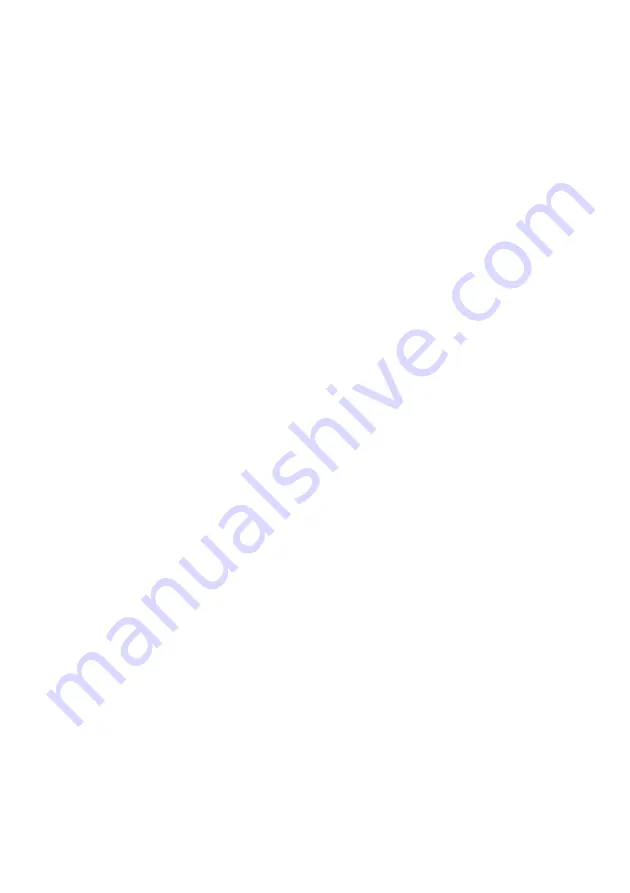
Cutting threads
The integrated electronic and the reversal of the direction
of rotation makes the percussion drill also suitable for cut-
ting threads. The use of machine taps is recommended.
The tap is clamped into the chuck. The electronic controls
are sensitive and should be handled with utmost care to
prevent any breaking of tap – particularly when cutting
threads into blind holes.
The torque required can be selected via the adjusting
wheel in switch (1).
Important! When cutting threads, use low speeds only.
Drill chuck
The drill chuck is tightened with a torque of 30 Nm. Only in
this way is it guaranteed that the chuck does not loosen
itself from the spindle during anticlockwise rotation.
If the chuck is removed from the spindle for replacement
purposes, the new chuck must be tightened with a torque
of at least 30 Nm before restarting the machine.
Before applying a new chuck, the surfaces of both the
chuck and the spindle must be cleaned.
Caution!
Before disassembling and reassembling the drill chuck,
either disconnect the machine from the power supply,
or remove the mains cable (5) from the grip using the
locking device buttons (6).
Caution!
When turning anticlockwise, it is possible that the
chuck loosens itself from the spindle. For this reason
make sure that the chuck sits properly on the spindle.
Operating the quick-change chuck
This chuck has been developed especially for use with
percussion drills.
The fully-automatic spindle locking device enables a quick
and problem-free tool change in the chuck.
The drill spindle will be automatically fixed when the chuck
is actuated.
The chuck has a release safety lock which prevents any
unintentional release of the drilling tool even at high impact
frequencies.
After attaching the jaw chuck to the tool, a slightly higher
torque must be used to engage the clamping force safety
lock. The torsion angle of the collar must be approximately
50° during the locking procedure. After this has been
completed, the tool can be tensioned as usual. Turn the
collar firmly in the “ZU” direction until a click is heard. The
drill is only properly tensioned when the collar has been tur-
ned as far as possible and no more clicking is heard.
Always make sure that the chosen speed is correct for
the purpose for which you are using the machine.
High speeds are necessary for polishing and grinding.
When drilling match speed with type of material and drill.
High speed drilling in steel and stone will cause premature
tool wear.
Use tool steel twist drills for soft materials such as wood
and plastics; carbide-tipped stone drills for stone and con-
crete; high speed twist drills for steel and iron.
Also make sure that, using a gear-rim-chuck, the drill
chuck key is never fastened to the drill with chains,
strings or by similar means. Be sure that the workpiece
cannot be taken along by the drill.
Maintenance
The machine’s motor has life-time lubrication and requires
no special maintenance. However, should you operate the
machine on a continuous basis over long periods of time
we recommend that you send us the machine for thorough
cleaning and an inspection. This will spare you unneces-
sary repair expenses and increase the machine’s service
life. If you always clean the ventilator of dust after each
operation, the motor will enjoy an ever longer service life.
Uniform ventilation is essential for a long service life.
Replacing carbon brushes
Our service personnel will do this and all other servicing
work fast and professionally.
Mains cable
Damaged mains cables must not be used. They are to be
replaced immediately.
Thanks to the innovative mains cable with patent quick-
release lock (5) it is possible for you to replace the cable
with the greatest of ease. Press the two lock pushbuttons
(6) and pull the mains cable (5) out of the casing. Feed the
new mains cable into the hand grip until it snaps in place.
Various cable lengths are available upon request.
Only use the mains cable module for KRESS power
tools! Do not try to operate other power tools with it!
Auxiliary handle (optional accessory)
Guarantees safe, wander-free guidance of the drill, and at
the same time precise adjustment of the drilling depth with
the depth stop.
Tighten the tensioning screw on the auxiliary handle
well. This is the only way to prevent the auxiliary handle
from twisting on the collar or from coming off the unit.
We reserve the right to make alterations resulting from
technical development without prior notice.
Noise/vibration information
Measured values correspond with EN 50144.
Sound pressure level
= 74
+3
dB (A)
Sound power level
= 87
+3
dB (A)
Work place emission value
= 77
+3
dB (A)
Operators require noise protection equipment.
The weighted acceleration is typically 13.2 m/s
2
.
Environmental protection
Kress takes back old machines for resource saving recyc-
ling. Kress machines can very easily be broken down into
their recyclable basic materials. Hand in your old Kress-
machine at a dealer or send it directly to Kress.