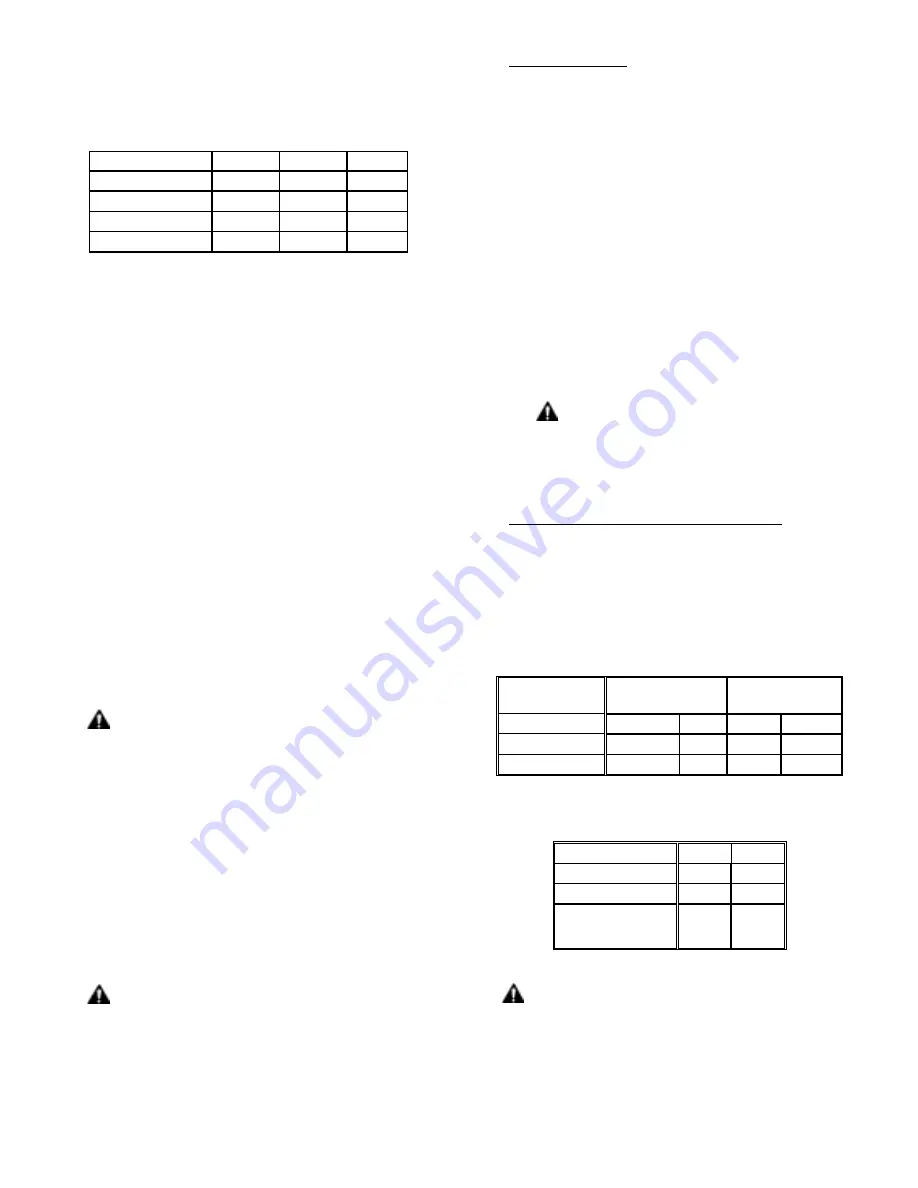
to Table 3 5 values.
Definite purpose VFD motors may
accommodate longer cable lengths.
For additional
information contact motor manufacturer.
% 1
!
B
1
'
4 - 6
;
These values are based on 3 kHz carrier frequency. Add
suitable VFD output side filters when exceeding the listed
values.
( 3
#! =
@
=
A =
!#
600 ft.
125 ft.
40 ft.
!
<<
1000 ft.
225 ft.
60 ft.
#
180 m.
40 m.
12 m.
## #
,
300 m.
70 m.
18 m.
!,!, ,!
= ? 6
4*
Equipment grounding conductors
may be run in the same conduit as the AC motor power leads.
This wire must be used as the equipment ground for the motor and
not as the fourth current carrying wire of a “WYE” motor circuit.
The grounded metal conduit carrying the output power conductors
can provide EMI shielding, but the conduit does not provide an
adequate ground for the motor; a separate grounding conductor
must be used. Grounding the motor neutral (WYE) of a VFD
powered motor may result in a VFD ground fault trip. Improper
grounding of an inverter fed motor may result in frame voltages in
excess of 500 Volts. Refer to Grounding section 3.4.4
!,!, ,@
= ? " ( 4
;-
*
/%
* (
6'
;& (
% $
'/$ *
Single Phase motors are
%
suitable for use on VFD power.
Connecting a Single Phase Motor to a VFD voids the warranty.
!,!, ,
(
0 =
4
0 '
*
VFD’s will couple stray (common mode) voltage to motor
mounted
RTDs,
thermistors,
thermostats
and
space
heaters.
The leads of these elements must be properly
insulated and control input circuits must be designed to
withstand this common mode voltage.
!,!,
(( $
( 9 ;$ = (
(*
!,!, ,<
6
*
Carefully read and understand the accessory
manufacturer’s instructions, supplied with motor. Contact the
manufacturer for additional information.
!,!, ,#
7
8
:
/%
* =
;
7 8
Motors with brakes that are designed for vertical applications are
equipped with springs to support the brake pressure plate.
Mounting a horizontal brake motor vertically shaft up or down may
require a pressure plate spring modification. Failure to modify the
brake for the vertical application may result in premature brake
failure.
If in question, consult brake literature or brake
manufacturer.
7
8
(
5
4*
Do NOT connect the brake
solenoid to the output of a VFD. The brake solenoids must be
wired to 50/60 Hz line power
!,!, ,!
(
&
*
Motors provided with space heaters have two leads that are
brought into the conduit box or into an auxiliary box. These leads
are marked ”H1”, “H2” (”H3”, “H4” if a second space heater is
supplied). See the space heater nameplate on motor for heater
rating.
5 $
6*
? = (
# H;' (
& G $?
The space heater temperature rating when used in Class I,
Division 2 motors shall
%
exceed 80% of the auto ignition
temperature of the hazardous gas or vapor. See the space heater
nameplate on motor for heater Temperature Code and heater
rating. Failure to follow this instruction could result in serious
personal injury, death and/or property damage
!,!, ,@
%-
;
*
6
*
When thermal protection is provided, one of
the following will be stamped on the nameplate:
<,
O%& $
''. ;$ %
% ?
” This motor has built in thermal
protection.
Thermal
protectors
open
the
motor circuit
electrically when the motor overheats or is overloaded. The
protector cannot be reset until the motor cools. If the
protector is automatic, it will reset itself. If the protector is
manual, disconnect motor from power supply. After protector
cools (five minutes or more) press the reset button and
reapply power to the motor. In some cases a motor is marked
“Auto” and the connection diagram on the motor will identify
T’Stat leads – see “2 ” below. (See warnings on Manual and
Automatic reset protectors section 1.1)
#,
O5 %&
= $&
% ;$ %
% =
? =
”: This motor is
provided with an overheat protective device that does not
directly open the motor circuit. Motors nameplated with this
phrase have either thermostats, thermisters or RTD’s. The
leads to these devices are routed into the motor conduit box
or into an auxiliary box. The lead markings are defined on the
nameplate (normally “P1”, “P2”) . The circuit controlled by the
overheat protection device must be limited to a maximum of
600 volts and 360 volt amps. See connection decal provided
inside the terminal box cover. Failure to connect these over
temperature devices (when provided) will void the warranty.
5 $
6*
H;' (
& G $?
For Hazardous Locations motors provided with thermostats
UL and the NEC require connection of thermostat leads into
the control portion of a manual reset start circuit. Failure to
follow this instruction could result in serious personal injury,
death and/or property damage
$
%
?
$%? *
When winding
and/or bearing RTDs are provided the RTD lead markings are
defined on the nameplate. (Normally “R1”, “R2”, “R3” etc.)
!,!, ,
$%?
> %
(
4 *
Tables 3 6 & 3 7 are suggested initial RTD alarm and trip settings.
For motors found to operate significantly below these values the
settings may be reduced accordingly.
% 1
!
5
4 $%? " %
'
@
B
1
'
7 %
$
≤
≤
≤
≤
%
$
≤
≤
≤
≤
<
%
%
Up to 1.0 SF
130
140
155
165
>1.0 to 1.15 SF
140
150
160
165
% 1
! A
7
4 $%? " %
'
@
B
1
1
%
Up to 40
95
100
> 40
110
115
Bearings that are
Heat Stabilized to
150
130
135
!,!,A
6/ $?(*
5 $
6*
$ % %
6 ; $%( & G $?
When devices are assembled to the motor shaft, be sure to install
protective devices such as belt guards, chain guards, and shaft
covers. These devices must protect against accidental contact with
extremities, hair, and clothing. Consider the application and provide
guarding to protect personnel. Remove all unused shaft keys and
loose rotating parts to prevent them from flying off and causing
bodily injury. Failure to follow this warning could result in serious
personal injury, death and/or property damage.