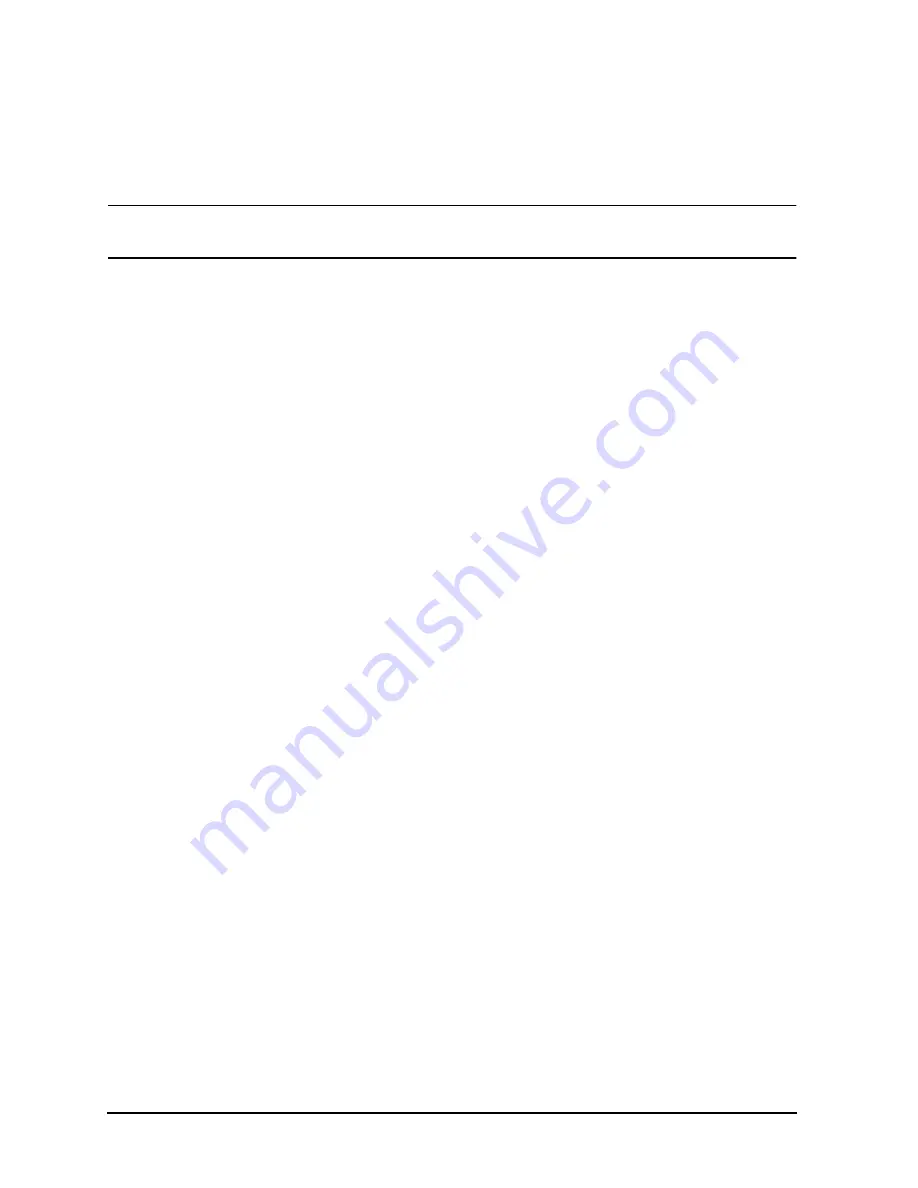
3- 8
85054B
Use, Maintenance, and Care of the Devices
Gaging Connectors
Gaging Procedures
Gaging Male Type-N Connectors
NOTE
Always hold a connector gage by the gage barrel, below the dial indicator. This
gives the best stability, and improves measurement accuracy.
1. Select the proper gage for your connector. (Refer to
for the gage set part number).
2. Inspect and clean the gage, gage master, and device to be gaged. Refer to
and
3. Zero the connector gage (refer to
a. While holding the gage by the barrel, and without turning the gage or the gage master,
screw the gage master connecting nut onto the male gage, just until you meet
resistance. Connect the nut finger tight. Do not overtighten.
b. Use the torque wrench recommended for use with this kit to tighten the connecting nut to
135 N-cm (12 in-lb). Refer to
for more information.
c. Loosen the dial lock screw on the gage and rotate the gage dial so that the pointer
corresponds to the correction value noted on the gage master. Do not adjust the gage
dial to zero, unless the correction value on the gage master is zero.
d. Tighten the dial lock screw and remove the gage master.
e. Attach and torque the gage master to the gage once again to verify that the setting is
repeatable. Remove the gage master.
4. Gage the device connector (refer to
):
a. While holding the gage by the barrel, and without turning the gage or the device, screw
the connecting nut of the device being measured onto the gage, just until you meet
resistance. Connect the nut finger-tight. Do not overtighten.
b. Use the torque wrench recommended for use with this kit to tighten the connecting nut to
135 N-cm (12 in-lb). Refer to
for more information.
c. Gently tap the barrel of the gage with your finger to settle the gage reading.
d. Read the gage indicator dial. If the needle has moved clockwise, the center conductor is
protruding
by an amount indicated by the
black
numbers. If the needle has moved
counterclockwise, the center conductor is
recessed
by an amount indicated by the
red
numbers.
For maximum accuracy, measure the connector a minimum of three times and take an
average of the readings. After each measurement, rotate the gage a quarter-turn to
reduce measurement variations that result from the gage or the connector face not being
exactly perpendicular to the center axis.
e. Compare the average reading with the observed pin depth limits in
Summary of Contents for 85054B
Page 1: ...Keysight Technologies 85054B 50 Type N Calibration Kit User s and Service Guide...
Page 2: ......
Page 3: ...85054B...
Page 7: ...1 General Information...
Page 15: ...2 Specifications...
Page 20: ...2 6 85054B Specifications Electrical Specifications...
Page 21: ...3 Use Maintenance and Care of the Devices...
Page 43: ...4 Performance Verification...
Page 46: ...4 4 85054B Performance Verification Recertification...
Page 47: ...5 Troubleshooting...
Page 52: ...5 6 85054B Troubleshooting Contacting Keysight...
Page 53: ...6 Replaceable Parts...
Page 58: ...6 6 85054B Replaceable Parts Introduction...
Page 59: ...A Standard Definitions...
Page 64: ...Index 85054B Index 4 part number 6 2 Z zeroing connector gage 3 8 3 10 3 12...