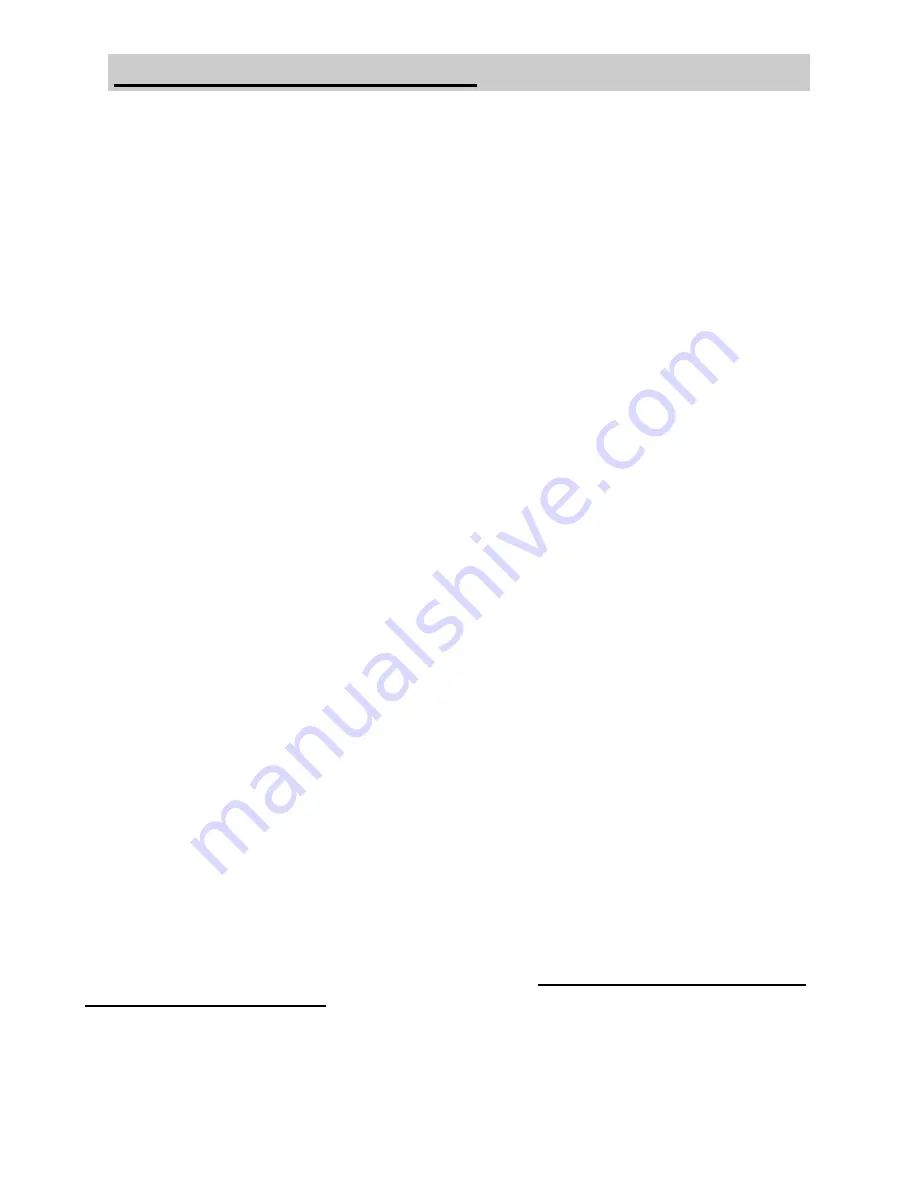
6
All safety and operating procedures reviewed
All hardware checked for tightness
Field adjustment procedures reviewed
Lubrication information reviewed
Machine fully lubricated
Hitch connection to implement information reviewed
Warranty information reviewed
RE-OPERATIONAL CHECKLIST:
FINAL ASSEMBLY ADJUSTMENTS AND
PRE-DELIVERY CHECK LIST
1. Check to make sure each ripper shank is located on desired row spacing and that all mounting bolts
are torqued properly.
2. Be sure jackstands are mounted securely with the bottom of the rear jackstands angled rearward.
3. Check alignment and spacing of each pair of disc gangs (see pages 14-44 for layout dimensions)
and are position same distance from row.
4. Make certain that disc gangs are set in same hole angle.
5. Make sure the safety reflectors are mounted correctly and located as near the ends of the tool bar as
possible.
6. If row markers are used, check to make sure they are assembled correctly (left marker on left end of
tool bar, right marker on right end of tool bar) and working freely.
7. If lift assist wheels are used, check to make sure they are assembled and mounted correctly with the
proper hydraulic connections.
8. Check toolbar gauge wheel and bedder gauge wheels, and lift assist wheel tires for proper air infla-
tion, and grease all grease fittings.
9. Double check all nuts and bolts for proper torque.
10. Store your Operator’s Manual in a safe and dry environment.
This manual must be delivered to
the customer with the machine.
Summary of Contents for 68 Series
Page 15: ...13 SAE GRADE 5 SAE GRADE 8 BOLT TORQUE CHART ...
Page 25: ...23 ...