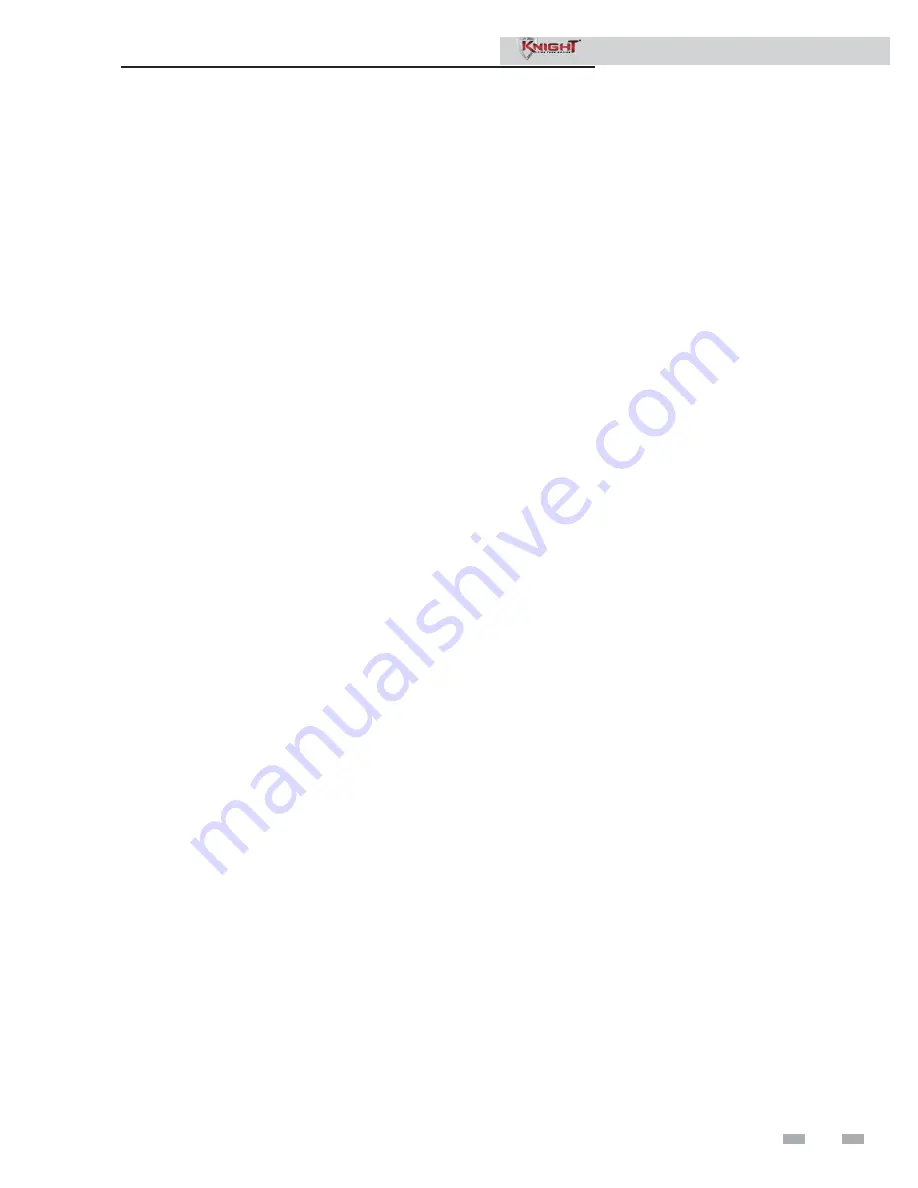
69
Installation & Operation Manual
11
Operating information
(continued)
Anti-cycling
After the burner turns off, the control will delay the next
burner cycle for a set time period (time is adjustable by the
installer). The time delay will be bypassed if the inlet water
temperature drops too far during the delay.
Boiler and system pump control
The boiler pump will run whenever the burner is firing,
unless the DHW is programmed for Normal Mode and the
boiler is heating the DHW tank. The boiler pump will run
during Freeze Protection Mode as well. It will continue to
run for a short time after the burner turns off or the Freeze
Protection Mode ends.
The system pump will run whenever there is a space heating
call for heat, or the boiler goes into Freeze Protection Mode.
It may be programmed to run during a DHW call for heat
when the DHW is programmed for Zone Mode. It will
continue to run for a short time after the end of the heat
demand or the Freeze Protection Mode. The system pump
can be programmed to run continuously if desired, except
during outdoor shutdown and/or a DHW call for heat.
DHW recirculation pump control
When a DHW recirculation loop is used, the Knight Wall
Hung Fire Tube boiler can control the recirculation pump. To
activate this function, simply install the DHW recirculation
sensor into the return water from the DHW circulation loop.
The control will turn on the DHW recirculation pump when
the return water drops 10°F (5.5°C) below the DHW tank set
point, and will turn back off when the return water rises to
within 5°F (2.5°C) of the DHW tank set point. The control
will turn the DHW recirculation pump off whenever DHW
night setback is active.
Temperature control
Modulation
The Knight Wall Hung Fire Tube boiler is capable of
modulating its firing rate on WH56 models only from a
minimum of 15% to a maximum of 100%, WH86 - 286
models from a minimum of 10% to a maximum of 100% and
the WH400 model from a minimum of 20% to a maximum
of 100%. The firing rate is dictated by the call for heat (i.e.,
space heating or domestic hot water), the heating load, ramp
delay (if enabled), and various other temperature limitations.
Ramp delay
For systems with lower flow, the SMART SYSTEM can
limit the firing rate (when enabled) when a space heating
call for heat starts, or when switching from a DHW call for
heat to a space heating call for heat. There are six (6) limits
that can be programmed, as well as six (6) time intervals
corresponding to each limit. The sixth limit will also limit
the firing rate for the rest of the call for heat.
Gradient limiting
If during operation of the boiler the outlet water temperature
is rising too quickly, the control will reduce the firing rate to
its lowest setting.
Outdoor air reset
With the outdoor air sensor connected, the control module
will calculate the set points of the three (3) space heating
demands based on the programmed reset curves. The
installer can change the slope of the reset curves by several
adjustable parameters. The user can limit the maximum
set point for the system using the space heating set points.
Boost function
If outdoor air reset is active, and any space heating demand
has been active continuously for a set period of time
(time adjustable by installer) and there has been no DHW
demands, the control will increase the set point of that
demand by a fixed number of degrees (adjustable by
installer). This process will continue until the space heating
demand ends, the set point reaches the programmed set
point or a maximum of 20 increases has occurred. Once the
system heat demand is satisfied, the set point will revert to
the value determined by the reset curve.
Night setback
The controller may be programmed to reduce the space
heating and DHW set points during certain times each week.
Seven different start and stop times may be programmed for
the space heating setback and seven start and stop times
for the DHW setback. Any night setback event scheduled
within the next seven (7) days can be temporarily bypassed
if desired.
Vacation mode
Vacation Mode is used to lower the Space Heat (SH) and /
or DHW set points much like Night Setback. The set points
will remain lowered until Vacation Mode is disabled. Night
Setback will not function when Vacation Mode is enabled.
Flame current support
To prevent nuisance shutdowns when the boiler is firing
at minimum rates, the control will increase the firing rate
when the flame signal drops too low.