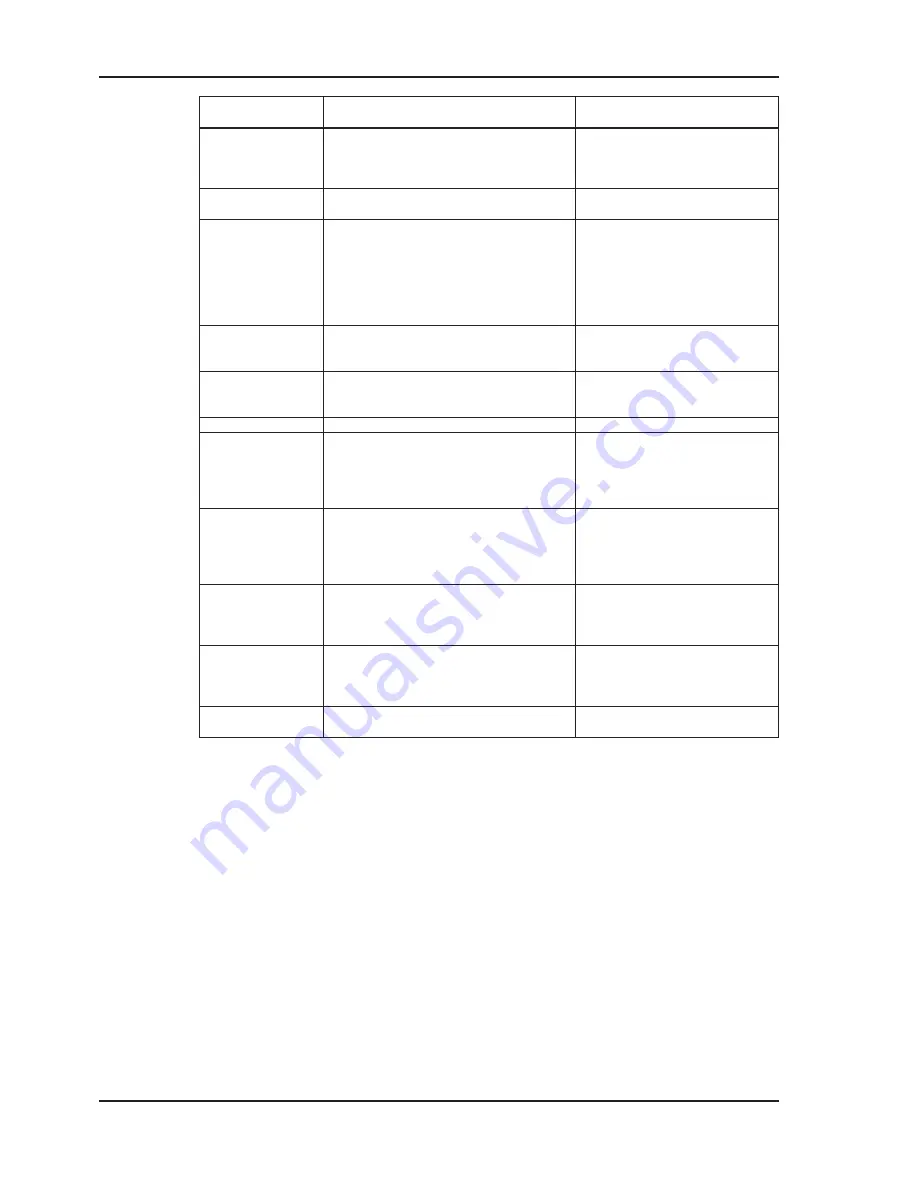
Fault
possible causes
measures to remove the cause of
the fault
F25 message:
Commutation error
— wrong cable
— wrong phasing
— check wiring
— check resolver poles (RESPOLES)
check motor poles (MPOLES)
check offset (MPHASE)
F27 message:
error AS-option
— -AS-24V relay AND hardware enable AND
software enable are active
— check PLC programming and
wiring
motor does not rotate
— servo amplifier not enabled
— break in setpoint cable
— motor phases swapped
— brake not released
— drive is mechanically blocked
— no. of motor poles set incorrectly
— feedback set up incorrectly
— apply enable signal
— check setpoint cable
— correct motor phase sequence
— check brake control
— check mechanism
— set no. of motor poles
— set up feedback correctly
motor oscillates
— gain too high (speed controller)
— shielding in feedback cable has a break
— AGND not wired up
— reduce Kp (speed controller)
— replace feedback cable
— join AGND to CNC-GND
drive reports
following error
— Irms or Ipeak is set to low
— setpoint ramp is too long
— increase Irms or Ipeak
(keep within motor data !)
— shorten setpoint ramp +/-
motor overheating
— Irms/Ipeak set too high
— reduce Irms/Ipeak
drive too soft
— Kp (speed controller) too low
— Tn (speed controller) too high
— PID-T2 too high
— T-Tacho too high
— increase Kp (speed controller)
— use motor default value for
Tn (speed controller)
— reduce PID-T2
— reduce T-Tacho
drive runs
roughly
— Kp (speed controller) too high
— Tn (speed controller) too low
— PID-T2 too low
— T-Tacho too low
— reduce Kp (speed controller)
— use motor default value for
Tn (speed controller)
— increase PID-T2
— increase T-Tacho
axis drifts at
setpoint = 0V
— offset not correctly adjusted for analog
setpoint provision
— AGND not joined to the CNC-GND of the
controls
— adjust setpoint-offset (analog I/O)
— join AGND and CNC-GND
n12 message:
Motor default values
loaded
— Motor number stored in sine encoders
EEPROM different than what drive is
configured for
— If n12 is displayed, default values
for the motor are loaded.
Motor number will be automatically
stored in EEPROM with SAVE.
n14 message:
Wake & shake active
— Wake & shake not executed
— Enable the drive
82
SERVO
STAR
®
601...620 Installation Manual
Appendix
06/02
Seidel