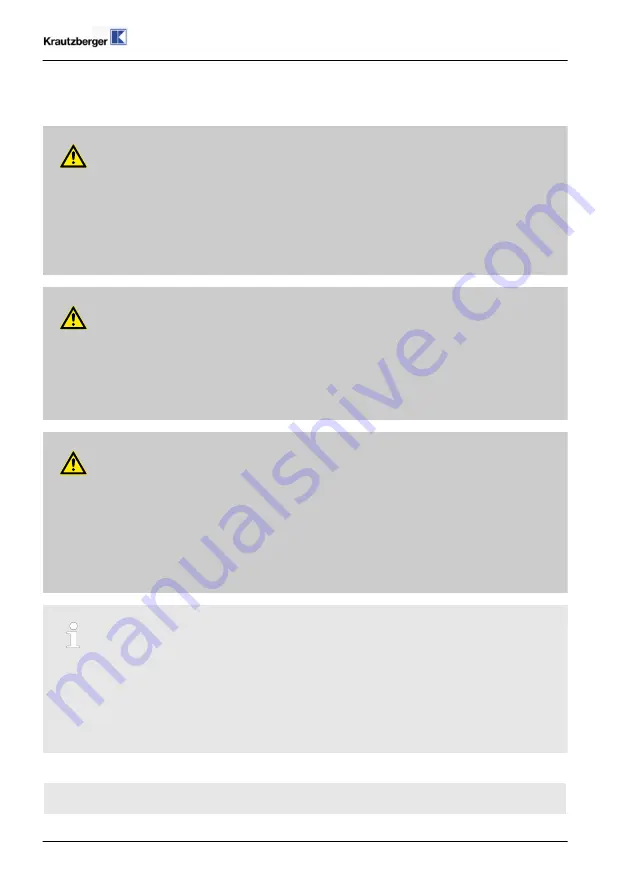
3 Safety and responsibility
3.1 General safety instructions
WARNING!
Life threatening risk of injury or property damage through the application of hazardous
media!
The application of hazardous media can lead to death, serious injuries or property damage.
–
Ensure the resistance of the machine against the medium that is to be applied.
–
Always adhere to the safety data sheet of the medium that is to be applied.
CAUTION!
Risk of injury through compressed air!
Uncontrolled leaks of compressed air can lead to serious injuries!
–
Prior to any work on the device, all compressed-air lines must be closed and bleed if nec-
essary.
WARNING!
Sound pressure level
Depending on the operating conditions, the sound pressure of the device may cause hearing
damage.
Take suitable action to reduce the impact of the existing sound pressure level. The owner is
responsible for the type and implementation of suitable measures, which may depend on the
local conditions.
Outdoor operation and operation in exterior areas!
Use suitable measures to protect the device during the operation from environmental impacts
in an exterior area through:
–
Moisture
–
UV radiation
–
Frost, etc.
3.2 Intended use
The automatic spray gun is used to spray paints, colours, adhesives, glazes, enamels, release
agents, as well as other fluids. The nozzle size depends on the spray viscosity of the spray fluid.
Operating instructions
T-Dok-040-GB-Rev.5
[email protected], www.krautzberger.com
GB–12
Summary of Contents for 200-0148
Page 48: ......