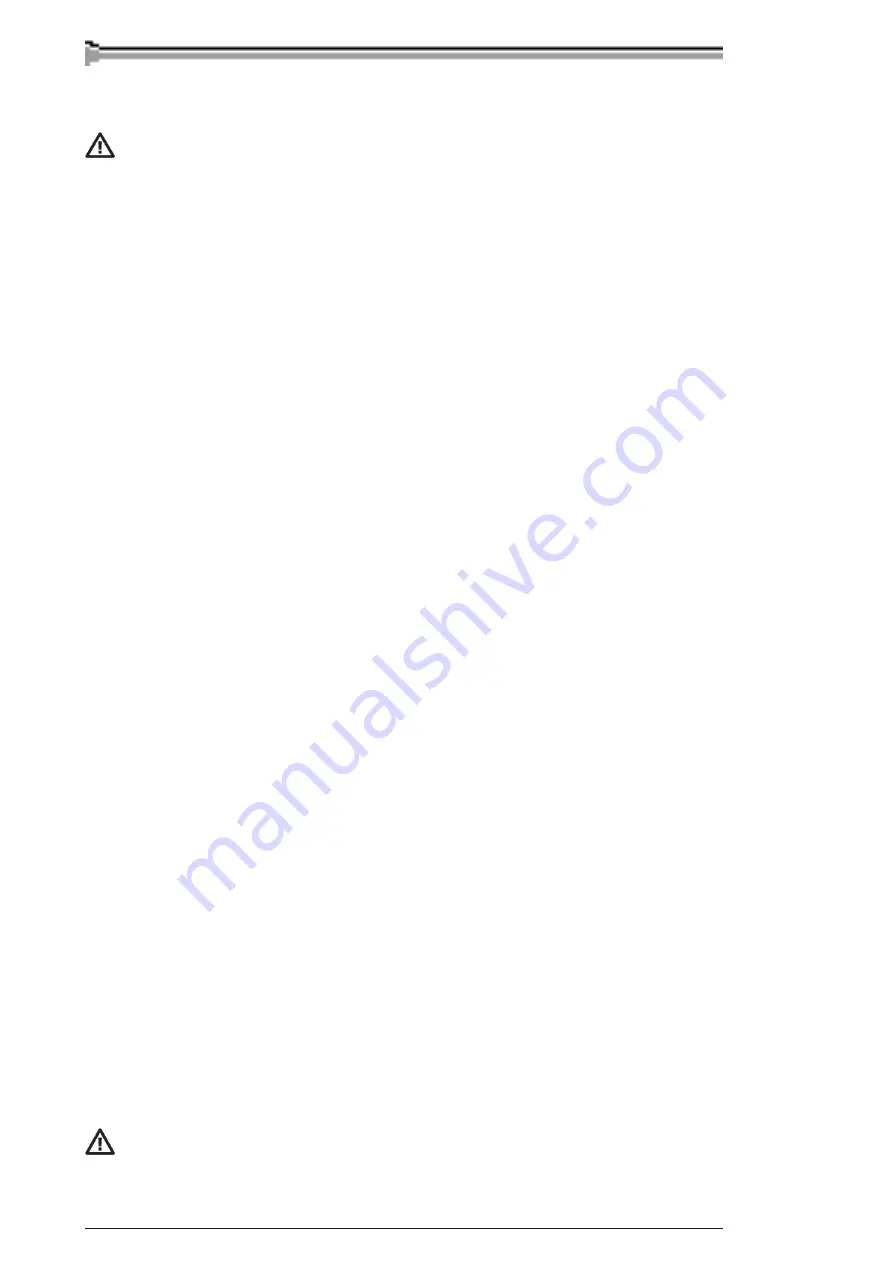
12 – Pro 3200 Evolution, Pro 4200 Evolution, Pro 5200 Evolution/0109
©
COPYRIGHT
KEMPPI
OY
6.2. POWER SOURCE
Note! Disconnect the plug of the machine from the mains socket and wait
approx. 2 minutes (capacitor charge) before removing the cover plate.
Check at least every half year:
- Electric connectors of the machine - clean the oxidized parts and tighten the loosened ones.
- Note! You must know correction tension torques before starting the reparation of the joints.
- Clean the inner parts of the machine from dust and dirt e.g. with a soft brush and vacuum
cleaner. Also clean the ventilation net behind the front grate.
- Do not use compressed air, there is a risk that dirt is packed even more tightly into gaps
of cooling profiles.
- Do not use pressure washing device.
- Only authorized electrician shall carry out repairs to the machines.
6.3. REGULAR MAINTENANCE
Kemppi Service Shops make regular maintenance according to agreement.
The major points in the maintenace procedure are listed as follows:
- Cleaning of the machine
- Checking and maintenance of the welding tools
- Checking of connectors, switches and potentiometers
- Checking of electric connections
- Meter checking
- Checking of mains cable and plug
- Damaged parts or parts in bad connection are replaced by new ones
- Maintenace testing. Operation and performance values of the machine are checked, and
adjusted when necessary by means of test equipment.
7. OPERATION DISTURBANCES
In case of problems contact the Kemppi works in Lahti, Finland, or your local Kemppi dealer.
Check the maintenace objects before the machine is sent to the Service Repair Shop.
7.1. OPERATION OF THE OVERLOAD PROTECTION
Yellow pilot lamp H12 of thermal protection is illuminated when thermostat has
operated due to overheating of machine.
7.2. CONTROL FUSES
Fuse F11, 6,3 A slow-blow, on the rear wall of machine is as protection for
connection of auxiliary devices X14-15.
Voltage unit for auxiliary devices (1~230 V/240 VA) has a fuse of its own F12 1,0 A slow-blow.
Use same type and rating of fuse which is marked beside the fuse adapter.
Damage caused by a wrong type fuse is not covered by the guarantee.
The thermostat of machine will operate, if machine is continuously loaded over rated values or
cooing air circulation is blocked.
Cooling fan cools down the machine and when the pilot lamp is not illuminated the machine
is automatically ready for welding.