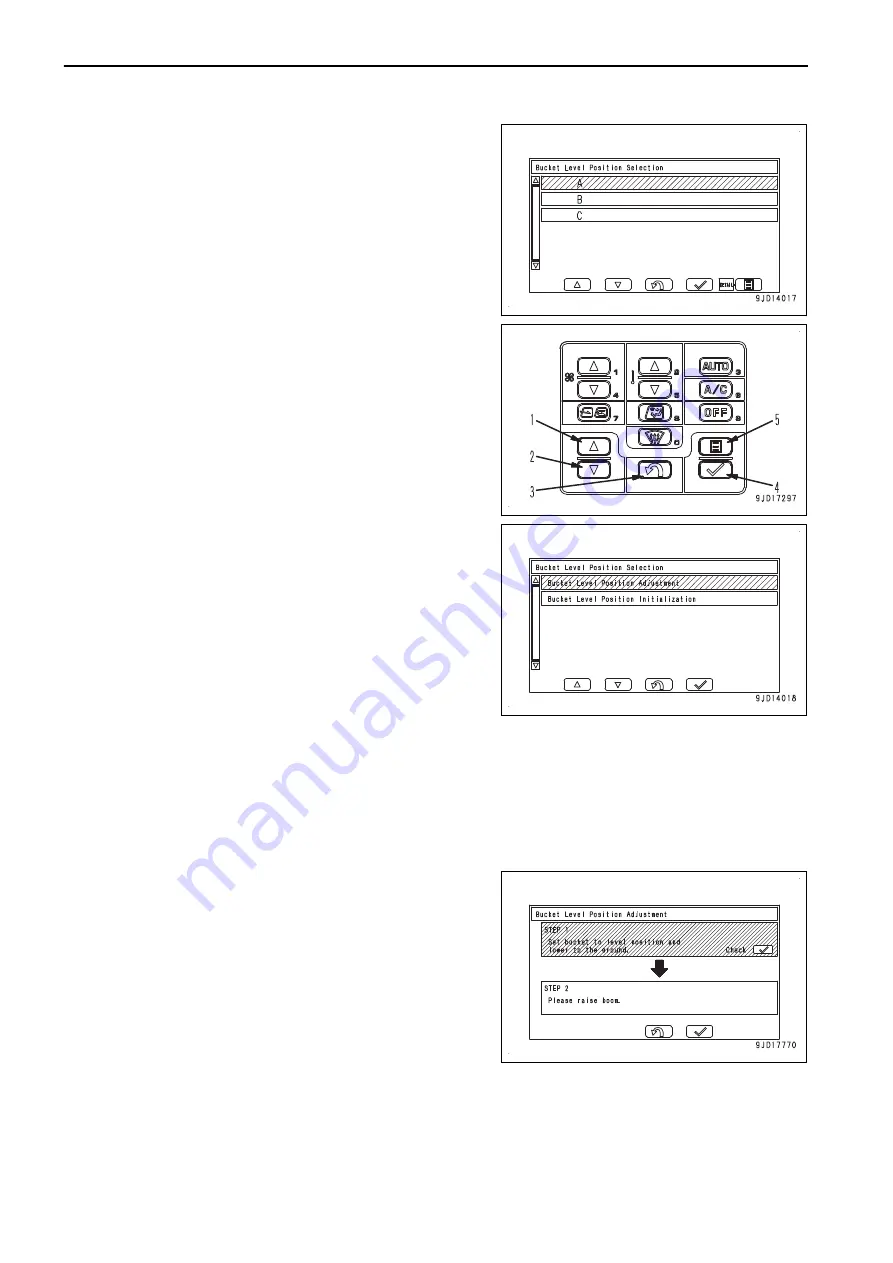
1.
Select a type of bucket whose level position is to be ad-
justed from the “Bucket Level Position Selection” screen,
then press menu switch (5).
2.
“Bucket Level Position Selection” screen is switched.
Select the “Bucket Level Position Adjustment”, press EN-
TER switch (4), and then the adjustment mode starts.
You can perform the following operations with switches (1)
to (4) on the switch panel.
(1) UP switch
Moves to the previous item (1 line above).
When on the first line, it moves to the last line.
(2) DOWN switch
Moves to the next item (1 line below).
When on the last line, it moves to the first line.
(3) RETURN switch
The screen returns to “Bucket Level Position Selection” screen.
(4) ENTER switch
The screen changes to “Bucket Level Position Adjustment”, and then the adjustment mode starts.
3.
According to the screen instructions, set the bucket bottom
horizontal, and lower the boom to the ground.
REMARK
When canceling the adjustment, press RETURN switch
(3).
4.
Press ENTER switch (4).
The screen switches to STEP2.
EXPLANATION OF COMPONENTS
OPERATION
3-74
Summary of Contents for WA600-8
Page 2: ......
Page 8: ...Do not repeatedly handle and lift loads VIBRATION LEVELS FOREWORD 1 6...
Page 20: ......
Page 25: ...LOCATION OF SAFETY LABELS SAFETY SAFETY LABELS 2 5...
Page 68: ......
Page 71: ...CONTROLS AND GAUGES NAMES OPERATION GENERAL VIEW 3 3...
Page 173: ...SWITCHES OPERATION EXPLANATION OF COMPONENTS 3 105...
Page 366: ......
Page 457: ...SPECIFICATIONS 5 1...
Page 461: ...SPECIFICATIONS SPECIFICATIONS 5 5...
Page 462: ......
Page 470: ...SWITCHES HANDLE STEERING WHEEL SPEC MACHINE ATTACHMENTS AND OPTIONS 6 8...
Page 534: ......
Page 535: ...REPLACEMENT PARTS 7 1...
Page 544: ......
Page 553: ......