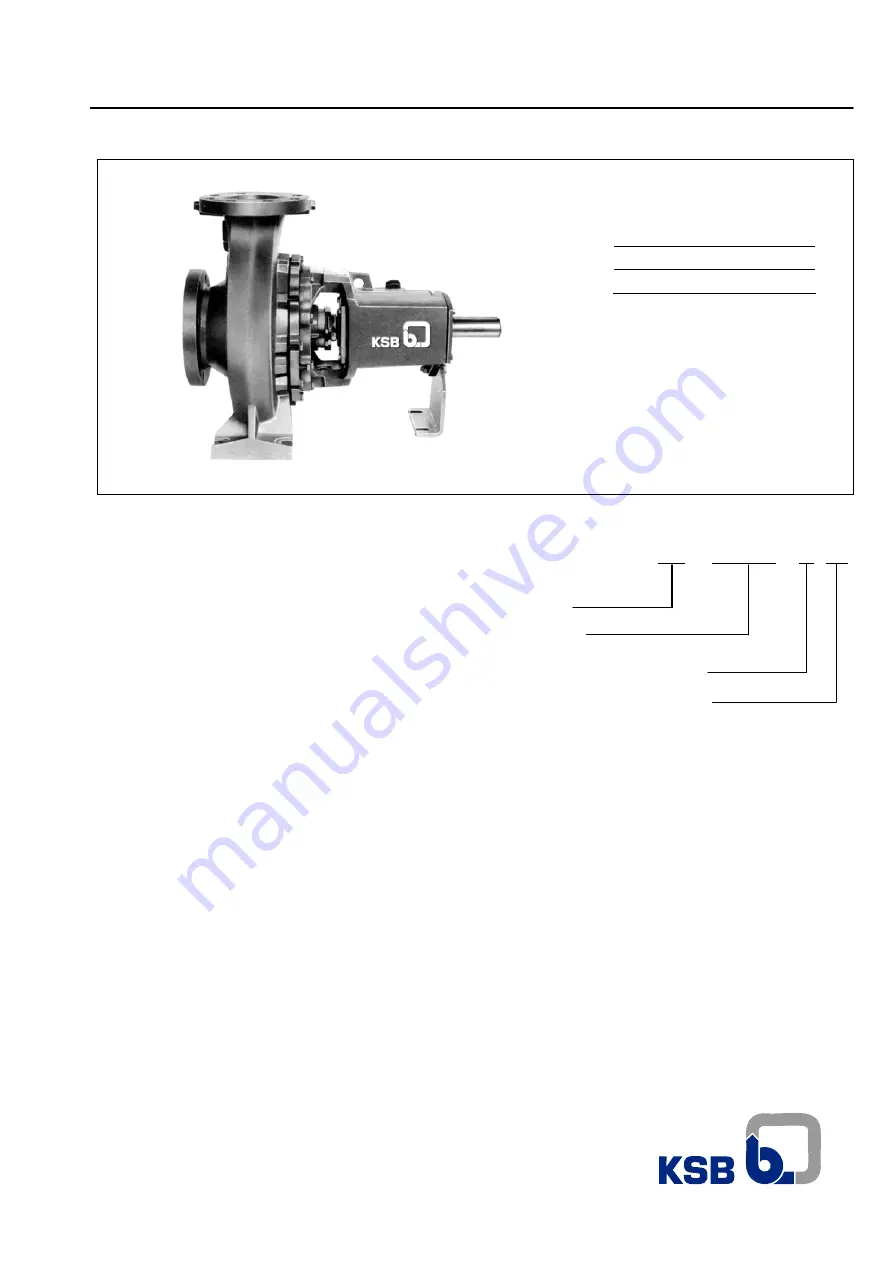
KSB Meganorm
Operating Instructions
Nº A2742.8E/8
1.
Application
The KSB MEGANORM centrifugal pump is suitable for
handling chemical products, aggressive organic and
inorganic liquids, oil, water, condensate and other liquids,
and it is mainly used in the following applications:
-
Sugar and alcohol industry
-
Water
supply
-
Irrigation
-
Air
conditioning
-
Fire
fighting
-
Drainage
2. Design
Horizontal, single-stage, end suction with top centerline
discharge. The “back-pull-out”design allows maintenance
and repair services through the backside, without
dismantling piping supports.
Dimensionally built to ISO 2858/DIN 24256 and
mechanically to ANSI B73.1.
3. Designation
KSB Meganorm 80 - 200
Trade Mark
Model / Type
Discharger Nozzle Diameter (mm)
Nominal Impeller Diameter(mm)
4. Operating data
Sizes
- DN 25 up to 150 ( 1 ¼” to 6’)
Flow
- up to 3,082 gpm (700 m3/h)
Head
- to 460 ft (140 m)
Temperature
- to 221ºF (105º C)
Max. Suction pressure
- to 145 psi (10 bar)
Speed
- to 3,500 rpm
Centrifugal pump for general use
Line :
Mega
Standard :
ISO 2858