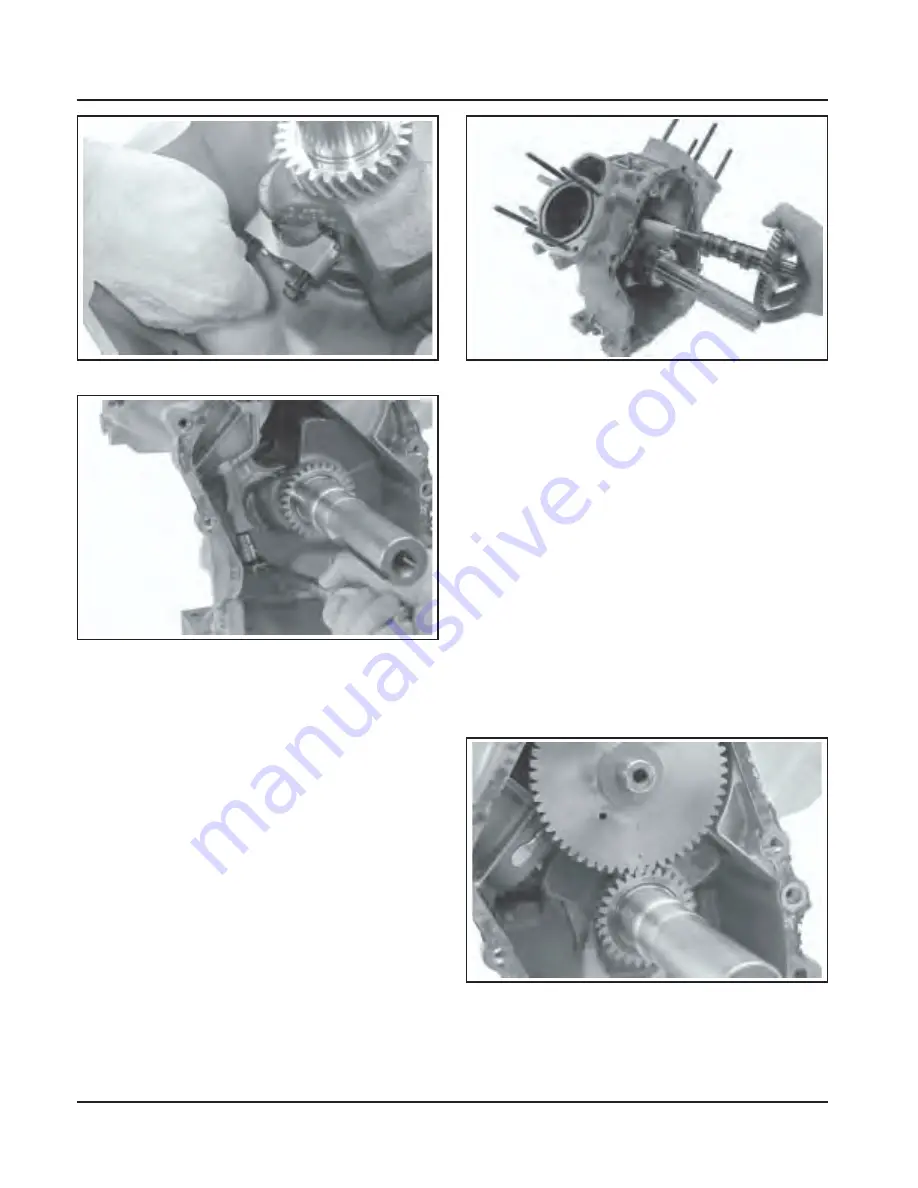
11.4
Section 11
Reassembly
Figure 11-8. Attaching #1 Rod Cap.
Figure 11-9. Torquing #1 Rod Cap.
NOTE:
Make sure to align the chamfer of the
connecting rod with the chamfer of its
mating end cap. When installed, the flat
faces of the connecting rods should face
each other. The faces with the raised rib
should be toward the outside.
6. Repeat the above procedure for the other
connecting rod and piston assembly.
Install Camshaft
1. Inspect the edges of the camshaft keyway, make
sure they are not nicked or burred. Install the seal
protector sleeve tool (SPX Tool No. KO1070) to
prevent damaging the seal lips, or dislodging inner
spring when the camshaft is installed. Cellophane
tape over the keyway is also recommended. See
Figure 11-10.
Figure 11-10. Installing Camshaft using Seal
Protector.
2. Lubricate the camshaft bearing surfaces of the
crankcase and camshaft with engine oil. Apply a
small amount of grease to the lips of the oil seal.
3. Rotate the crankshaft and position the timing mark
of the crankshaft gear at the 12 o'clock position.
4. Turn the governor cross shaft clockwise until the
lower end of shaft contacts the crankcase (#1 side).
Make sure the cross shaft remains in this position
while installing the camshaft.
5. Slide the camshaft into the bearing surface of the
crankcase, positioning the timing mark of the
camshaft gear at the 6 o'clock position. Make sure
that the camshaft gear and crankshaft gear mesh,
and the timing marks are aligned. See Figure 11-11.
Figure 11-11. Timing Marks Aligned.
Not For Resale
www.SmallEngineDiscount.com