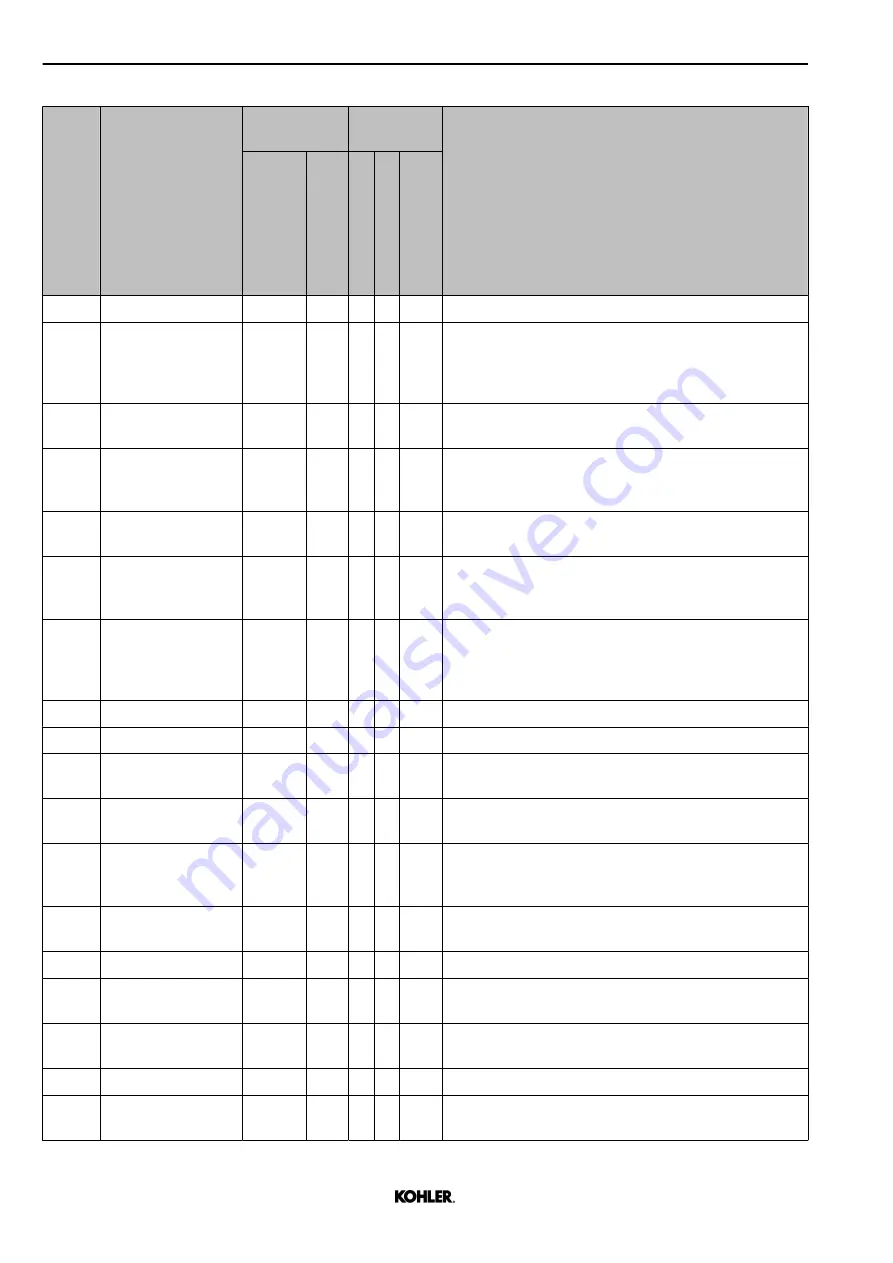
Maintenance
Inspection and maintenance schedules
Task iden
tification
Component
Schedule
Service
Type
Task description
Time limit (h)
Calendar limit (y
ear)
R
eplacemen
t
Ov
erhaul
Inspection/Clean R
epair
/Adjus
tmen
t
SL205
Fuel injectors
7500
8Y
X
Replace.
SL206 Combustion cham‐
bers
7500
8Y
X
Done at the time the injectors are replaced. Use a
borescope to identify condition of combustion
chamber (piston crown, liner hatches, fire deck,
etc.).
SL2-13
40
Torsional vibration
damper
4000
X
Replace.
SL2-13
45
Silicon oil of
torsional vibration
damper
1000
1Y
X
Collect and send silicon oil sample for analysis.
SL209 HP fuel pump and
LP fuel pump
-
8Y
X
Inspect for leaks. Replace pump if necessary.
SL212
Cold start oil
cooler by-pass
valve
7500
18Y X
Replace.
SL213 Exhaust gas turbo‐
chargers
7500
18Y X
Check overall condition (compressor blades, leaks,
connections, housings, etc.) every 4000 hours.
Replace the exhaust gas turbocharger at the indi‐
cated service interval.
SL215
LT coolant pump
7500
18Y X
Replace.
SL216
HT coolant pump
7500
18Y X
Replace.
SL217
Coolant thermo‐
stats
7500
18Y X
Replace.
SL218 Auxiliary belt drive
- PTO
7500
18Y X
Replace.
SL219
Rubber sleeves
7500
18Y X
Replace all rubber hose connections on the engine:
e.g., coolant hoses for ECU cooling, hose connec‐
tions for crankcase ventilation.
SL220
Charge air cooler
7500
18Y
X
Check visually for leaks. If shown, identify reason.
Replace component if needed.
SL221
Oil cooler
7500
18Y
X
Inspect the oil cooler.
SL222
Recommended:
Starter
7500
18Y
X
Inspect the starter (winding insulation, relay, condi‐
tion of the gear teeth, etc.).
SL223
Battery charging
alternator
7500
18Y X
Replace.
SL224
Cylinder heads
7500
18Y X X
Replace.
SL2-53
30
Diesel exhaust
fluid injectors
5000
-
X
Replace.
92
© 2022 by Kohler Co. All rights reserved.
KD62V12 33521030301_8_1 EN_US 2022-09