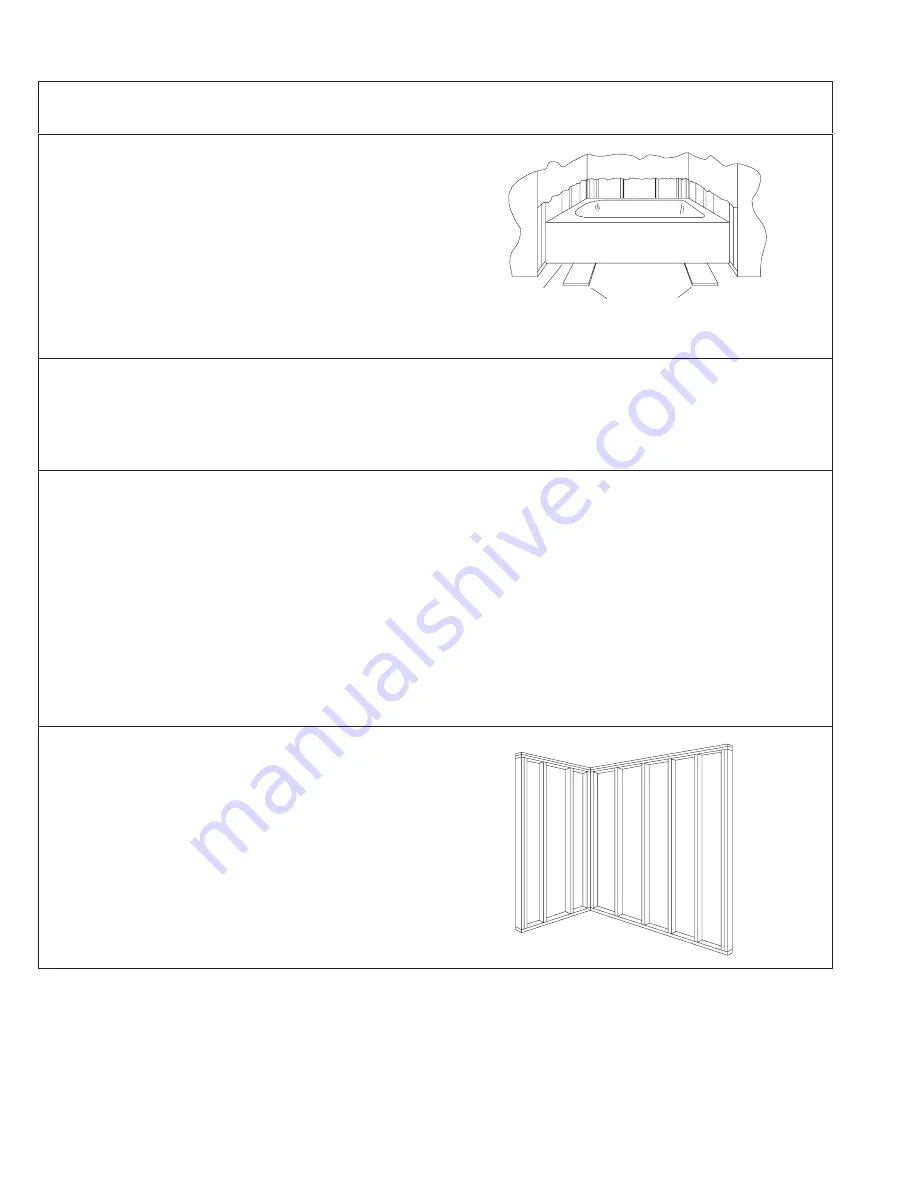
8
111889-
CA
(1093)
Kohler Co., Kohler WI
5. SITE REQUIREMENTS
A. OLD BATH REMOVAL
Disconnect the drain at the trap. Remove old wall
material. Slip boards under old bath feet to protect
floor and slide old bath out of recess as illustrated.
Floor
Protection
Boards
Old Bath
B. SUBFLOOR PREPARATION
Check flooring under the bath and repair if necessary.
Make sure that the subfloor is level. Seal subfloor to
reduce the risk of water damage.
C. STUD POCKET PREPARATION
Construct a recess designed for your particular
installation. Framing is of 2 x 4 construction. When
constructing framing, allow for thickness of sub and
finished wall materials.
If an apron wall without a ledge is desired, the finished
apron wall surface must be 1/32” under the bath rim.
Bath can be installed as a corner, recess or sunken
installation. Possible studding arrangements are
illustrated in 1. through 3. below; modifications may be
needed for other types of construction.
1.
Corner Installation: Suggested stud construction
is illustrated.