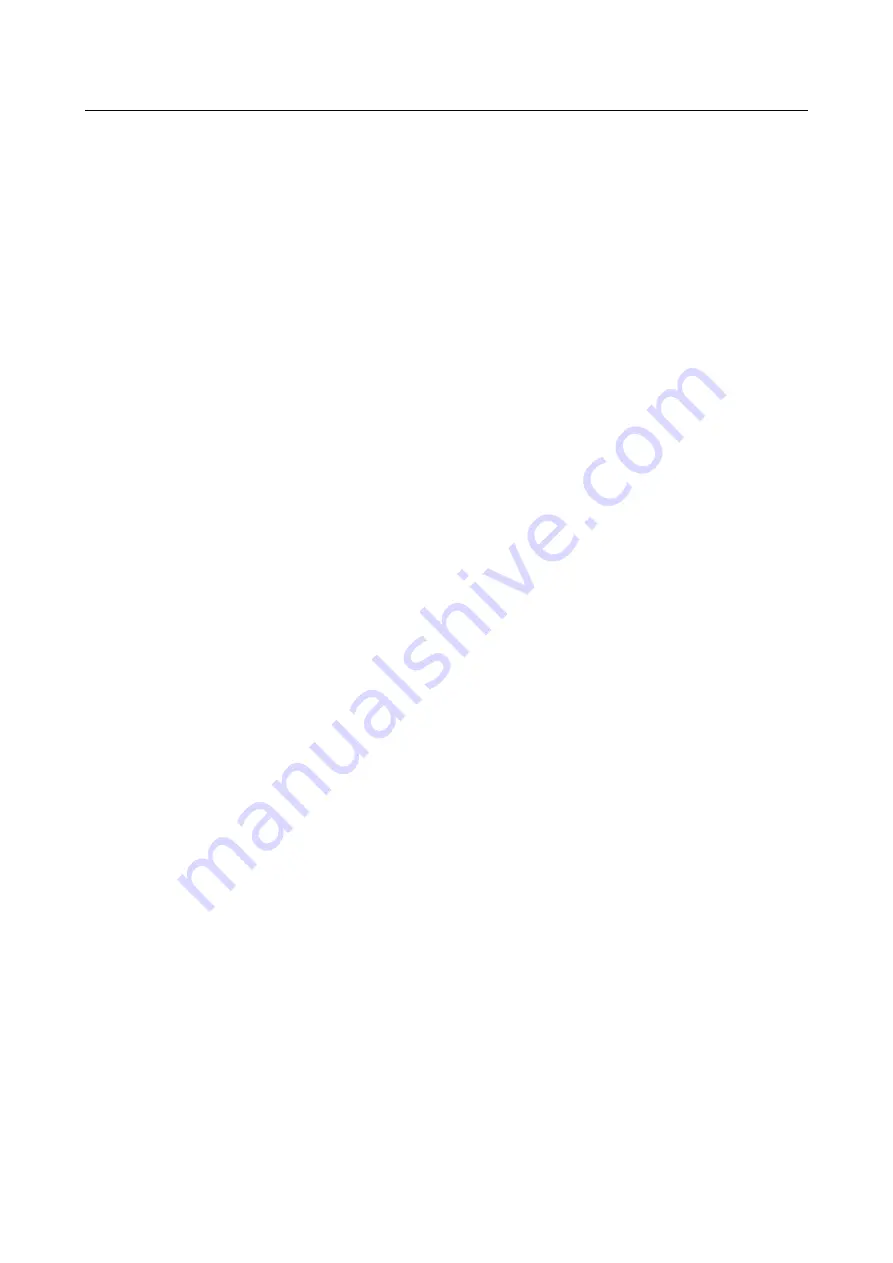
10
2.1 Basic safety instructions
2.1.1 Observe notes in the operating instructions
The basic prerequisite for the safe handling and uninterrupted operation of this honing machine is
knowledge of the basic safety instructions and regulations.
• These operating instructions contain important notes on how to operate the honing machine
safely.
• All persons carrying out work on the honing machine must follow these operating instructions,
in particular the safety notices.
• In addition, the accident prevention rules and regulations applicable at the place of use of the
machine must also be observed.
2.1.2 Operator's duty
The operator is obliged to allow only those persons to work on the honing machine, who
• are familiar with the basic occupational safety and accident prevention regulations and have
been trained and instructed in the handling of the honing machine,
• have read the operating instructions, particularly the “Safety” section, and have read and
understood the warning notes. They have given a signed confirmation of this in writing.
It is also checked at regular intervals as to whether the worker is fulfilling his employee obligation
to observe safety at work.
2.1.3 Obligations on the part of the personnel
All the personnel working on the honing machine shall be obliged to
• observe the basic occupational safety and accident prevention regulations,
• read the operating instructions, particularly the “Safety” chapter, and the warning notes. They
must provide signed confirmation of this in writing.
2.1.4 Hazards associated with handling the honing machine
The honing machine has been built to the latest technological standards and the acknowledged
rules of technical safety. In spite of that, its use presents inherent risks which could result in bodily
harm or even death of the user or third persons, or impairment of the honing machine or other
property.
The honing machine may be used only:
• for the intended purpose, and
• in faultless condition with regard to safety-relevant aspects.
2. Safety