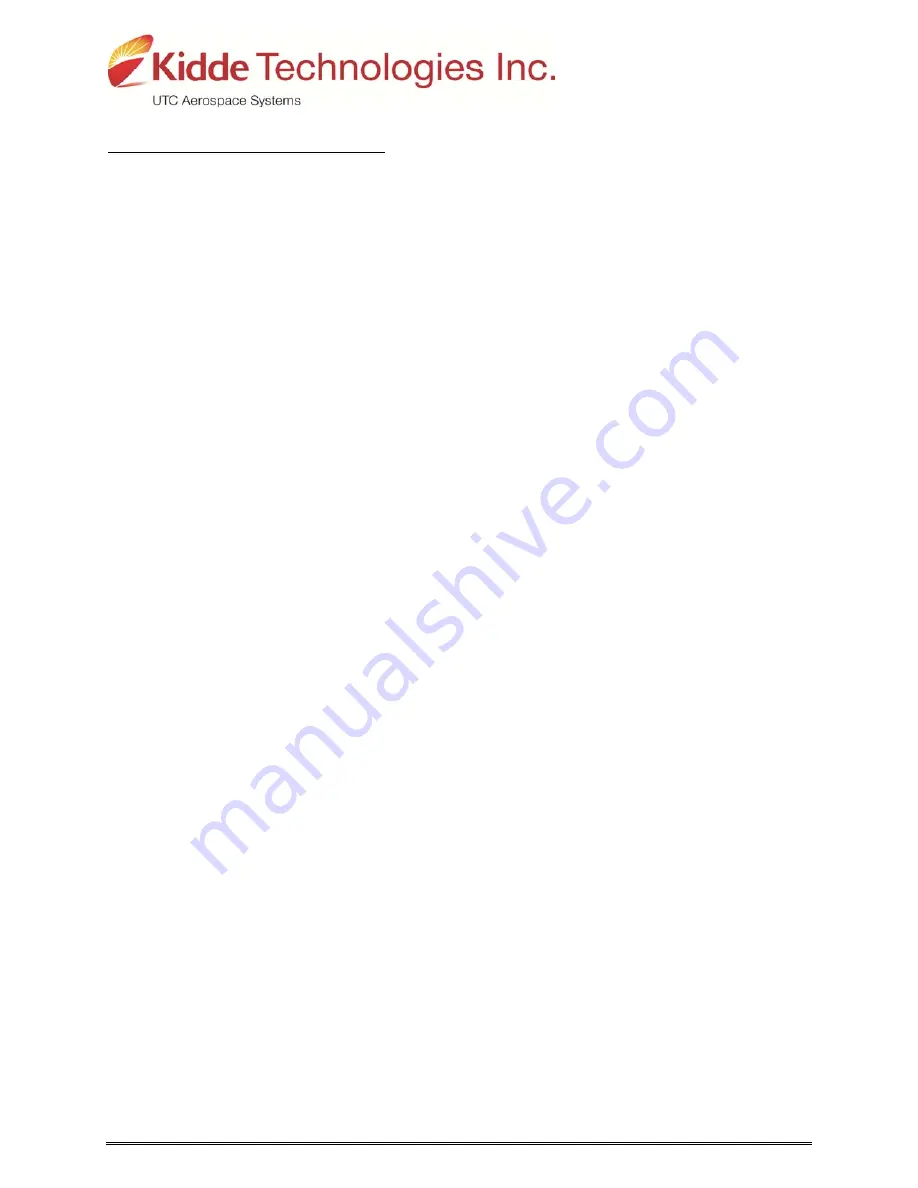
181922 Rev B
15
Controlled by ECCN:EAR99
PROPRIETARY INFORMATION –
Refer to the restrictions provided on the Title Page of this document.
EAR DATA
- Subject to the export control restrictions on the Title
Page of this document or file
Extinguisher & Distribution System
Verify the extinguisher is oriented correctly.
Verify the extinguisher pressure gauge pointer is in the green arc at room temperature.
Verify distribution piping and nozzles are intact, unobstructed, and that nozzle blow-off
caps are in place.
Visually inspect the extinguisher for damage such as pits, gouges, dents, or corrosion. If
a pit, gouge, or cut exceeds a depth of 0.08 inches; if the depth of a dent exceeds 0.25
inches or one-tenth of the average diameter of the dent; or corrosion exceeds a depth of
0.05 inches or a coverage area larger than 15% of the extinguisher’s outer surface, have
the extinguisher evaluated by a qualified fire protection
equipment company familiar with
Kidde equipment.
EVERY 18000 MILES OR SEMI-ANNUALLY (WHICHEVER OCCURS FIRST)
Perform a comprehensive fire system test according to KAD Generic AFSS Checkout
Procedure, R10027 using a Kidde Fire System Test Set (Thermal Detection Test Kit P/N
4208971-1)
Perform a comprehensive gas leak system test using the KAD Gas Sensor Test Kit, P/N
420756, for CNG, LNG, and Propane.
EVERY SIX YEARS
Have the fire extinguisher assembly rebuilt and inspected by a qualified fire protection
equipment company familiar with Kidde equipment. The date of manufacture of the
extinguisher assembly is stamped (MM/YY) on the top neck of the cylinder. This is the date
that should be used to determine the 6 year service interval date.
EVERY TWELVE YEARS
Have the fire extinguisher cylinder hydrostatically tested by a qualified fire protection
equipment company familiar with Kidde equipment. The date of manufacture of the cylinder
is stamped (MM/YY) on the neck of the cylinder. This is the date that should be used to
determine the12 year service interval date.
ADDITIONAL INSPECTIONS
A thorough inspection should be performed after any major engine work is done to ensure
components have not been damaged or relocated.