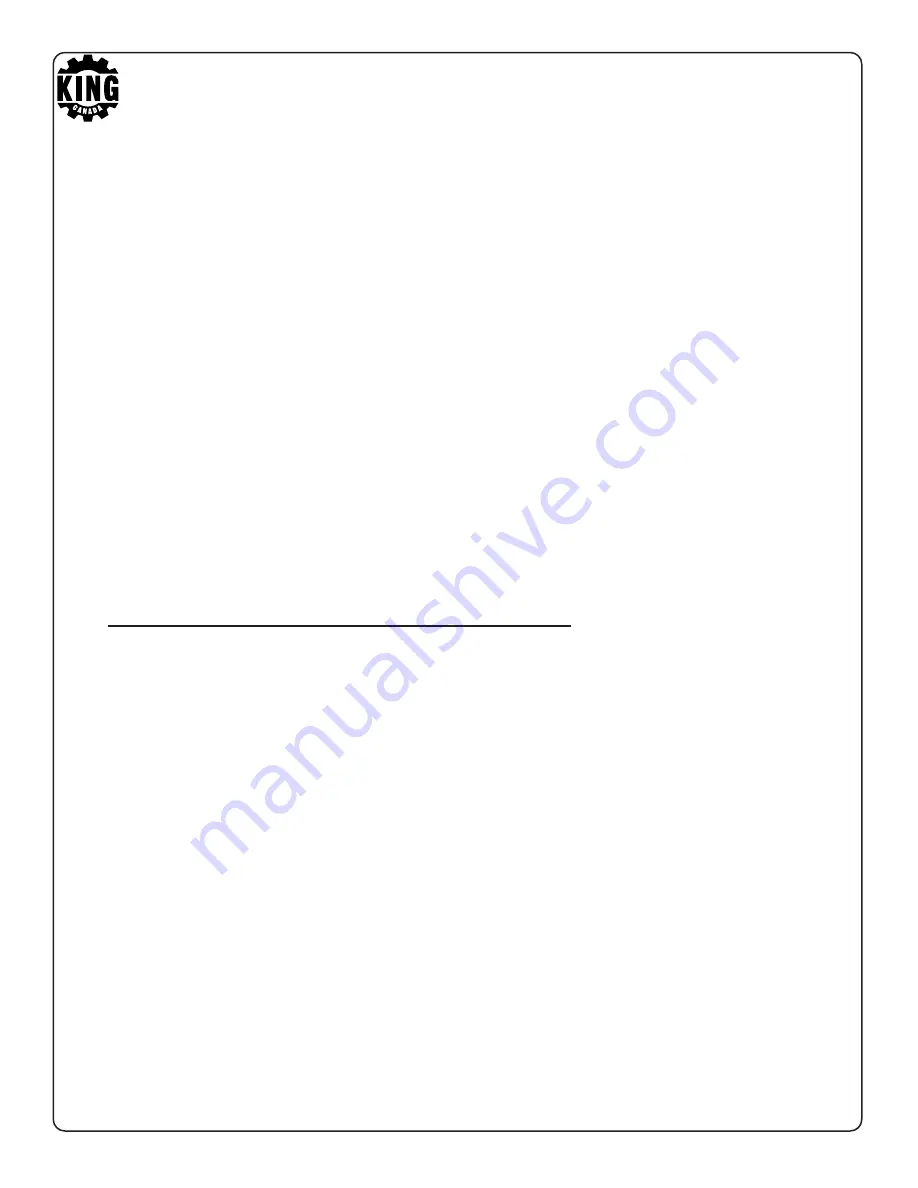
13. DO NOT OVERREACH.
Keep proper footing and balance at all times.
14. MAINTAIN MACHINE IN TOP CONDITION.
Keep machine clean for best and safest performance. Follow instructions for
lubricating and changing accessories.
15. DISCONNECT THE MACHINE FROM POWER SOURCE.
Before servicing and when changing accessories, or when mounting and
remounting motor.
16. USE RECOMMENDED ACCESSORIES
Consult the owners manual for recommended accessories.
17. CHECK DAMAGED PARTS.
Before further use of the machine, the guards and other parts should be carefully
inspected to ensure it will operate properly and perform its intended function.
Check for alignment of moving parts, binding of moving parts, mounting, and any other
condition that may affect its operation. Guards and other parts that are damaged
should be properly repaired or replaced.
18. NEVER LEAVE THE MACHINE RUNNING UNATTENDED.
SAFETY RULES FOR JOINTERS
1. KEEP
cutterhead sharp and free of all rust and pitch.
2. ALWAYS
use a push block when jointing stock that does not give reasonable distance
of safety for your hands.
3. NEVER
pass hands directly over the cutterhead.
4. ALWAYS
make sure exposed cutterhead behind the fence is guarded, especially
when jointing near the edge.
5. DO NOT
perform jointing or planing operations on material shorter than 8 inches,
narrower than 3/4 inch, or thinner than 1/2 inch.
6. MAINTAIN
the proper relationship between the infeed and outfeed table surfaces and
cutterhead knife path.
7. SUPPORT
the workpiece adequately at all times during operation, maintain
control of the work at all times.
8. DO NOT
back the workpiece towards the infeed table.
9. DO NOT
attempt to perform abnormal or little-used operations without study and use
of adequate holddown/push blocks, jigs, fixtures, stops, etc..
10. DO NOT
make cuts deeper than 1/8’’ in a single pass. On cuts more than 1/2’’ wide,
adjust depth of cut to 1/16’’ or less to avoid wood tearing.