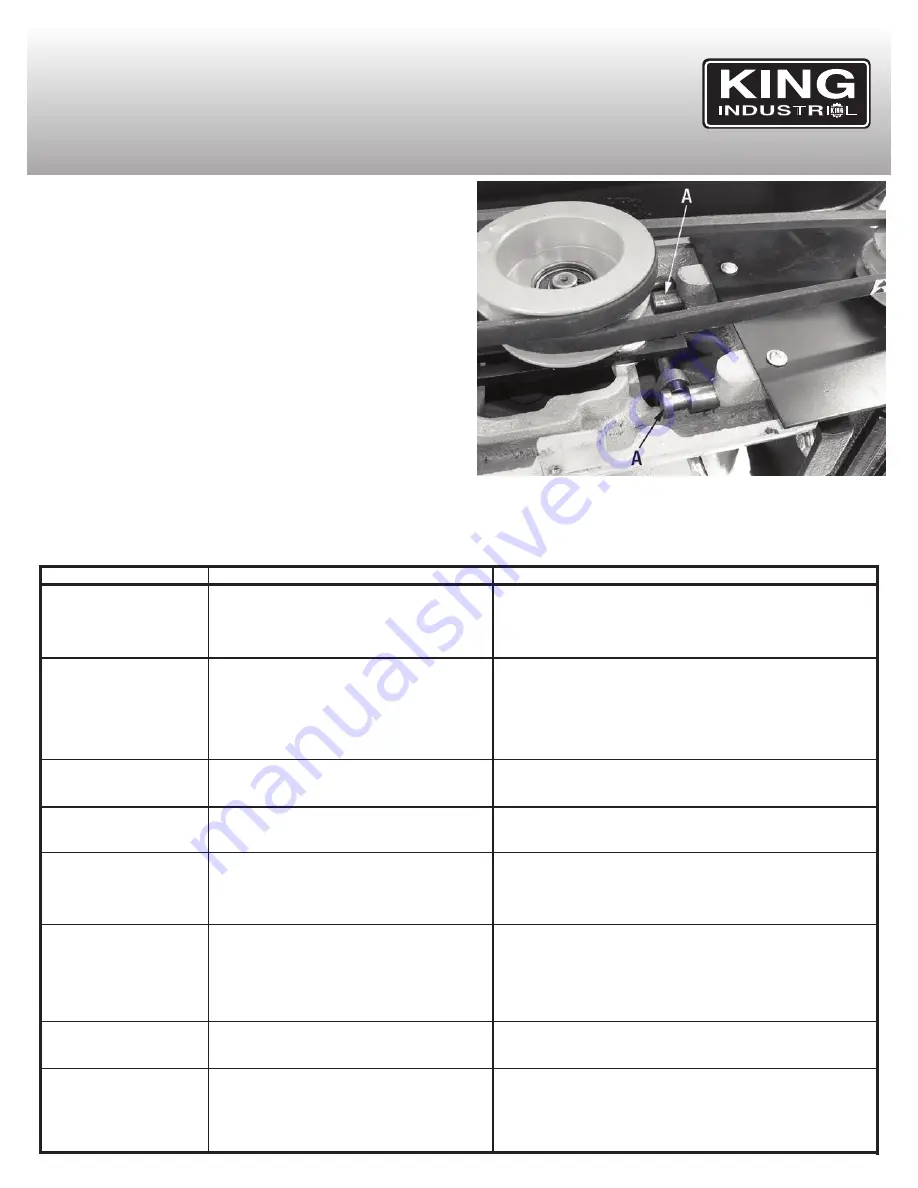
MAINTENANCE / TROUBLESHOOTING
MAINTENANCE
WARNING!
For your own safety, turn the switch “OFF” and remove the
plug from the power source before maintaining or lubricating your drill
press.
• Keep the Drill Press clean and free of dust and debris. Painted surfaces
can be wiped with a damp rag.
• Periodically lubricate all sliding or moving parts including the column and
rack (A & C) Fig.8 and the quill (C) Fig.16 (use any all purpose grease,
available at any hardware store).
• Lightly grease the belt tension slide bars (A) Fig.23 every two months or
as needed depending on frequency of use.
• Bearings in the quill and the V-belt pulleys are sealed and permanently
lubricated – no further lubrication is required.
•
Frequently blow out any dust that may accumulate inside the motor. After
operation, remove chips or dirt on the machine and apply a coat of furniture-type paste wax to the table and the column, this will help keep the
surfaces clean and free of rust.
PRObLEM
Noisy operation.
Drill bit burns.
Wood splinters on un-
derside of workpiece.
Workpiece torn loose
from hand.
Drill bit binds in work-
piece.
Excessive drill bit
wobbling.
Quill returns too fast or
too slow.
Chuck will not stay at-
tached to the spindle. It
falls off when trying to
install it.
PRObAbLE CAUSE
1. Incorrect belt tension.
2. Dry spindle.
3. Loose spindle pulley.
4. Loose motor pulley.
1. Incorrect speed.
2. Chips not comming out of hole.
3. Dull drill bit.
4. Feeding too slow.
5. Not lubricated.
1. No “Back-up material” under the work-
piece.
1. Not supported or clamped properly.
1. Workpiece is pinching the drill bit or there
is an excessive feeding pressure.
2. Improper belt tension.
1. Bent drill bit.
2. Worn spindle bearings.
3. Drill bit is not properly installed in the
chuck.
4. Chuck not properly installed.
1. Spring has improper tension.
1. Dirt, grease or oil on the tapered inside
surface of the chuck or on the spindle ta-
pered surface.
SOLUTION
1. Adjust the tension.
2. Lubricate the spindle.
3. Tighten the retaining nut on the pulley as needed.
4. Tighten the set screws which hold the puleys in place.
1. Change the speed.
2. Retract the drill bit frequently to clear the chips.
3. Resharpen the drill bit.
4. Feeding too fast...allow the drill bit to cut.
5. Lubricate the drill bit with cutting or motor oil.
1. Support the workpiece or clamp it.
1. Support the workpiece or clamp it.
1. Support the workpiece or clamp it.
2. Adjust the tension of the belt.
1. Use a straight drill bit.
2. Replace the bearings.
3. Install drill bit properly.
4. Install chuck properly.
1. Adjust the spring tension.
1. Using a household detergent, clean the tapered surfaces
of the chuck and the spindle to remove the dirt, grease
and oil.
FIGURE 23