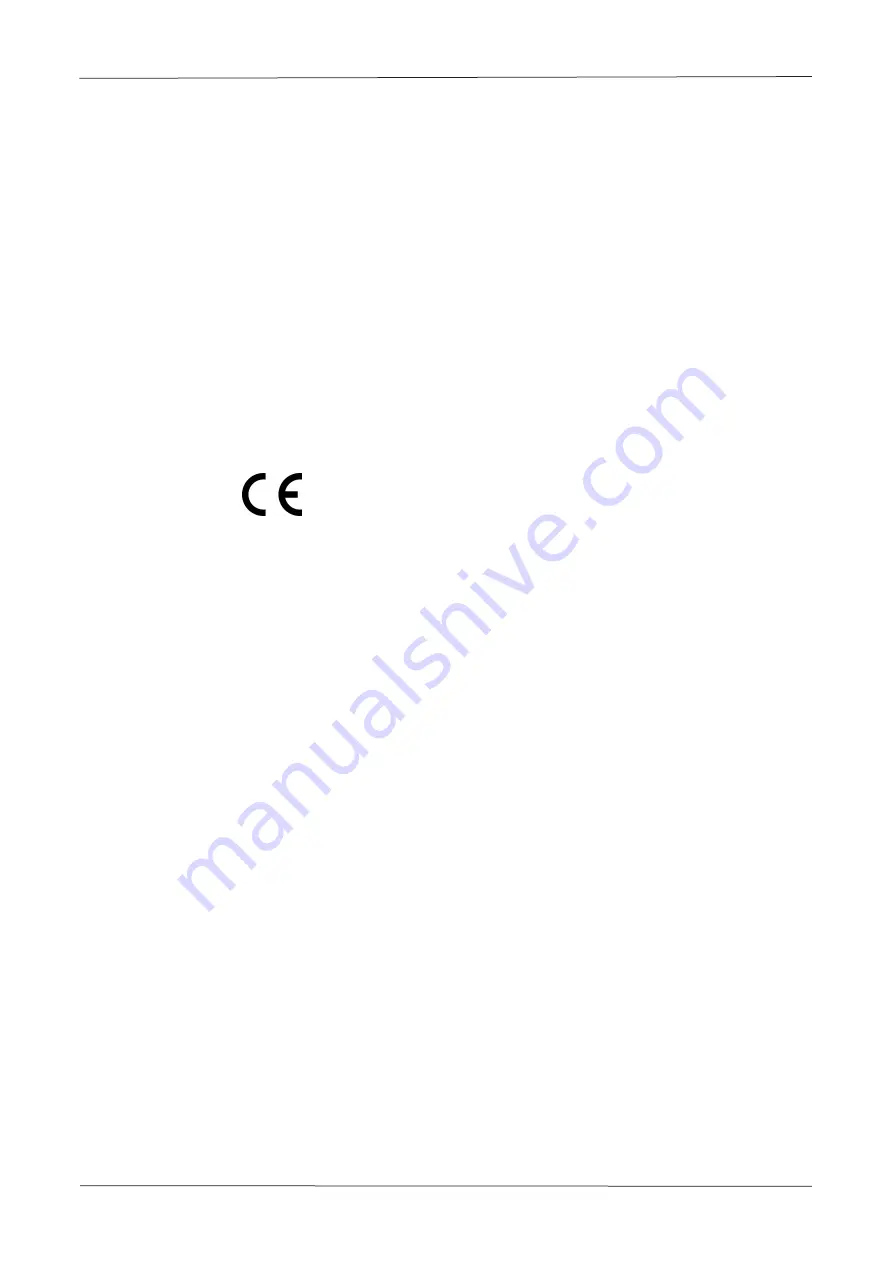
Safety
Diaphragm Pump N936
6
Translation of Original operating and installation instruction, English, KNF 320276-320275 09/19
Environmental protection Store and dispose of all replacement parts in accordance with environmen-
tal regulations. Observe the respective national and international regula-
tions. This applies in particular to parts that are contaminated with toxic
substances.
EU/EC directives/standards With respect to the Machinery Directive 2006/42/EC, the pumps are partly
completed machinery and are, therefore, to be regarded as not ready for
use. Partly completed machinery may not be commissioned until it has
been determined that the machine into which the partly completed machin-
ery is to be installed complies with the provisions of the Machinery Direc-
tive 2006/42/EC. The following fundamental requirements of Annex I of Di-
rective 2006/42/EC (general principles) are applied and observed:
§
General principles no. 1
§
No. 1.1.2. / 1.1.3. / 1.3.1. / 1.3.3. / 1.3.4. / 1.4.1. / 1.5.1. / 1.5.2. /
1.5.8. / 1.5.9. / 1.7.4. / 1.7.4.1. / 1.7.4.3.
As these partly completed machines are built-in devices, the mains con-
nections and equipment for disconnecting and switching off the partly com-
pleted machinery as well as overcurrent and overload protection gear must
be considered when mounting.
Furthermore, protection against contact with moving and hot parts, if
present, must be provided during installation.
The pumps comply with Directive 2011/65/EU.
The following harmonized standards are satisfied:
§
DIN EN 55014-1/2
§
DIN EN 61326-1 – Class A
§
DIN EN 60204-1
§
DIN EN 50581
§
DIN EN 61000-6-2/3
The pumps comply with:
§
EN 61010-1
§
IEC 61010-1
§
UL 61010-1
§
CAN/CSA-C22.2 No. 61010-1
including the following comments:
§
The pumps are intended for use up to degree of contamination 2 or
comparable environment.
§
The requirements on the housing with respect to fire protection, me-
chanical protection and electrical connection must be satisfied in the fi-
nal application.
§
Maximum ambient temperature for continuous operation: +50°C.
Briefly >+50°C; Temperatures must be determined in the final applica-
tion.
§
The warming (temperature measurements) must be tested in the final
application.
§
The terminal strip is suitable exclusively for wiring at the factory.
§
The pumps must be connected to protective earth.
§
The motor has insulation class F (+155°C) and is equipped with a self-
resetting overtemperature switch.
Summary of Contents for N963
Page 29: ......
Page 30: ......
Page 31: ......
Page 32: ...KNF worldwide Find your local KNF partner on www knf com...