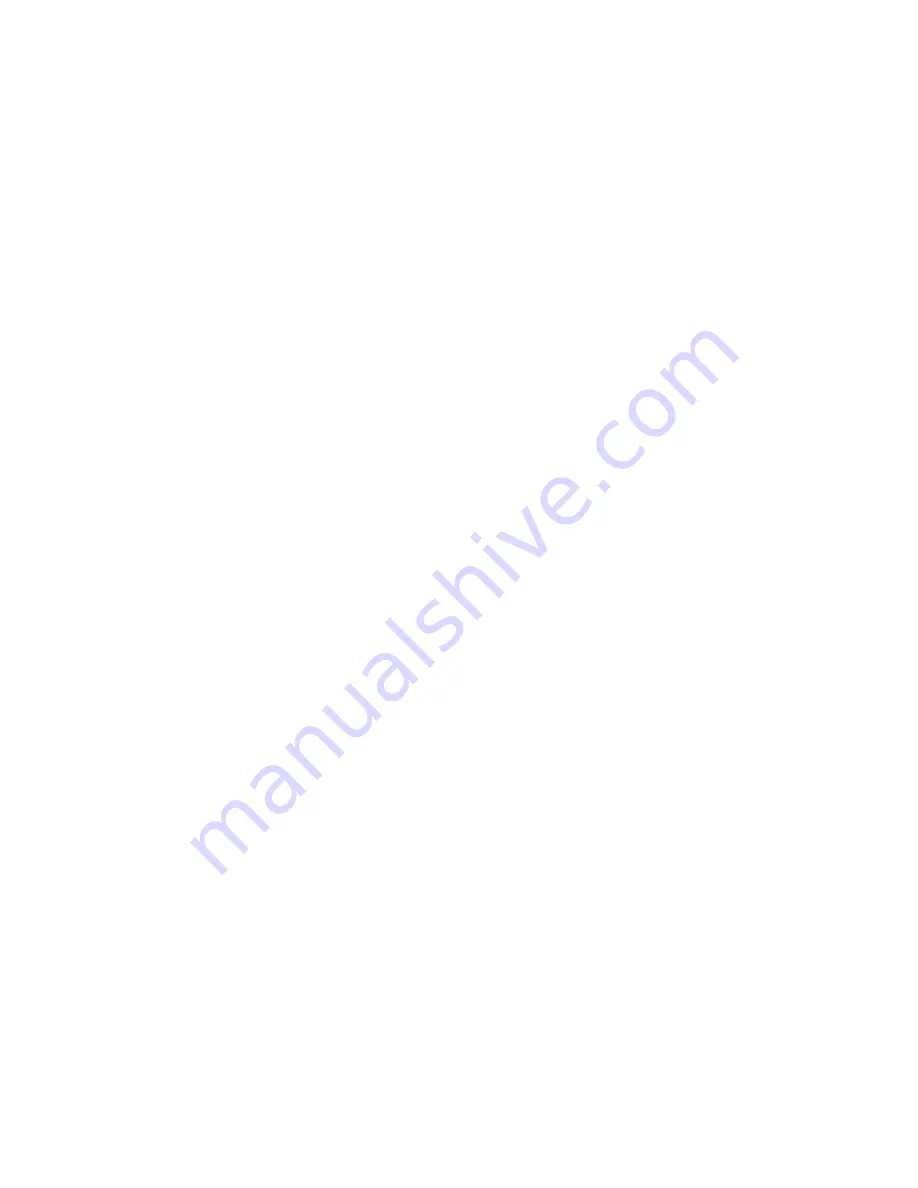
water level. As a consequence, the turbine flow meter will continue to count the litres of water
loaded until the set "number of safety pulses" corresponding to 7.8 litres is reached. At this point,
the timer closes the fill SV and activates the drain pump. When the tub is empty, the electronic timer
blocks the appliance and indicates E9.
Summary of Contents for DW6010
Page 1: ......
Page 2: ......
Page 13: ...A WATER SYSTEM ANCHOR POINTS Detail of motor mountings ...
Page 14: ...Detail of sump mounting ...
Page 21: ...1 ADJUSTING SCREW 2 TENSIONER 3 TENSIONER TRAVEL ...
Page 51: ......
Page 52: ......