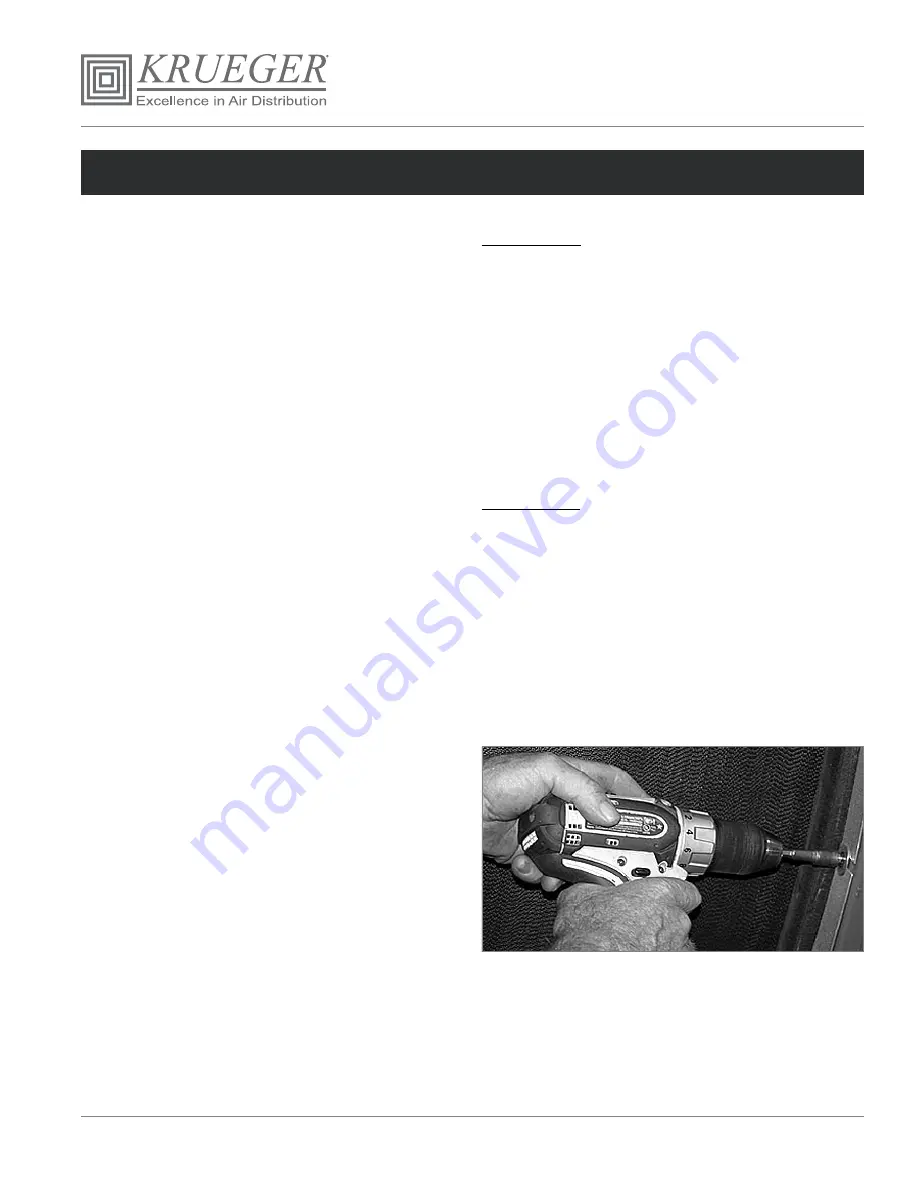
KAH Operation & Maintenance Guide
Page: 55 of 88
Krueger | 1401 N Plano Rd | Richardson, TX 75081 | 972.680.9136 | [email protected] | www.krueger-hvac.com
SECTION 3 - MAINTENANCE (CONTINUED)
THERMOTECH®
Periodic cleaning of the energy recovery wheel will
be a function of the operating schedule, climate, and
contaminates in the indoor air being exhausted and
outdoor air being supplied to the building.
Cleaning the Wheel
The wheel media does not require any cleaning under
normal operating conditions and proper maintenance of the
drive systems and main bearings. The key is to make sure
the wheel is always turning in order to utilize the counter
flow air streams and the purge sector to keep the media
clean. Over the years there might be some accumulation
of dirt on the face of the media, but the inside will remain
clean.
The best method to clean the wheel is to brush the surface
on the air discharge side with the airflow on, or by using a
vacuum cleaner. A 2,300 psi pressure washer can be used
in situations where the media is severely clogged. Care
should be taken to not damage the media face by the full
force of the spray. It is recommended that the pressure
cleaning method is tested on a small area of the media.
Adjusting Air Seals
The seals are set at the factory and should not require
adjustment. If the seals are rubbing on the media face,
due to incorrect installation and other factors, adjust the
seals.
1. Rotate the wheel one full revolution, and determine
where the wheel media face is rubbing on the seal.
2. Working on one seal quadrant at a time, loosen the
seal Tek screws as shown in Figure 66 (right).
3. Move the seal away form the wheel surface until no
more rubbing is noticed.
A typical large diameter wheel will have a flatness variation
of 1/16” from the high to low point of the wheel surface. If
the seals are adjusted correctly, the seal gap will vary that
much as the wheel turns, but the seal should never touch
the wheel surface.
Inspect Wheel Drive Components
Rotor Bearings - The main rotor bearings have been sized
for an L-10 life of a minimum of 25 years; operating 24
hours per day, 7 days a week. The main reason that a
main bearing would fail is lack of lubrication or the existing
grease hardens in the bearing due to evaporation or by
penetration of moisture causing corrosion. The bearings
are filled with grease at the factory or at the time of start-up
to eliminate a future failure.
Add a small amount of grease every six months to
maintain fresh grease on the inside of the bearing. Wipe
off any excess purged grease to avoid it getting blown onto
the wheel surface. All bearings are greased with a Dow
Corning Molycote BR2 Plus Grease, which is available
through most bearing distributors
Drive System - The motor does not require any
maintenance and has permanently lubricated bearings.
The speed reducer is grease lubricated as well and does
not require any maintenance. Life expectancy is in excess
of 10 years.
The drive belt tension does not need any adjustment, due to
the gravity based mounting base used. The B-type V-belts
are installed with a B-437 belt connector manufactured
by FLEXCO. This connector will eventually wear out and
need to be replaced. A typical life span is five to 10 years,
depending on the environmental condition.
FIGURE 66 - LOOSEN SCREWS BEFORE ADJUSTING
SEALS