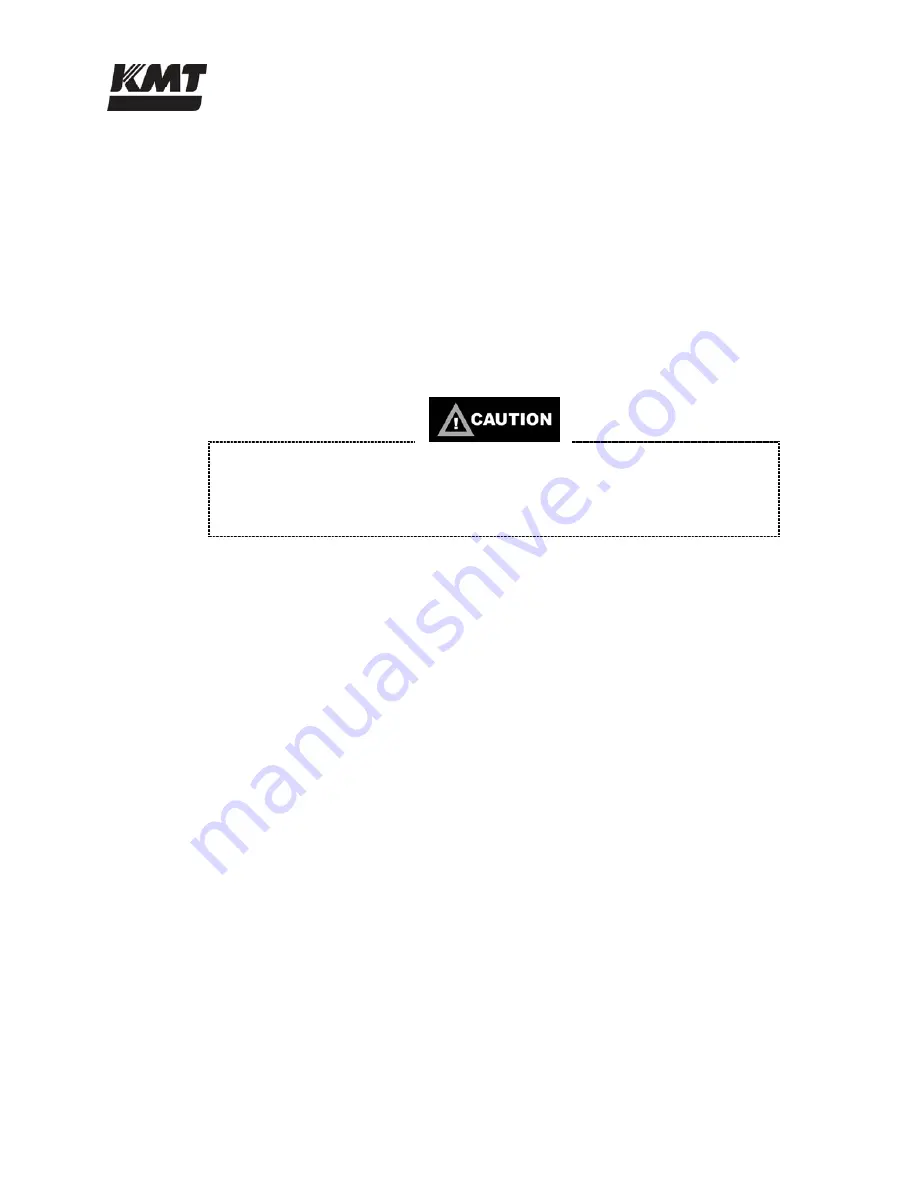
Section 6
Hydraulic System
20425603
5-2005/Rev 0
6-3
The main system relief valve provides system protection by monitoring the oil pressure entering
the manifold. If the hydraulic pressure exceeds 3,400 psi (234 bar), the valve opens to limit the
pressure. The valve is factory calibrated and is not serviceable. A drain line from the valve
prevents oil from collecting behind the relief valve to ensure a constant pressure under all
operating conditions.
The hydraulic system operates at high or low pressure settings up to the maximum flow capacity
of the hydraulic pump. The high and low limit compensators mounted on the pump regulate the
flow of hydraulic fluid to maintain constant operating pressures. Operating pressures are set and
adjusted at the high and low pressure control valves on the manifold.
If the machine is equipped with proportional pressure control, low pressure is adjusted at the
manifold, and the high pressure setting is made from the controller.
The high and low limit compensators regulate the flow of hydraulic fluid to the
system by controlling the angle of the swashplate. If the oil is not properly
maintained, the compensators can become blocked with debris. As a result, pump
control will be lost and you will not be able to create hydraulic oil pressure.
The normally closed, two position solenoid valve is controlled by the operator’s selection of high
or low pressure. The valve is closed while operating in high pressure and is open during low
pressure operation. A light on the solenoid connector indicates low pressure operation.
A reference gauge on the top of the manifold displays hydraulic pressure to the intensifier. When
the intensifier shifts, it is normal for the pressure to quickly fall and then rise again.
The directional valve consists of a spool with internal passages that direct hydraulic flow to one
end while returning fluid to the reservoir through the opposite end. Spool position is controlled
by a pair of solenoids, one at each end of the spool. The solenoids are alternately energized in
response to the position of the hydraulic piston as the proximity switch detects the end of the
stroke.
On redundant models, the 4-way directional control valve directs pressurized oil to one end of the
hydraulic cylinder and returns fluid to the reservoir from the opposite end, causing the intensifier
to stroke. The movement is controlled hydraulically by a pilot valve, electrically operated by two
solenoids. Indicators light up as each solenoid is energized. The directional control valve sends
flow to the hydraulic cylinder in one direction until the hydraulic piston activates the proximity
switch at the end of the stroke. The activated switch sends a signal to the controller to reverse the
direction of flow. The piston then moves in the opposite direction until it activates the proximity
switch at the opposite end of the stroke.
Summary of Contents for STREAMLINE S30
Page 1: ...MANUAL 20425545 R01 STREAMLINE S30 WATERJET INTENSIFIER OPERATION AND MAINTENANCE MANUAL ...
Page 66: ...Section 7 Electrical System 20425610 5 2005 Rev 0 7 2 Figure 7 1 Sensors and Solenoids ...
Page 139: ...Section 11 Parts List 20425652 5 2005 Rev 0 11 9 Figure 11 2 Intensifier Assembly ...
Page 143: ...Section 11 Parts List 20425652 5 2005 Rev 0 11 13 Figure 11 5 Hydraulic Piston Assembly ...
Page 145: ...Section 11 Parts List 20425652 5 2005 Rev 0 11 15 Figure 11 6 High Pressure Piping ...
Page 147: ...Section 11 Parts List 20425652 5 2005 Rev 0 11 17 Figure 11 7 Hydraulic Power Package ...
Page 149: ...Section 11 Parts List 20425652 5 2005 Rev 0 11 19 Figure 11 8 Motor Pump Assembly ...
Page 151: ...Section 11 Parts List 20425652 5 2005 Rev 0 11 21 Figure 11 9 Hydraulic Manifold Assembly ...
Page 153: ...Section 11 Parts List 20425652 5 2005 Rev 0 11 23 Figure 11 10 Hydraulic Hose Connections ...
Page 155: ...Section 11 Parts List 20425652 5 2005 Rev 0 11 25 Figure 11 11 Reservoir Assembly ...
Page 157: ...Section 11 Parts List 20425652 5 2005 Rev 0 11 27 Figure 11 12 Bulkhead Pipe Assembly ...
Page 159: ...Section 11 Parts List 20425652 5 2005 Rev 0 11 29 Figure 11 13 Electrical Assembly ...
Page 163: ...Section 11 Parts List 20425652 5 2005 Rev 0 11 33 Figure 11 15 Junction Box Configuration ...
Page 165: ...Section 11 Parts List 20425652 5 2005 Rev 0 11 35 Figure 11 16 Electrical Interface ...
Page 167: ...Section 11 Parts List 20425652 5 2005 Rev 0 11 37 Figure 11 17 Dump Valve Kit ...
Page 173: ...Section 11 Parts List 20425652 5 2005 Rev 0 11 43 Figure 11 20 Low Pressure Water Filter ...
Page 175: ...Section 11 Parts List 20425652 5 2005 Rev 0 11 45 Figure 11 21 Proportional Pressure Control ...
Page 179: ...Section 11 Parts List 20425652 5 2005 Rev 0 11 49 Figure 11 23 Intensifier Assembly ...
Page 181: ...Section 11 Parts List 20425652 5 2005 Rev 0 11 51 Figure 11 24 High Pressure Piping ...
Page 183: ...Section 11 Parts List 20425652 5 2005 Rev 0 11 53 Figure 11 25 Hydraulic Power Package ...
Page 185: ...Section 11 Parts List 20425652 5 2005 Rev 0 11 55 Figure 11 26 Motor Pump Assembly ...
Page 187: ...Section 11 Parts List 20425652 5 2005 Rev 0 11 57 Figure 11 27 Hydraulic Manifold Assembly ...
Page 189: ...Section 11 Parts List 20425652 5 2005 Rev 0 11 59 Figure 11 28 Hydraulic Hose Connections ...
Page 191: ...Section 11 Parts List 20425652 5 2005 Rev 0 11 61 Figure 11 29 Reservoir Assembly ...
Page 193: ...Section 11 Parts List 20425652 5 2005 Rev 0 11 63 Figure 11 30 Electrical Assembly ...
Page 195: ...Section 11 Parts List 20425652 5 2005 Rev 0 11 65 Figure 11 31 Control Box Configuration ...
Page 226: ......
Page 227: ......
Page 228: ......
Page 229: ......
Page 230: ......
Page 231: ......
Page 257: ......
Page 258: ......
Page 259: ......
Page 260: ......
Page 261: ......