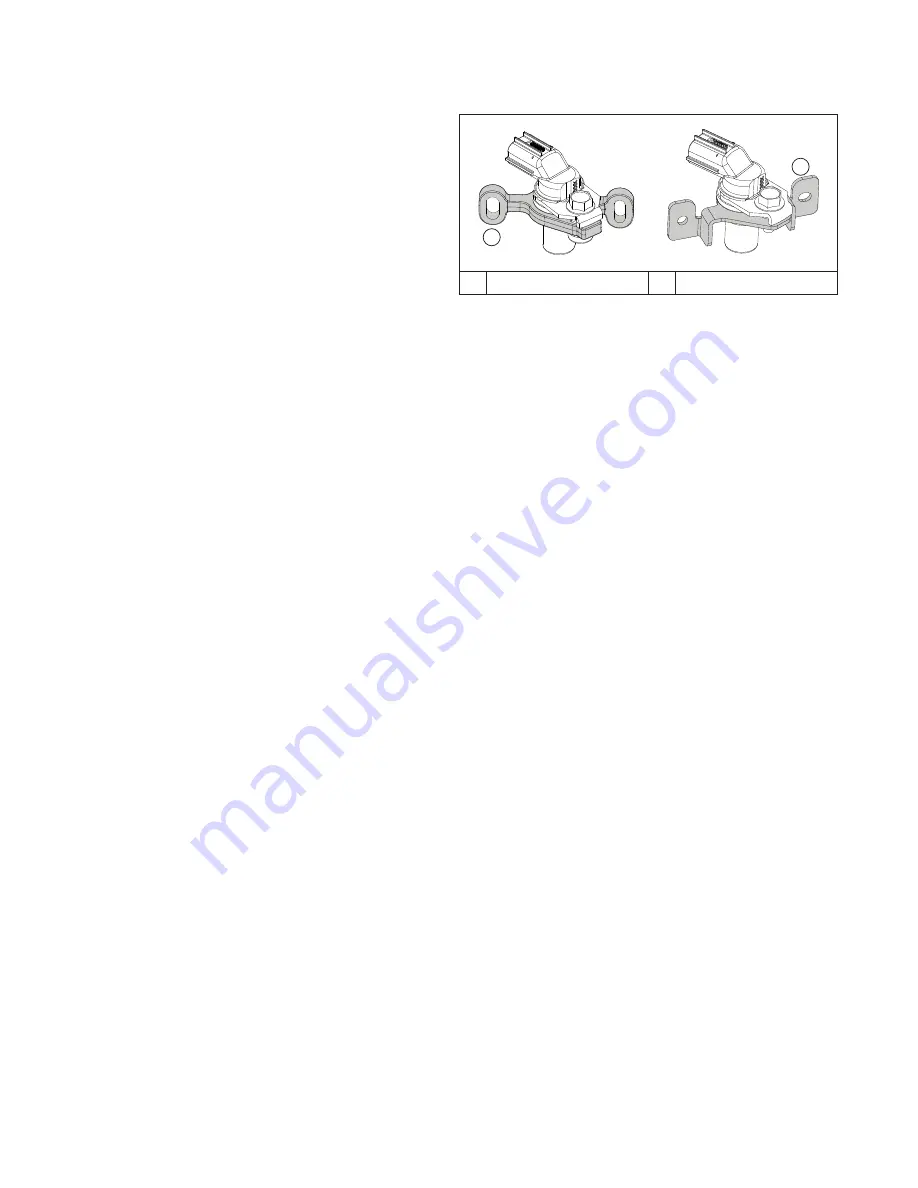
Propane EFI System
22
24 690 31 Rev. D
KohlerEngines.com
ECU compares input signals to programmed maps in
its memory to determine appropriate fuel and spark
requirements for immediate operating conditions. ECU
then sends output signals to set injector duration and
ignition timing.
ECU continually performs a diagnostic check of itself,
each of sensors, and system performance. If a fault
is detected, ECU can turn on a Malfunction Indicator
Light (MIL) (if equipped) on equipment control panel,
store fault code in its fault memory, and go into a default
operating mode. Depending on signifi cance or severity
of fault, normal operation may continue. A technician can
access stored fault code using a blink code diagnosis
fl ashed out through MIL. An optional computer software
diagnostic program is also available, see Tools and Aids.
ECU requires a minimum of 6.0 volts to operate.
To prevent engine over-speed and possible failure, a
rev-limiting feature is programmed into ECU. If maximum
RPM limit (4500) is exceeded, ECU suppresses injection
signals, cutting off fuel fl ow. This process repeats itself in
rapid succession, limiting operation to preset maximum.
Wiring harness used in EFI system connects electrical
components, providing current and ground paths for
system to operate. All input and output signaling occurs
through two special all weather connectors that attach
and lock to ECU. Connectors are Black and Grey and
keyed diff erently to prevent being attached to ECU
incorrectly.
Condition of wiring, connectors, and terminal
connections is essential to system function and
performance. Corrosion, moisture, and poor connections
are as likely cause of operating problems and system
errors as an actual component. Refer to Electrical
System for additional information.
EFI system is a 12 VDC negative ground system,
designed to operate down to a minimum of 6.0 volts.
If system voltage drops below this level, operation of
voltage sensitive components such as ECU, lock-off
valve, ignition coils, and injectors will be intermittent or
disrupted, causing erratic operation or hard starting.
A fully charged, 12 volt battery with a minimum of 350
cold cranking amps is important in maintaining steady
and reliable system operation. Battery condition and
state of charge should always be checked fi rst when
troubleshooting an operational problem.
Keep in mind that EFI-related problems are often caused
by wiring harness or connections. Even small amounts
of corrosion or oxidation on terminals can interfere with
milliamp currents used in system operation.
Cleaning connectors and grounds will solve problems
in many cases. In an emergency situation, simply
disconnecting and reconnecting connectors may clean
up contacts enough to restore operation, at least
temporarily.
If a fault code indicates a problem with an electrical
component, disconnect ECU connector and test for
continuity between component connector terminals and
corresponding terminals in ECU connector using an
ohmmeter. Little or no resistance should be measured,
indicating that wiring of that particular circuit is OK.
Crankshaft Position Sensor Bracket
B
A
A
Earlier Design Bracket
B
Later Design Bracket
Crankshaft position sensor is essential to engine
operation; constantly monitoring rotation and speed
(RPM) of crankshaft. There are 23 consecutive teeth
cast into fl ywheel. One tooth is missing and is used
to reference crankshaft position for ECU. Inductive
crankshaft position sensor with earlier design bracket is
mounted 0.20-0.70 mm (0.008-0.027 in.) from fl ywheel.
Later design bracket requires no adjustment.
During rotation, an AC voltage pulse is created within
sensor for each passing tooth. ECU calculates engine
speed from time interval between consecutive pulses.
gap from missing tooth creates an interrupted input
signal, corresponding to specifi c crankshaft position near
BDC for cylinder #1. This signal serves as a reference
for control of ignition timing by ECU. Synchronization of
inductive speed pickup and crankshaft position takes
place during fi rst two revolutions each time engine is
started. Sensor must be properly connected at all times.
If sensor becomes disconnected for any reason, engine
will quit running.
Throttle position sensor (TPS) is used to indicate throttle
plate angle to ECU. Since throttle (by way of governor)
reacts to engine load, angle of throttle plate is directly
related to load on engine.
Mounted on throttle body and operated directly off end
of throttle shaft, TPS works as a potentiometer, varying
voltage signal to ECU in direct correlation to angle
of throttle plate. This signal, along with other sensor
signals, is processed by ECU and compared to internal
preprogrammed maps to determine required fuel and
ignition settings for amount of load.
Correct position of TPS is established and set at factory.
Do not loosen TPS or alter mounting position unless
absolutely required by fault code diagnosis. If TPS
is loosened or repositioned, appropriate TPS Learn
Procedure must be performed to re-establish baseline
relationship between ECU and TPS.
Engine (oil) temperature sensor is used by system to
help determine fuel requirements for starting (a cold
engine needs more fuel than one at or near operating
temperature).
Mounted in breather cover, it has a temperature-
sensitive resistor that extends into oil fl ow. Resistance
changes with oil temperature, altering voltage sent
to ECU. Using a table stored in its memory, ECU
correlates voltage drop to a specifi c temperature. Using
fuel delivery maps, ECU then knows how much fuel is
required for starting at that temperature.