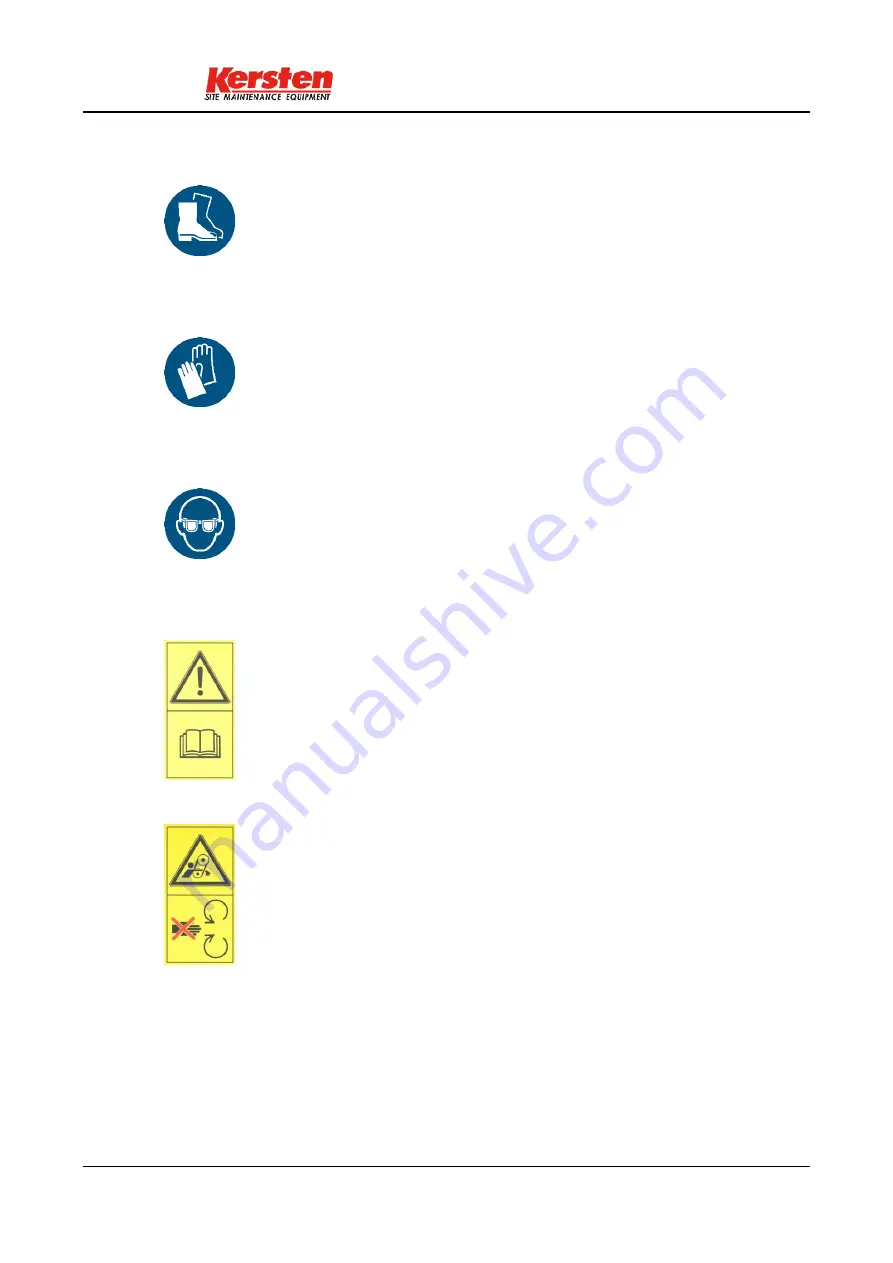
UBS Hydro II
Safety
EN
2018-05-02
9 / 60
Wear protective shoes
This sign indicates that protective shoes are to be worn in the respective area.
Safety shoes protect your feet from crushing, falling parts and slipping on slippery
floor.
Wear protective gloves
This sign indicates that protective gloves are to be worn in the respective area.
Wear protective gloves to protect your hands from friction, abrasion, punctures,
cuts or deep injuries, as well as from contact with hot surfaces.
Wear safety glasses
This sign indicates that safety glasses are to be worn in the respective area.
Safety glasses shall protect the eyes from particles flying around and splashing
fluid.
Operating Instructions and Safety Instructions
Before commissioning, read and observe the Operating Instructions and the safety
instructions.
Never open or remove the safeguards with the engine running.