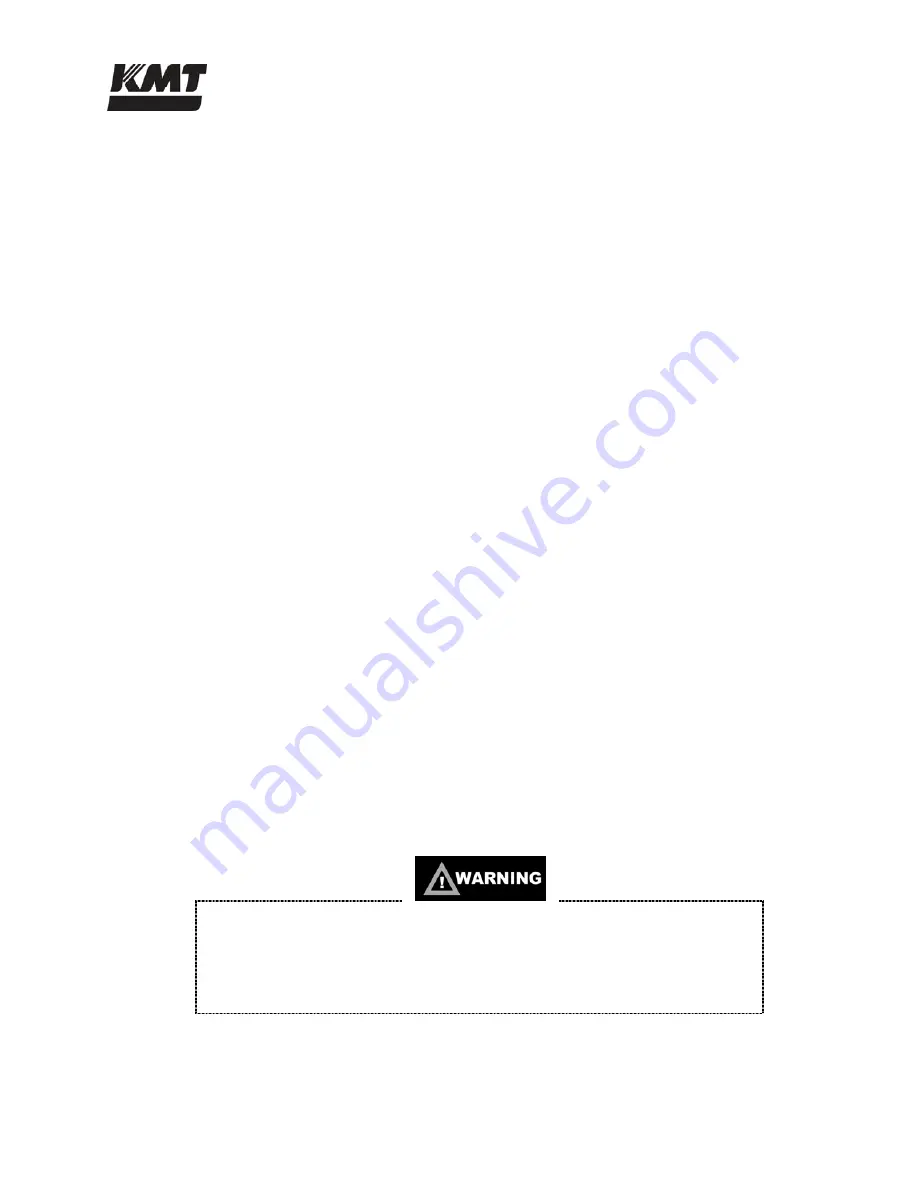
Section 8
High Pressure Water System
20425618
5-2005/Rev 0
8-22
8.
Remove the cylinder liner from the bore and inspect for possible heat or wear damage, or
for debris. If cracks or brittleness are detected on the tabs on the ends of the liner, the
liner must be replaced.
9.
Feel approximately one inch into the cylinder bore for obvious ridges or grooves. If seal
debris is present, follow the procedure, High Pressure Cylinder Maintenance.
10.
Inspect the plunger surface for flaws. Rotate the plunger 360 degrees by hand while
viewing light reflection on the surface to detect any dullness, streaks, pits or other defects.
Run a fingernail perpendicular to the direction of the suspected flaws to determine the
severity of defects. Depending on the seal life achieved with the removed seal assembly,
make a judgment regarding plunger and/or cylinder replacement. If seal debris is present
on the plunger, polish with 600-grit wet/dry sandpaper, using a radial motion.
11.
Lightly coat the new seal components with FML-2 grease and install the new components
on the plunger. Ensure the proper orientation of the backup rings as illustrated in Figure
8-12, High Pressure Seal Assembly.
The cantilever spring inside the u-cup seal is easily distorted. Verify that the spring, lips
and cavity appear uniform prior to installation.
12.
Slide the cylinder liner over the plunger.
13.
Install the high pressure cylinder assembly into the hydraulic cylinder head, following the
procedure, High Pressure Cylinder Assembly Installation.
14.
Reconnect the high and low pressure water piping and turn the low pressure water supply
on.
8.11
Hydraulic Cartridge Seal and Plunger Removal
The following procedure is used to remove the hydraulic cartridge seal and the plunger.
Prior to removing electrical power or any high or low pressure piping, start the machine and
extend the plunger on the end to be serviced to allow full exposure when the unit is disassembled.
1.
Turn the machine off and observe the appropriate Lockout/Tagout procedures.
Severe injury can result if the machine is not properly locked out. Observe
electrical Lockout/Tagout procedures before proceeding.
Ensure all pressure is relieved or blocked from the hydraulic and high pressure
circuits before proceeding.
2.
Disconnect the high and low pressure water piping, following the procedure, High and
Low Pressure Water Piping.
Summary of Contents for STREAMLINE S30
Page 1: ...MANUAL 20425545 R01 STREAMLINE S30 WATERJET INTENSIFIER OPERATION AND MAINTENANCE MANUAL ...
Page 66: ...Section 7 Electrical System 20425610 5 2005 Rev 0 7 2 Figure 7 1 Sensors and Solenoids ...
Page 139: ...Section 11 Parts List 20425652 5 2005 Rev 0 11 9 Figure 11 2 Intensifier Assembly ...
Page 143: ...Section 11 Parts List 20425652 5 2005 Rev 0 11 13 Figure 11 5 Hydraulic Piston Assembly ...
Page 145: ...Section 11 Parts List 20425652 5 2005 Rev 0 11 15 Figure 11 6 High Pressure Piping ...
Page 147: ...Section 11 Parts List 20425652 5 2005 Rev 0 11 17 Figure 11 7 Hydraulic Power Package ...
Page 149: ...Section 11 Parts List 20425652 5 2005 Rev 0 11 19 Figure 11 8 Motor Pump Assembly ...
Page 151: ...Section 11 Parts List 20425652 5 2005 Rev 0 11 21 Figure 11 9 Hydraulic Manifold Assembly ...
Page 153: ...Section 11 Parts List 20425652 5 2005 Rev 0 11 23 Figure 11 10 Hydraulic Hose Connections ...
Page 155: ...Section 11 Parts List 20425652 5 2005 Rev 0 11 25 Figure 11 11 Reservoir Assembly ...
Page 157: ...Section 11 Parts List 20425652 5 2005 Rev 0 11 27 Figure 11 12 Bulkhead Pipe Assembly ...
Page 159: ...Section 11 Parts List 20425652 5 2005 Rev 0 11 29 Figure 11 13 Electrical Assembly ...
Page 163: ...Section 11 Parts List 20425652 5 2005 Rev 0 11 33 Figure 11 15 Junction Box Configuration ...
Page 165: ...Section 11 Parts List 20425652 5 2005 Rev 0 11 35 Figure 11 16 Electrical Interface ...
Page 167: ...Section 11 Parts List 20425652 5 2005 Rev 0 11 37 Figure 11 17 Dump Valve Kit ...
Page 173: ...Section 11 Parts List 20425652 5 2005 Rev 0 11 43 Figure 11 20 Low Pressure Water Filter ...
Page 175: ...Section 11 Parts List 20425652 5 2005 Rev 0 11 45 Figure 11 21 Proportional Pressure Control ...
Page 179: ...Section 11 Parts List 20425652 5 2005 Rev 0 11 49 Figure 11 23 Intensifier Assembly ...
Page 181: ...Section 11 Parts List 20425652 5 2005 Rev 0 11 51 Figure 11 24 High Pressure Piping ...
Page 183: ...Section 11 Parts List 20425652 5 2005 Rev 0 11 53 Figure 11 25 Hydraulic Power Package ...
Page 185: ...Section 11 Parts List 20425652 5 2005 Rev 0 11 55 Figure 11 26 Motor Pump Assembly ...
Page 187: ...Section 11 Parts List 20425652 5 2005 Rev 0 11 57 Figure 11 27 Hydraulic Manifold Assembly ...
Page 189: ...Section 11 Parts List 20425652 5 2005 Rev 0 11 59 Figure 11 28 Hydraulic Hose Connections ...
Page 191: ...Section 11 Parts List 20425652 5 2005 Rev 0 11 61 Figure 11 29 Reservoir Assembly ...
Page 193: ...Section 11 Parts List 20425652 5 2005 Rev 0 11 63 Figure 11 30 Electrical Assembly ...
Page 195: ...Section 11 Parts List 20425652 5 2005 Rev 0 11 65 Figure 11 31 Control Box Configuration ...
Page 226: ......
Page 227: ......
Page 228: ......
Page 229: ......
Page 230: ......
Page 231: ......
Page 257: ......
Page 258: ......
Page 259: ......
Page 260: ......
Page 261: ......