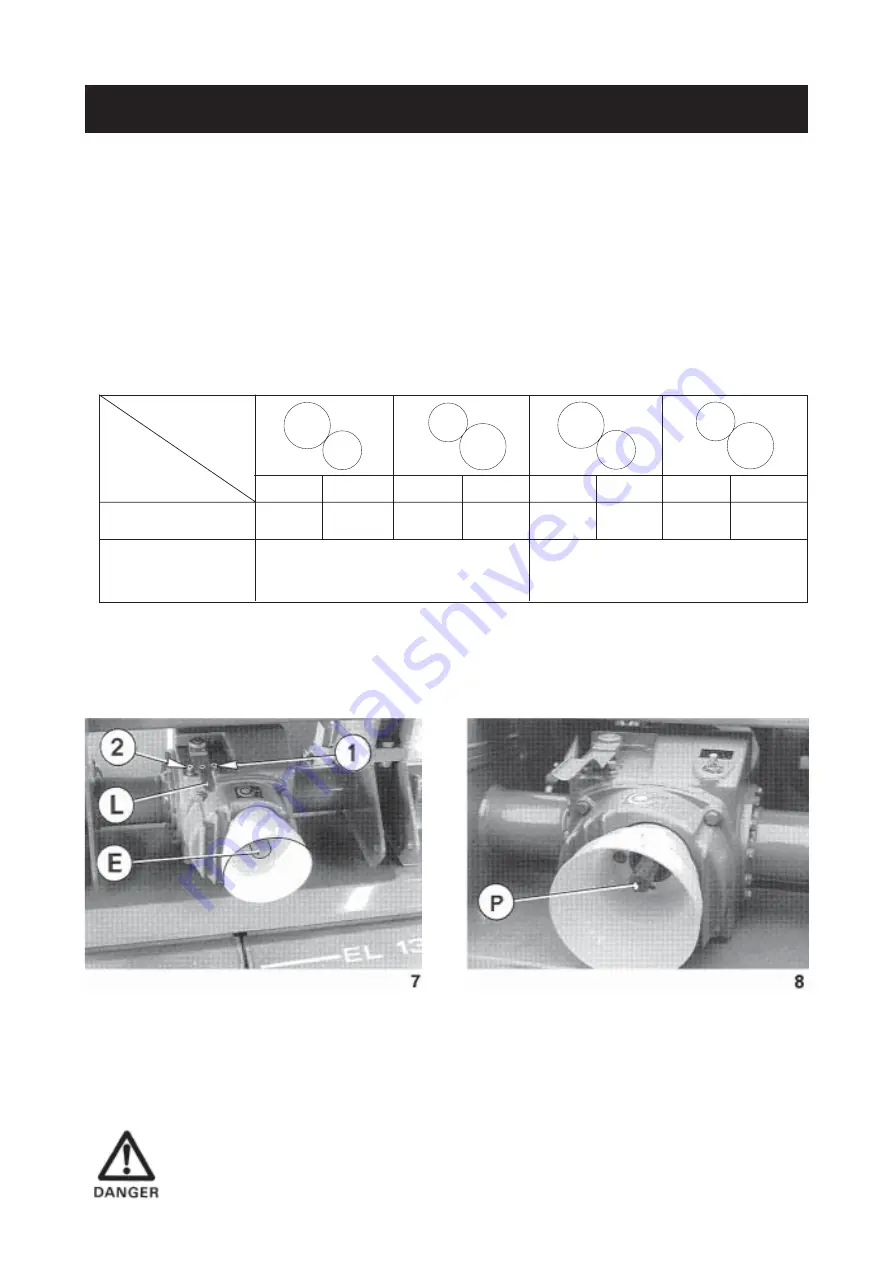
- 15 -
ROTOR SPEEDS
The
EL 131
must only be driven at
1000 rpm PTO speed.
The selector lever (L) (shown in the neutral position on photo 7) associated with invertable gearwheels enables
4 different rotor speeds to be selected (see table 6).
To invert the two gearwheels the machine must be tilted forwards, thus avoiding oil loss.
To do this, proceed as follows :
- Uncouple the PTO shaft.
- Reduce top link length to the minimum.
- Lift the machine to the maximum.
- Remove the gearbox rear cover.
- Invert gearwheels.
POSITION OF
PINIONS
1st
2nd
1st
2nd
1st
2nd
1st
2nd
1 000 rpm
221
269
289
351
187
225
350
422
24 21
26
19
21
24 19
26
Set installed at factory
PTO SPEED
Optional 19/26 teeth
(Set no 123 7420)
6
B
A
= Recommended speeds and fitted as standard for
EL 131 POWER TILLER
with curved blades or with
mulch blades
B
= Recommended speeds and fitted as standard for
EL 131 CULTITILLER
or
CULTIPLOW.
A
SET OF PINIONS
The gearbox is factory fitted with a rear PTO shaft (P) which rotates at the same speed as the tractor PTO shaft
(photo 8). An extra implement can be driven by a secondary PTO shaft which should be assembled and used
according to the legislation in force at the time.
The rear PTO shaft
is 1 3/8" 6 spline profile, and
must not be used to transmit more than 37 kW (50 hp.
It
should not be used with the gears disengaged (neutral) when driving a secondary implement (seed-drill etc.)
as
this could damage the gearbox due to a lack of lubrication.
If the rear PTO shaft is not used, always put cover (E) in place (photo 7).
Summary of Contents for EL 131
Page 1: ...ASSEMBLY OPERATOR S MANUAL EL 131 POWER TILLER CULTITILLER CULTIPLOW N 95454 GB 06 06 96...
Page 10: ...8...
Page 33: ...31...
Page 44: ...N O T E S...
Page 45: ......
Page 46: ......