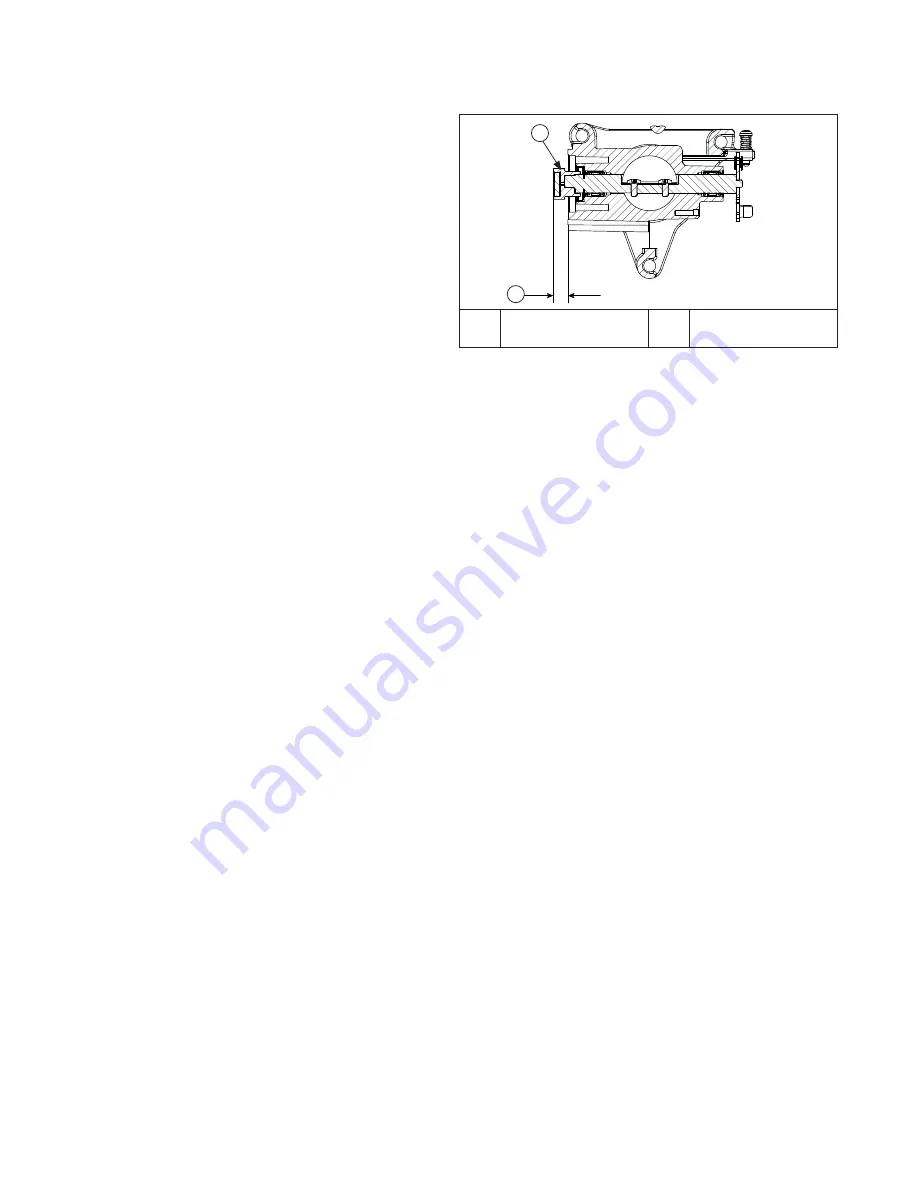
Propane EFI System
32
24 690 31 Rev. D
KohlerEngines.com
7. Remove two mounting screws from TPS. Save
screws for reuse. Remove and discard faulty TPS.
Install replacement TPS and secure with original
mounting screws.
a. Reconnect Black and TPS connector plugs.
b. Perform TPS Learn Procedure integrating new
sensor to ECU.
Contactless (Magnet) Type TPS
TPS is a sealed, non-serviceable assembly. If diagnosis
indicates a bad sensor, complete replacement is
necessary. Magnet that sensor detects is separate, and
can be replaced or reused. If a blink code indicates a
problem with TPS, it can be tested as follows:
Diagnostics of sensor: ECU will still have electrical faults
captured in fault codes: P0122 & P0123. These electrical
faults still have same meaning as with prior sensor,
P0122 detecting low voltage, open circuit, and P0123 for
high voltage conditions between ECU, wire harness, and
sensor. Tip: when working with any electrical connection,
remember to keep connections clean & dry. This is best
accomplished by cleaning connection thoroughly prior
to disassembly. Contaminated sensor connections can
cause premature engine faults. Functionally testing
sensor can no longer be done with simple resistance
checks. If either of these two faults is present or a TPS
fault is suspected, recommended diagnostic test is as
follows:
If a computer with diagnostic software is available
Observe throttle percent and raw TPS values through
diagnostic software. With diagnostic software
communicating to ECU and key ON engine not running,
these values can be observed while throttle is moved
from closed to full open position. There should be a
smooth and repeatable throttle percent value starting
at closed position reading between 0 (about 6.5%) to
WOT position reading 93 (100%). If one of these values
is outside of specifi ed range and output transitions in a
smooth manner, reset ECU and run test again. Since
there is no longer any wear elements inside sensor, most
likely faults will be in electrical connections between
sensor and wire harness and wire harness to ECU. With
service software communicating to ECU and engine not
running, a small load or gentle back and forth motion can
be applied to connectors or wires just outside connectors
to detect a faulty connection.
I
f only a volt meter is available
Measure voltage supply to sensor from ECU. This
voltage should be 5.00 +/- 0.20 volts. This can be
measured by gently probing terminals B & C on harness
side with TPS connector removed from TPS and key
ON. This will generate a P0122 fault that can be cleared
with an ECU reset. If voltage is low, battery, harness and
ECU should be investigated. If supply voltage is good,
plug sensor back into harness. Probe sensor signal
wire with volt meter, terminal A at TPS or pin Black 12
at ECU. This signal should start between 0.6-1.2 volts
at low idle and grow smoothly as throttle is opened to
4.3-4.8 volts at full open (WOT). Since there is no longer
any wear elements inside sensor, most likely faults will
be in electrical connections between sensor and wire
harness and wire harness to ECU.
Replace Magnet Assembly
A
B
A
Magnet Assembly
B
Magnet Installation
Depth
Magnet assembly is captured in a small plastic housing
that is press fi t to end of throttle shaft. This generally
does not need replacement. If replacement is required,
can be replaced as follows:
1. Remove sensor from throttle body, exposing round
magnet assembly.
2. A pair of fl at blade screw drivers or a spanner tool
can be used to pry this off shaft. Caution should be
used to avoid damage to machined fl at surface that
sensor seals against. Also, make sure throttle blade
is in full open position to avoid driving throttle blade
into throttle bore causing damage to blade and/or
bore.
3. When replacing magnet assembly, alignment is
critical. There is a D-shaped drive feature on end of
shaft and a matching pocket in magnet assembly.
On outer diameter of magnet assembly is a notch
that aligns with center of fl at feature of D. Align this
notch and fl at of D feature in shaft and preassemble
parts.
4. With throttle blade in full open position (WOT), press
magnet assembly fully on to throttle shaft. Full
insertion can be checked by measuring height from
throttle body sensor mounting face to end of magnet
assembly. This should be no more than 8.6 mm
(0.338 in.). Installation process requires signifi cant
force, so take care that all parts are aligned. Tapping
magnet assembly on can fracture/damage brittle
magnet within assembly and throttle body assembly
and is NOT RECOMMENDED.