty Therm2 is washable
and has an 80% arrestance rating. Since the filter is
washable, it will only need replacement occasionally.
If filter replacement is needed, it should only be
replaced with a factory part. Inspect the air filter
monthly, or more often in dirty environments. If there
is debris on the air filter, remove it from the filter
frame, and wash it with mild soap and water. Ensure
that the filter is completely dry before reinstalling.
7.2.3 Gas Valves
The gas valves are designed to operate with
supply pressures of 4-13 in. w.c. (1.0 to 3.2 kPa).
To remove a valve, shut off 120-volt power
and the manual gas shutoff valve. Remove the front
panels from the unit. Disconnect the wires to the valve.
Disengage the unions before and after the valve, and
remove the valve. Pull the pipe nipples from the inlet
and outlet of the valve, and clean the threads on the
pipe nipples for reuse. Apply new tape or pipe dope
to the pipe nipples (threaded joints should be coated
with piping compound resistant to action of liquefied
petroleum gas), and reinstall in reverse order. Turn
on manual gas shutoff valve and 120 volt power and
check appliance operation and tightness of gas valve
connections.
7.2.4 Manual Reset High Limit Control
The high limit switch is a manual reset, non-
adjustable switch with a remote bulb-type sensor.
Switches for water heaters and low temperature boiler
models are set at 200°F. Switches for standard boilers
are set at 240°F.
The control is located behind the front door, on a
panel in front of the blower. The probe is in the outlet
side of the header.
To reset the switch, unscrew the black cover that
is over the reset button, and push the button. Replace
the cover after the switch is reset.
To replace, shut off power to the appliance.
Remove the cover that is over the button, and remove
the nut that is around the button. Pull the control
through the panel, and remove the spade terminals.
Replace in reverse order.
7.2.5 Ignition Control
The ignition control controls the hot surface
ignitor and proves that the flame signal is appropriate
for powering the gas valves. It also controls the
blower’s pre-purge and post-purge.
To replace a control, shut off the 120-volt power
to the appliance. Remove the cover from the control
panel. Remove the electrical connectors from the
ignition control. Take out the controller’s mounting
screws, and pull the controller out. Replace in reverse
order.
7.2.6 Ignitor
The ignitor used is a 120v “Hot Surface” type.
It is energized whenever there is a call for heat and
switched off when ignition is established and the flame
has been sensed. To replace the ignitor, shut off the
120-volt power to the appliance, remove the ignitor/
burner access panel, disconnect the Molex connector,
remove the two mounting screws on the ignitor flange,
and pull the ignitor out. Install in reverse order, always
using a new ignitor gasket with the replacement
ignitor.
Caution
Ignitor gets hot. To avoid injury, handle the ignitor
with caution.
Attention
Le dispositif d’allumage devient très chaud.
Manipulez le dispositif d’allumage avec
précaution.
7.2.7 Transformer
The Mighty Therm2’s transformer is not capable
of supplying control voltage for external devices such
as zone valves, which must have their own separate
power supply. Should a transformer need replacing,
shut off the 120-volt power. Unplug the transformer
wires, remove the mounting screws and remove the
transformer. Replace transformer in the reverse order.
7.2.8 Flow Switch
The Mighty Therm2 uses a paddle-type flow
switch to ensure that the unit has water flow before
ignition is allowed. To replace the flow switch, turn