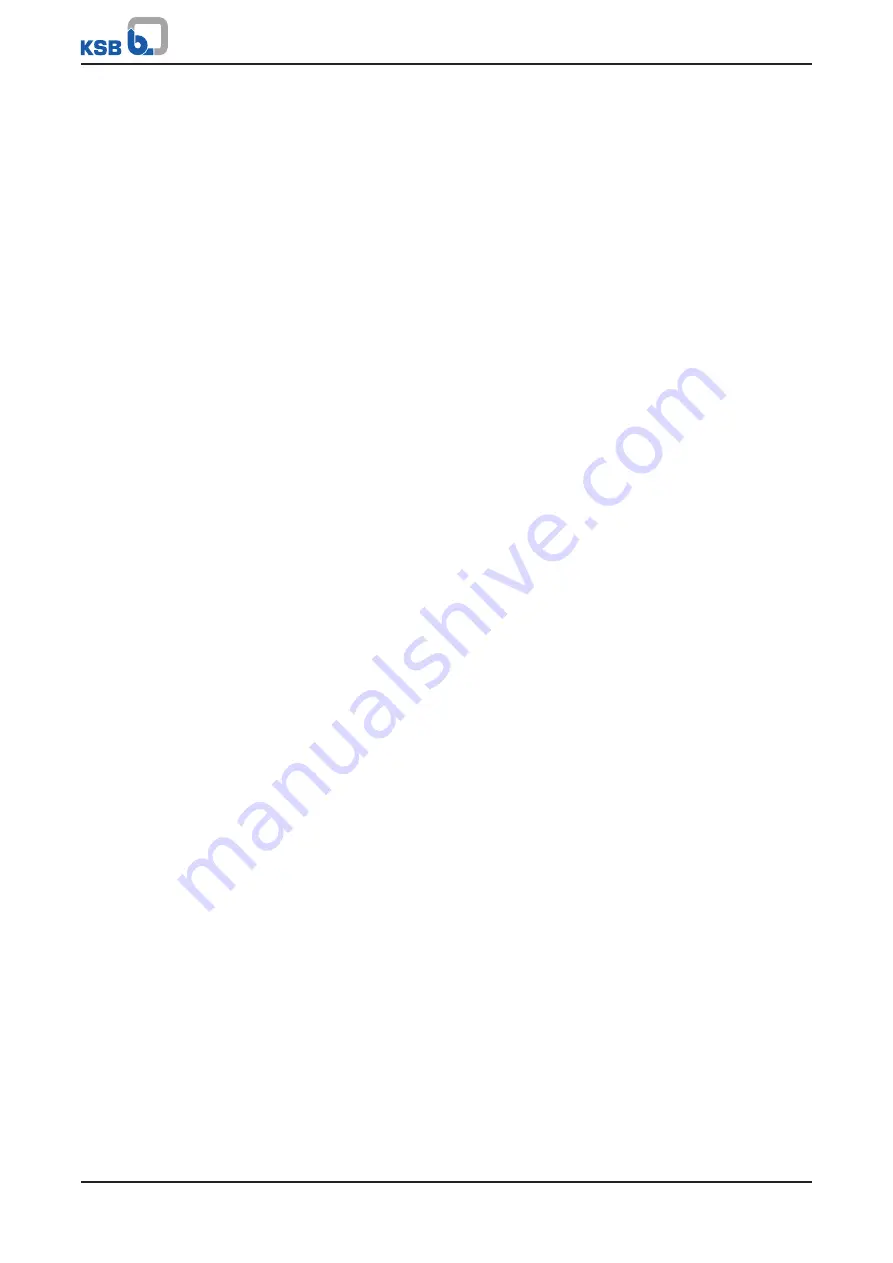
Index
47 of 48
Hya-Duo D FL Compact
Index
A
Applications 8
C
Certificate of Decontamination 45
D
Drive 16
Connecting the dry running protection device 25
Setting the dry running protection device 28
E
Event of damage 6
F
Faults
Frequency of starts 31
Functions
Automatic switchover (duty system and back-up
system) 34
I
K
Key to safety symbols/markings 6
L
LED display 33
List of components 42
M
N
O
Operating modes
Functional check run 33
Manual mode 33
P
Personnel 9
Pump activated 25
Q
R
S
Safety awareness 9
Scope of supply 18
Setting the start-up pressure 28
W
Warranty claims 6