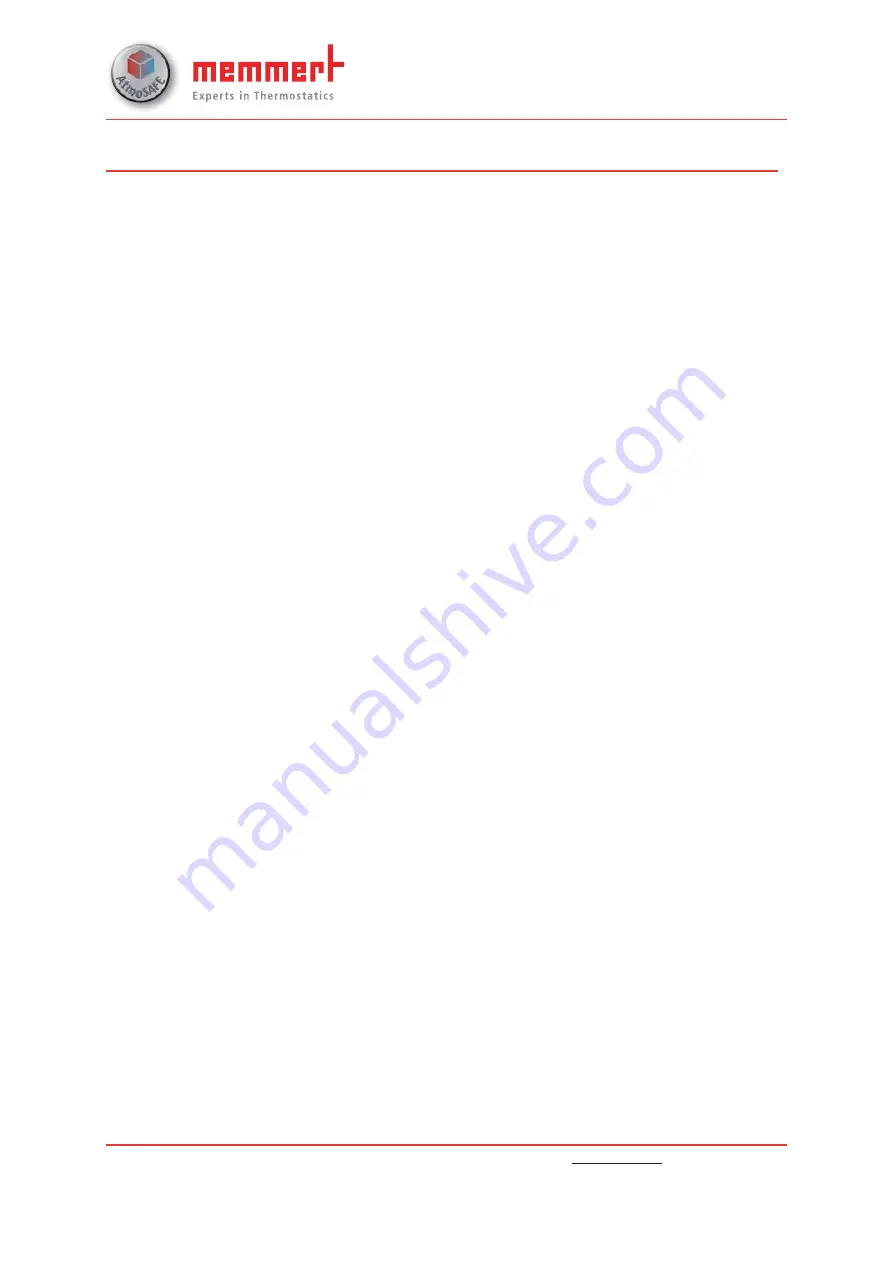
2
MEMMERT GmbH + Co. KG
Willi-Memmert-Straße 90-96
D-91186 Büchenbach
Germany
Phone: +49 (0)9122 925-0
Fax:
+49 (0)9122 14585
Email: [email protected]
Internet: www.memmert.com
Customer service:
Hotline:
+49 (0)9171 9792 911
Service fax: +49 (0)9171 9792 979
E-mail: [email protected]
© 2018 Memmert GmbH + Co. KG
About this manual
Purpose and target audience
This manual, together with the operating manual for the MEMMERT vacuum oven, describes
how to use and put into operation the MEMMERT pump module. Pump modules can be pur-
chased with or without a pre-installed vacuum pump.
The manual contains the original maintenance and operating manual for the membrane vacu-
um pump, which may have been installed, from the company KNF.
The pump module may only be used in combination with the MEMMERT vacuum oven VO or
VOcool. All information in terms of safety instructions, assembly, function, transport, putting
into operation, operation, troubleshooting, maintenance and decommissioning/disposal can be
found in the operating manual for the vacuum oven VO.
This manual is intended for use by trained personnel of the owner, who have the task of ope-
rating and/or maintaining the respective appliance. If you are asked to work on the appliance,
read this manual carefully before starting.
Familiarise yourself with the safety regulations. Only perform work that is described in this ma-
nual. If there is something you do not understand, or certain information is missing, ask your
manager or contact the manufacturer. Do not do anything without authorisation.
Other documents to be observed as applicable:
►
The operating manual for the MEMMERT vacuum oven VO
►
The original maintenance and operating manual for the vacuum pump from KNF
Storage and resale
This operating manual belongs with the appliance and should always be stored where per-
sons working on the appliance have access to it. It is the owner's responsibility to ensure that
persons who are working on or are going to work on the appliance know where to find the
operating manual. We recommend that it is always stored in a protected location close to the
appliance. Make sure that the operating manual is not damaged by heat or humidity. If the
appliance is resold or transported and then set up again at a different location, the operating
manual must remain with it.
The current version of this operating manual in PDF format is also available for download from
http://www.memmert.com/en/service/downloads/user-manual/.