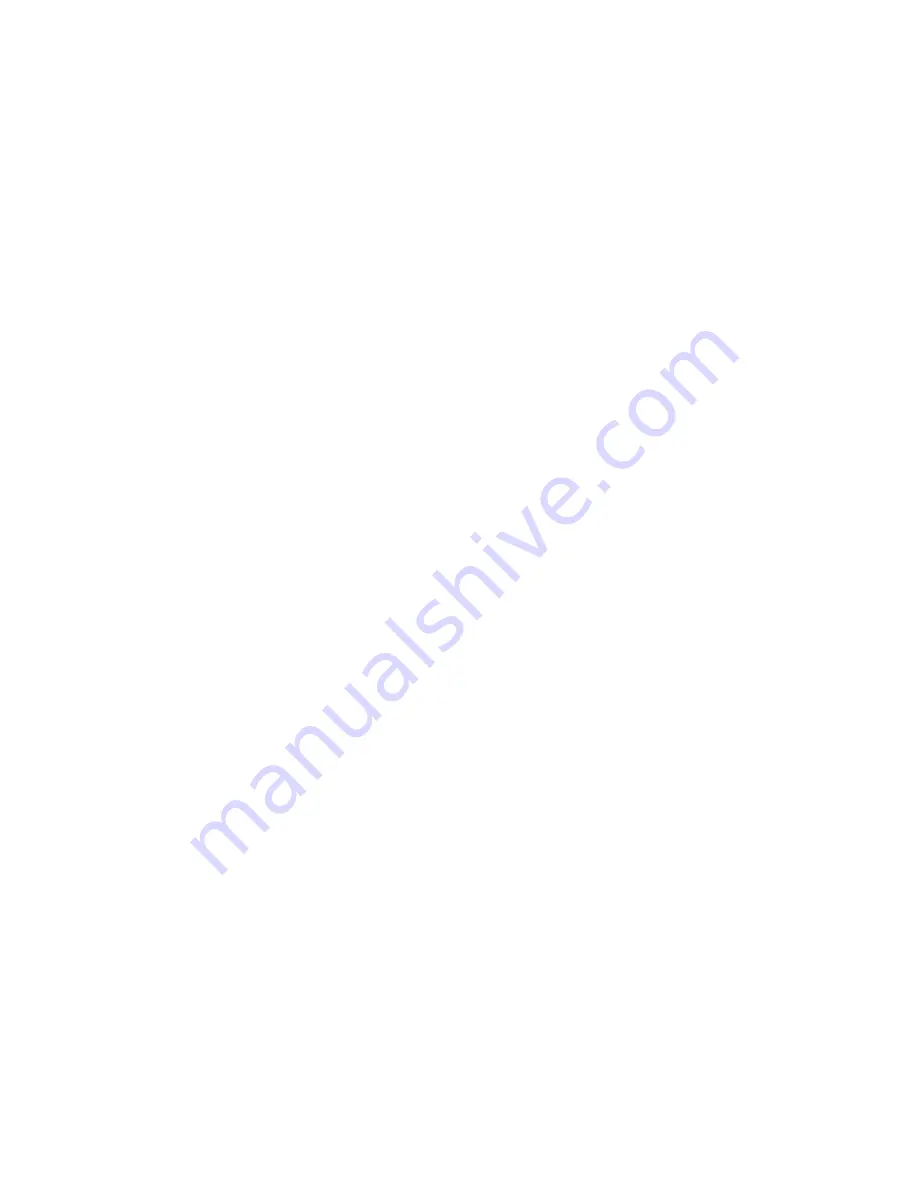
29
EFI System
66 690 14 Rev. A
KohlerEngines.com
Oxygen sensor functions like a small battery, generating
a voltage signal to ECU based upon di
ff
erence in oxygen
content between exhaust gas and ambient air.
Tip of sensor, protruding into exhaust gas, is hollow.
Outer portion of tip is surrounded by exhaust gas, with
inner portion exposed to ambient air. When oxygen
concentration on one side of tip is di
ff
erent than that of
other side, a voltage signal up to 1.0 volt is generated
and sent to ECU. Voltage signal tells ECU if engine is
straying from ideal fuel mixture, and ECU then adjusts
injector pulse accordingly.
Oxygen sensor functions after being heated to a
minimum of 375°C (709°F). A heater inside sensor heats
electrode to optimum temperature in about 10 seconds.
Oxygen sensor receives ground through wire, eliminating
need for proper grounding through mu
ffl
er. If problems
indicate a bad oxygen sensor, check all connections and
wire harness. Oxygen sensor can also be contaminated
by leaded fuel, certain RTV and/or other silicone
compounds, fuel injector cleaners, etc. Use only those
products indicated as O2 Sensor Safe.
Electrical relay is used to supply power to fuel pump.
When key switch is turned ON and all safety switch
requirements met, relay provides 12 volts to fuel pump
circuit. Fuel pump circuit is continuously grounded, so
pump is immediately activated and pressurizes system.
Fuel injectors mount into throttle body/intake manifold,
and fuel rail attaches to them at top end. Replaceable
O-rings on both ends of injector prevent external fuel
leakage and also insulate it from heat and vibration. A
special clip connects each injector to fuel rail and holds it
in place. O-rings and retaining clip must be replaced any
time fuel injector is separated from its normal mounting
position.
When key switch is on and relay is closed, fuel rail
will pressurize, and voltage is present at injector.
At proper instant, ECU completes ground circuit,
energizing injector. Valve needle in injector is opened
electromagnetically, and pressure in fuel rail forces fuel
down through inside. Director plate at tip of injector
contains a series of calibrated openings which directs
fuel into manifold in a cone-shaped spray pattern.
Injectors have sequential fueling that open and close
once every other crankshaft revolution. Amount of fuel
injected is controlled by ECU and determined by length
of time valve needle is held open, also referred to as
injection duration or pulse width. Time injector is open
(milliseconds) may vary in duration depending on speed
and load requirements of engine.
A high-voltage, solid-state, battery ignition system is
used with EFI system. ECU controls ignition output and
timing through transistorized control of primary current
delivered to coils. Based on input from crankshaft
position sensor, ECU determines correct
fi
ring point
for speed at which engine is running. At proper instant,
it interrupts
fl
ow of primary current in coil, causing
electromagnetic
fl
ux
fi
eld to collapse. Flux collapse
induces an instantaneous high voltage in coil secondary
which is strong enough to bridge gap on spark plug.
Each coil
fi
res every other revolution.
EFI engines are equipped with a 25 amp charging
system to accommodate combined electrical demands
of ignition system and speci
fi
c application. Charging
system troubleshooting information is provided in
Electrical System.
An electric fuel pump is used to transfer fuel in EFI
system. Pump is in fuel line near tank. Pumps are rated
for a minimum output of 25 liters per hour at 39 psi.
Pumps have an internal 60-micron
fi
lter. In-line pump
systems may also have a
fi
lter between tank and pump
on pickup/low pressure side.
When key switch is turned ON and all safety switch
requirements are met, ECU, through relay activates
fuel pump, which pressurizes system for start-up. If key
switch is not promptly turned to start position, engine
fails to start, or engine is stopped with key switch ON
(as in case of an accident), ECU switches o
ff
pump
preventing continued delivery of fuel. In this situation,
MIL will go on, but it will go back o
ff
after 4 cranking
revolutions if system function is OK. Once engine is
running, fuel pump remains on.
Fuel pressure regulator assembly maintains required
operating system pressure of 39 psi ± 3. A rubber-
fi
ber diaphragm divides regulator into two separate
sections; fuel chamber and pressure regulating chamber.
Pressure regulating spring presses against valve holder
(part of diaphragm), pressing valve against valve seat.
Combination of atmospheric pressure and regulating
spring tension equals desired operating pressure. Any
time fuel pressure against bottom of diaphragm exceeds
desired (top) pressure, valve opens, relieving excess
pressure, returning excess fuel back to tank.
Fuel rail is an assembly of hoses, injector caps and a
fuel connector. Fuel rail feeds fuel to top of injectors
through injector caps. Caps are fastened to intake
manifold and injectors are locked into place. A small
retaining clip provides a secondary lock.
Fuel rail assembly is serviced as a complete assembly to
prevent tampering and safety hazards. Components are
not individually serviceable.
This EFI engine is equipped with an engine mounted
purge port on #2 upper radiator support bracket. This
capped purge port can be used by OEM to vent fuel
tanks or used in conjunction with a carbon canister kit
for Tier III evaporative emissions compliance. Purge
port connects to vent hose assembly and directs all fuel
vapor into throttle body. If purge port remains unused,
port must remain capped to prevent dirt from entering
engine.
EFI engines have no carburetor, so throttle function
(regulate incoming combustion air
fl
ow) is incorporated in
intake manifold assembly. Manifold consists of a one-
piece aluminum casting which also provides mounting
for fuel injectors, throttle position sensor, fuel rail, air
ba
ffl
e, idle speed screw, and air cleaner assembly.