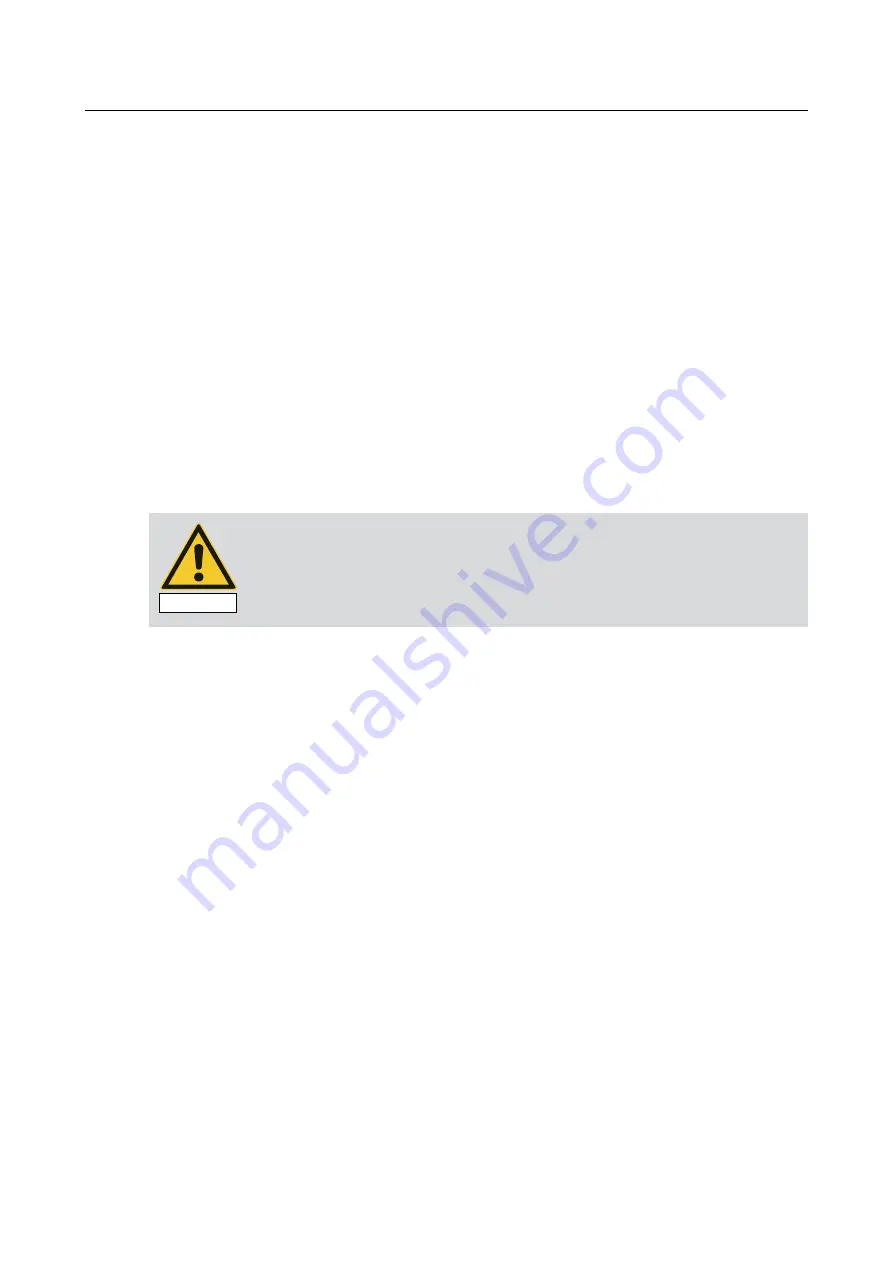
28
5.5 Initial commissioning of the grinding machine
Place the grinding machine at the installation site on a level base.
Level out any floor unevenness by adjusting the machine feet (3-2/6) with a flat wrench (SW19).
Check the machine for correct horizontal and vertical position by laying an appropriate water level
on the respective guide rails.
Dismantle all the handling devices on the machine. Ensure that all the axes can be moved freely.
Have a qualified electrician on site install the current supply.
Have the compressed air supply and the connection with the power supply installed on site by a
specialist.
Completely install and check the safety devices before commissioning.
Have all the safety devices checked for proper function by trained
personnel before commissioning.
CAUTION
5. Installation