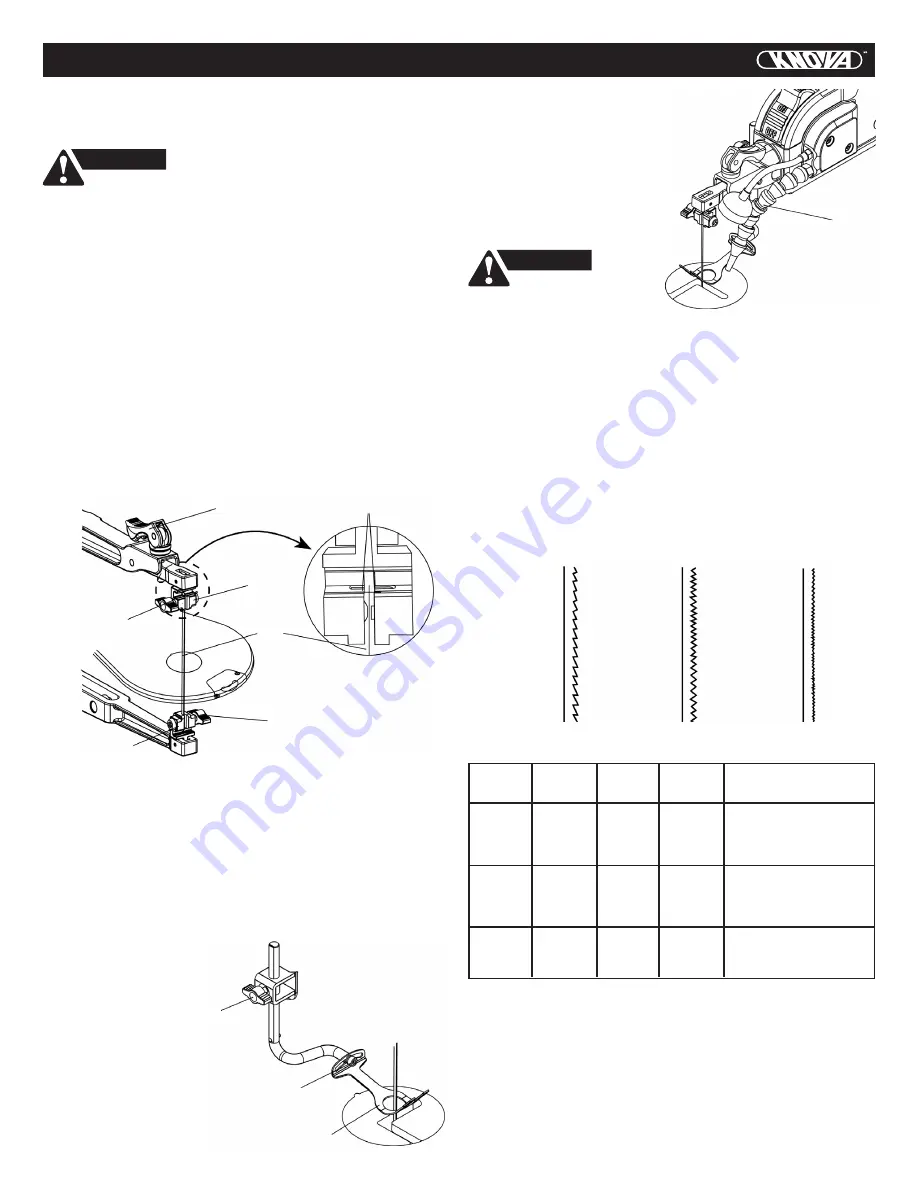
ASSEMBLY AND ADJUSTMENTS
10
Pin-end blade installation (Fig. H, L)
NOTE:
Do not tighten the blade holder lock knobs when using
pin-end blades.
WARNING
In order to avoid uncontrollable lifting of
the workpiece, the teeth of blade should always
point downward.
1. To install a new 5 in. pin-end blade, first insert the blade
into the lower blade holder (7), making sure the pins are
properly located in the slots (see Fig. L-2). Then place
the blade into the slot in upper blade holder (4). (Fig. L)
2. Tighten the upper (4) and lower (6) blade holder lock knob.
3. To tension the blade (9), lower the blade tension lever (2).
Check the tension on the blade. If tension is too tight,
turn the blade tension lever (2) counterclockwise.
If tension is too loose, turn the blade tension lever
clockwise.
NOTE:
If the blade is over tightened, the lever will be
difficult to lower and could result in damage to the blade
holder or arm assembly.
4. Tilt the table back to the 0° bevel setting and lock the table
lock knob (8). (Fig. H)
5. Replace the table insert, making sure it is not above
the worktable surface.
BLADE GUARD FOOT ADJUSTMENT (FIG. M)
NOTE:
User must keep constant downward pressure on
workpiece when cutting. The blade guard foot is not designed
to hold down the workpiece, but is rather to help prevent the
workpiece from lifting up excessively.
When cutting at angles, the blade guard foot (1) should be
adjusted so it is parallel to the table and rests flat above the
workpiece.
1. To adjust, loosen the blade guard screw (2) with the 3 mm
hex key, adjust the blade guard foot (1) parallel to table,
and tighten the screw (2).
2. Loosen the blade
guard foot lock
knob (3) to raise
or lower the foot
until it rests
slightly above
the workpiece.
Tighten blade
guard foot
lock knob (3).
2
3
9
6
3
2
1
7
4
Fig. L
Pins
Fig. L-2
Fig. M
SAWDUST BLOWER (FIG. N)
The sawdust blower (1) should be
positioned to point to the blade and
workpiece to blow sawdust out of
the line-of-sight when cutting.
It is not designed to blow all
of the sawdust off the table.
This scroll saw accepts 5 in. (127 mm) length blades with a
wide variety of blade thickness and widths. The type of
material and cutting operations (size of radius or curve) will
determine the number of teeth per inch. As a rule, always
select the narrowest blades for intricate curve cutting and the
widest blades for straight and large curve cutting operations.
The following table represents suggestions for various
materials. When purchasing blades, refer to the back of
the package for the best use of blades and speeds on various
materials.
Use this table as an example, but practice and your own
personal preference will determine the best selection method.
BLADE SELECTION (FIG. O)
1
WARNING
To avoid injury from
accidental starting, always
turn the switch OFF and
unplugthe scroll saw before moving,
replacing the blade or making adjustments.
Fig. O
9.5 - 15
15 - 28
30 - 48
TEETH / INCH
TPI
BLADE
WIDTH INCH
BLADE/ SPM
BLADE
THICKNESS INCH
MATERIAL CUT
Medium turns on
1/4 in. (6.35 mm) to
1-3/4 in. (44.45 mm) wood,
soft metal, hardwood
Small turns on
1/8 in. (3.18 mm) to
1-1/2 in. (38.1 mm) wood,
soft metal, hardwood
Non-ferrous
metals/hardwoods
using very slow speeds
400-1200
9.5-15
15-28
30-48
0.018
(0.46 mm)
0.110
(2.8 mm)
.055-.110
(1.4-2.8 mm)
024-.041
(0.6-1.0 mm)
.010-.018
(0.25-0.46 mm)
.012-.019
(0.3-0.48 mm)
800-1800
Varies
NOTE:
When using blades, sometimes speeds must change
to compensate for smaller curves, radii or smaller diameters.
Thinner blades will have more possibilities for blade deflection
when cutting angles which are not perpendicular to the table.
Read
RECOMMENDATION FOR CUTTING
for more
suggestions.
NOTE:
The blade must be installed with the teeth pointing
downward, to prevent the workpiece from being pulled
upward by the saw blade action.
Fig. N