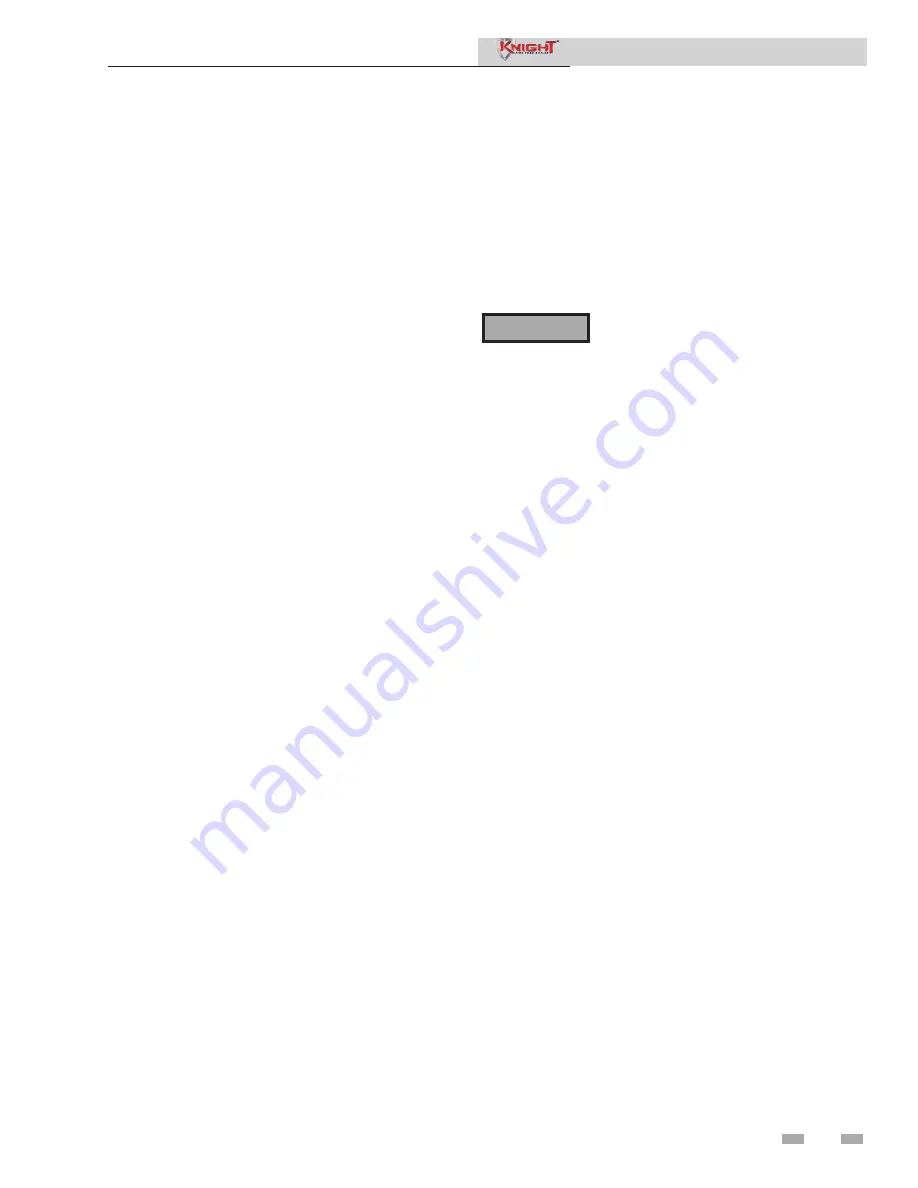
27
1
Service
(continued)
The other Cascade divider method is Efficiency
Optimization, designated as EFF in the menu. This method
is used, as the name implies, when it is desired to have the
most efficient system. When the first boiler reaches 100%
rate, it lowers its rate to 50% and turns on the next boiler at
50%. The two (2) boilers then modulate at the same rate.
As the calculated load increases further and both boilers
ramp up to 100%, it lowers the rate of the first two (2)
boilers to 67% and brings the next boiler on at 67%.
The
three (3) boilers then modulate together. As the calculated
load decreases, the boilers will reach 20%, at which time
the last boiler (the third in our example) will turn off and
the Cascade will increase the rates of the remaining boilers
to provide the equivalent total output as before ((3 x 20%)
/ 2 = 30% in our example). Efficiency optimization is
automatically selected when boilers of different sizes are
programmed into the Leader control.
Minimum On/Off Time
In order to prevent units in a Cascade from short cycling,
this parameter defines the minimum ON and OFF time for
each unit. The installer can adjust this time by accessing the
Minimum On/Off Time
parameter. The minimum setting
is 0 seconds and the maximum setting is 10 minutes. The
default is 30 seconds.
Minimum Next On Time
In order to reduce the risk of temperature overshoot with
a Cascade, this parameter defines the minimum time delay
from starting one unit until the next unit may be started.
The installer can adjust this time delay by accessing the
Minimum Next On Time
parameter. The minimum setting
is 0 minutes and the maximum setting is 10 minutes. The
default is 60 seconds.
Minimum Number of Pumps On
When the boiler is a Cascade Leader, it can force a
minimum number of boiler pump outputs to be on
continuously, regardless of how many boilers are firing.
This is normally used when the boilers are piped in a
full-flow configuration, and the boiler pump outputs are
controlling isolation valves. The Leader will force the
boiler pump output on the highest priority boiler to turn
on first, then the boiler pump output on the second highest
priority boiler, and so forth, until the minimum number of
pump outputs are turned on. The range of this parameter
is 0 to 8. The default value is 0.
Alternate Leader
This parameter allows the Member 1 boiler to automatically
assume control of the Cascade should it lose communication
with the Leader boiler. When programmed to YES, it is
recommended that the Member 1 boiler have its own set of
external sensors installed (such as the system supply sensor),
to maintain the same level of temperature control as with the
Leader boiler. Voltage signals (such as the 0 - 10V system
pump speed input) can be connected to both boilers.
DO NOT connect the sensors connected to
the Leader boiler to the Member 1 boiler.
The actual water temperatures will be higher
than expected, which could lead to property
damage, personal injury, or death.
When communication is re-established with the Leader boiler,
Member 1 will automatically relinquish control of the Cascade
to the Leader boiler.
The default value of this parameter is NO.
Boiler Size
When boilers of different sizes are connected together in a
Cascade, the Leader boiler has to know the size of each boiler
in that Cascade. The Knight Fire Tube boiler models are pre-
programmed with their respective sizes. Each Member will send
its input rating to the Leader. There are previous generation
boilers that do not have this capability. When operating in
Cascade with these boilers it may be necessary to input each
member boiler size to the Leader boiler. This may be done by
accessing the
Boiler Size
parameter (for additional information
reference the Programming Smart System Controls for Multiple
Size Units & Front End Loading Instruction Sheet provided in
the literature package attached to the appliance).
Building Management System (BMS)
BMS
The set point or modulation of the boiler may be controlled
through the 0 - 10V BMS input, BACnet, or ModBus. When
the
BMS parameter
is set to INACTIVE, the 0 - 10V input will
be ignored. When set to ACTIVE, the set point or modulation
will be controlled by the voltage on the 0 - 10V input (in the
case of 0 - 10V BMS control), or the 0 - 10V input value received
through ModBus or BACnet. The default value is INACTIVE.
BMS Type
When programmed for BMS control through the 0 - 10V BMS
input or through ModBus/BACnet, the 0 - 10V signal can be
interpreted as either a modulation command or a set point.
When the
BMS Type
parameter is set to POWER, the 0 - 10V
signal will control the modulation. When set to SETPOINT, the
0 - 10V signal will control the SH set point. The default setting
is SETPOINT.
Service Manual
⚠
WARNING
Summary of Contents for 100 Series
Page 51: ...51 Service Manual Notes ...