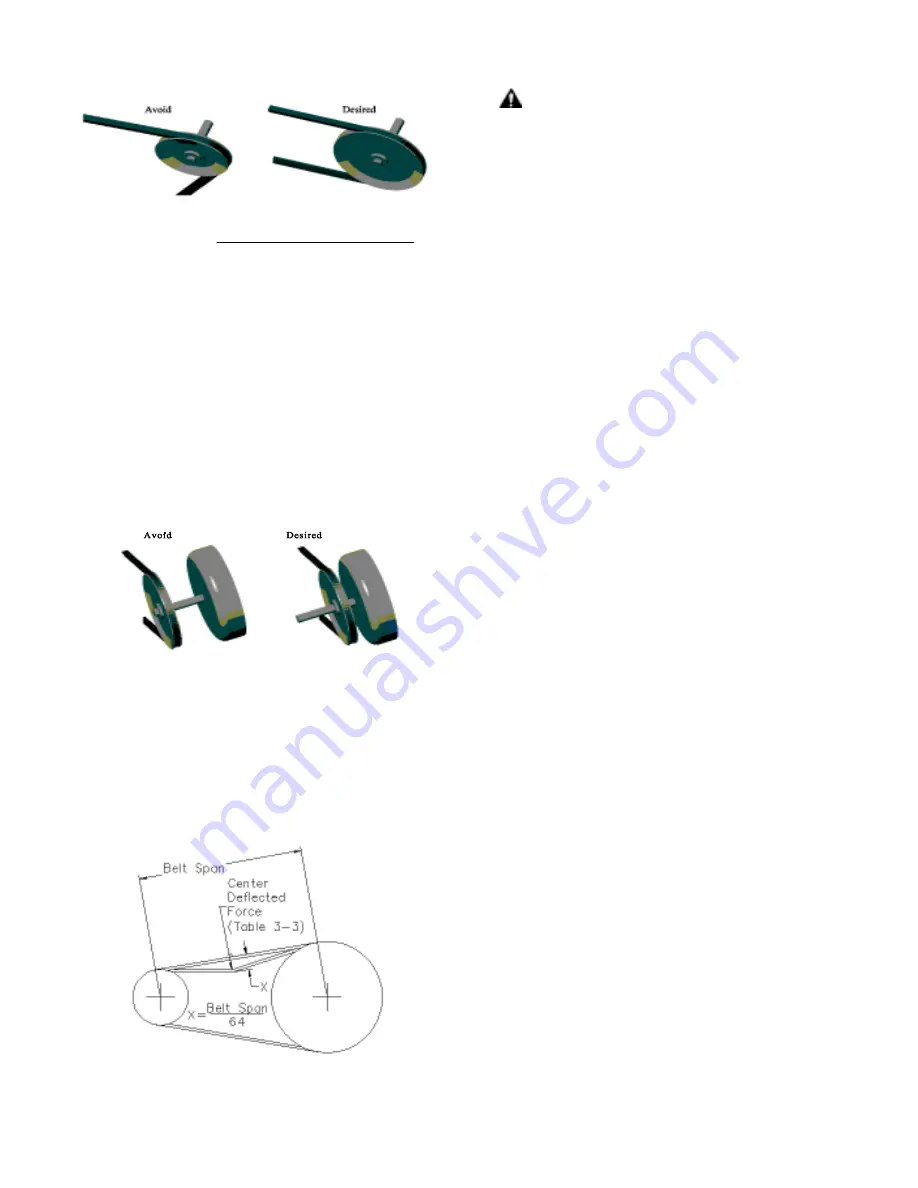
4
<
7 '% (;
?
9
L
!,!,@,#
1
7
In general, use the fewest number of belts that will transmit the
required torque without slipping. See Table 3 3 for recommended
maximum number of belts.
Each belt adds to the tension in the
system, which increases load on the shafts and bearings. Belts are
most efficient when operated at or near their rated horsepower.
If the sheaves have more grooves than the number of belts required,
use the grooves closest to the motor.
!,!,@,! (-
) '
Install sheaves as close to the housing as possible to increase the
bearing life of the motor and driven equipment
4
#
!,!,@,@
7
%
/%
*
:
Belt tensioning by feel is
%
acceptable. Tensioning by "feel" can
be very misleading, and can damage motor and equipment.
It is normal for V belts to squeal initially when line starting a motor.
In general, belt tensions should be kept as loose as possible while
still transmitting the required torque without slipping. Belt tensions
must be measured with a belt tension gage.
These inexpensive
gages may be obtained through belt manufacturers, or distributors.
Proper belt tension is determined by measuring the force required to
deflect the center of the belt a given distance. The proper deflection
(in inches) is determined by dividing the belt span in inches by 64.
Calculate the proper deflection and then see Table 3 3 for the
required “Deflected Force” to achieve that deflection.
After tensioning the belt, rotate the sheaves for several rotations or
operate the system for a few minutes to seat belts into the grooves,
then re tension the belts. New belts will stretch during use, and
should be retensioned after the first eight hours of use.