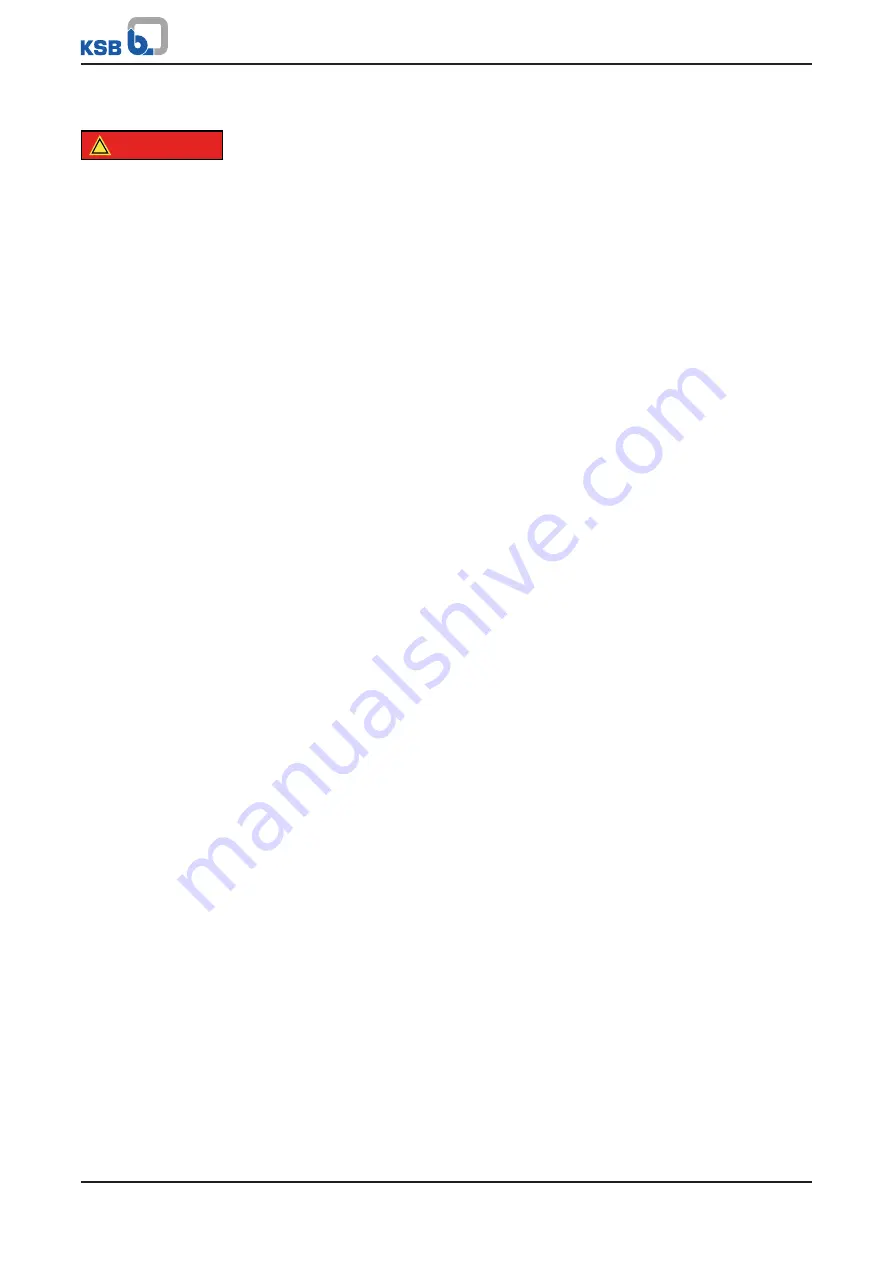
2 Safety
7 of 30
KWT51
1974.95/01-EN
2 Safety
!
DANGER
All the information contained in this section refers to hazardous situations.
In addition to the present general safety information the action-related safety
information given in the other sections must be observed.
2.1 General
▪
This operating manual contains general installation, operating and maintenance
instructions that must be observed to ensure safe operation of the system and
prevent personal injury and damage to property.
▪
Comply with all the safety instructions given in the individual sections of this
operating manual.
▪
The operating manual must be read and understood by the responsible specialist
personnel/operators prior to installation and commissioning.
▪
The contents of this operating manual must be available to the specialist
personnel at the site at all times.
▪
Information and markings attached directly to the product must always be
complied with and kept in a perfectly legible condition at all times. This applies
to, for example:
– Markings for connections
– Name plate
▪
The operator is responsible for ensuring compliance with all local regulations not
taken into account.
2.2 Intended use
▪
Consult the manufacturer about any use or mode of operation not described in
the data sheet or product literature.
▪
This product must only be operated within the limit values stated in the technical
product literature for the ambient temperature, density, pressure, temperature
and in compliance with any other instructions provided in the operating manual
or other applicable documents.
▪
The product must only be operated in the fields of application and within the use
limits specified in the other applicable documents.
2.3 Personnel qualification and training
▪
All personnel involved must be fully qualified to install, operate, maintain and
inspect the product this manual refers to.
▪
The responsibilities, competence and supervision of all personnel involved in
transport, installation, operation, maintenance and inspection must be clearly
defined by the operator.
▪
Deficits in knowledge must be rectified by means of training and instruction
provided by sufficiently trained specialist personnel. If required, the operator can
commission the manufacturer/supplier to train the personnel.
▪
Training on the product must always be supervised by specialist technical
personnel.
2.4 Consequences and risks caused by non-compliance with this manual
▪
Non-compliance with these operating instructions will lead to forfeiture of
warranty cover and of any and all rights to claims for damages.
▪
Non-compliance can, for example, have the following consequences:
– Hazards to persons due to electrical, thermal, mechanical and chemical
effects and explosions
– Failure of important product functions
– Failure of prescribed maintenance and servicing practices