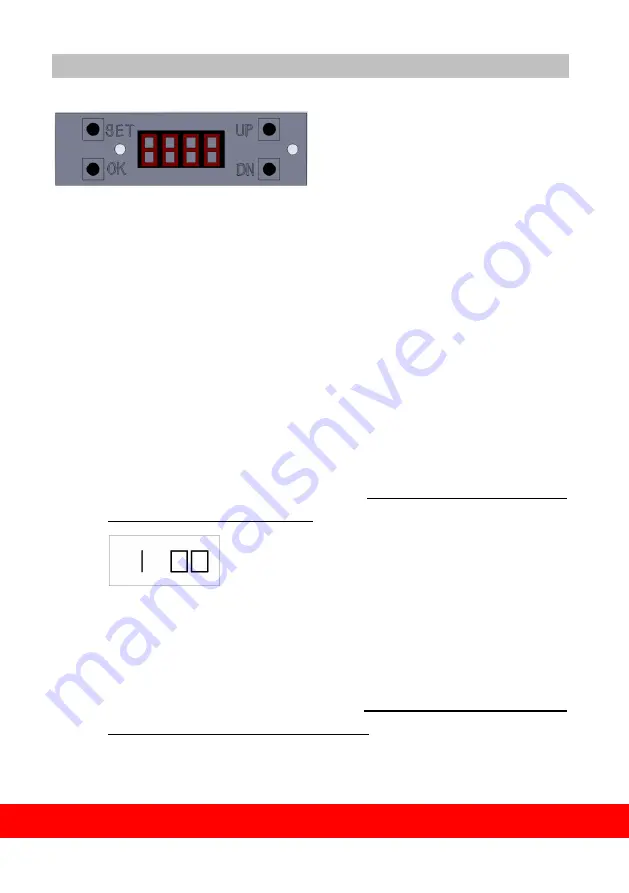
17
OPERATION MANUAL
A.
DISPLAY PANEL
B.
FUNCTIONS OF KEYS ON PANEL
SET
:
SET FUNCTION
OK
:
CONFIRM (COUNTER FUNCTION
)
UP
:
INCREASE VALUE
(
ADDEND KEY
)
DOWN
:
DECREASE VALUE
(
SUBTRAHEND KEY
)
C.
DESCRIPTON OF FUNCTION
1. Total counting status
:
Press OK to switch the status for counting value
automatically or setting counting.
2. Default setting
:
Either in operation or standby status, press the SET+OK
in 3 seconds that LED displays flicker 3 seconds with beep to remind the
system turn back default setting.
3. SET FUNCTION
3.1
Either in operation or standby status,
press SET 1 time in 3 seconds
to configure counting setting,
LED monitor shows flicker,
press UP or DN to increase or decrease the numbers
(
Default setting is 00, and the setting range is 00-99
)
, With or without
pressing any key in 3 seconds, setting will be completed with buzzer alert.
※
Note
:
If it is not into setting counting status, please press OK to switch the
status.
3.2
Either in operation or standby status,
press SET 2 times to configure
increasing or decreasing progressively
, LED monitor shows flicker,