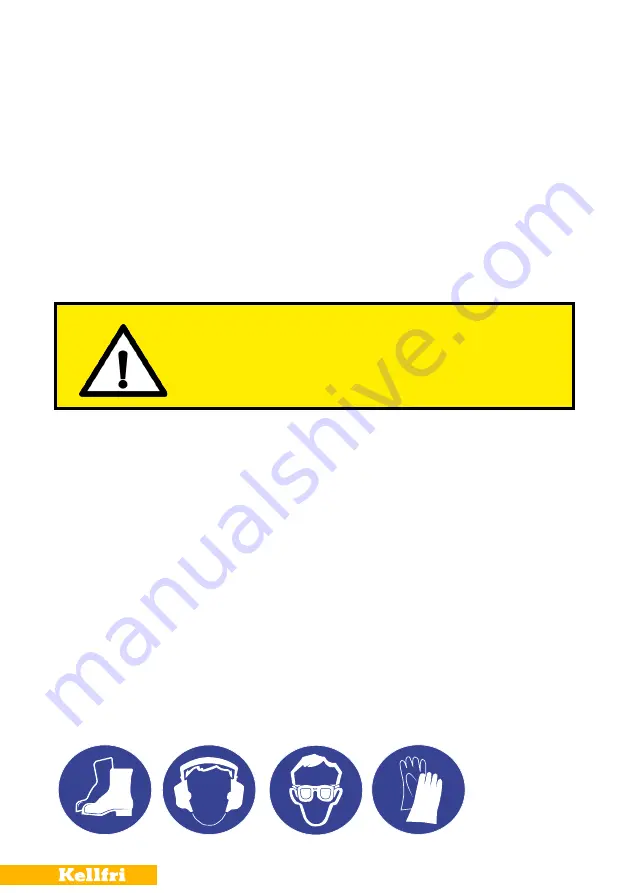
4
SAFETY INSTRUCTIONS
Before using the equipment or product, and for the safety of yourself and others, you must
read the safety instructions and operating manual and understand their contents. Always keep
the safety instructions and operating manual handy for users of the equipment or product.
For the safety of both yourself and others, it may be a good idea to read through the safety
instructions every now and then. If the safety instructions or the operating manual are
damaged, or become unusable for any other reason, new copies may be ordered from:
Kellfri AB, Storsvängen 2, 532 38 SKARA, Sweden.
The safety instructions can also be downloaded from Kellfri’s website:
www.kellfri.co.uk
Do not use the equipment or product if you feel ill, tired or are under the influence of alcohol.
Do not use the equipment or product if you are taking prescribed medication or drugs,
or suffering from severe depression or mental illness. Always comply with general rules of the
road and applicable rules stipulated by animal welfare legislation. People under the age of 15
are not allowed to use the equipment.
INSTRUCTIONS FOR EMERGENCY SITUATIONS
In case of emergency, call 112.
Always have a mobile phone or emergency phone available when working alone. A first-aid
kit and fire extinguisher must be kept in an easily accessible location when carrying out any
work, maintenance or service.
Warning!
The original design of the machine must not, under any circumstances, be modified without
the approval of the manufacturer. Unauthorised modifications and/or accessories may cause
life-threatening injuries or death to users and others.
PERSONAL PROTECTION
Always use suitable protection equipment. Do not wear loose clothing or jewellery while
working with the equipment. Long hair should be tied up when working with equipment
that has moving parts. Use protective gloves to avoid the risk of burns if hot surfaces such
as exhaust pipes are touched, and to avoid oil and petrol getting in contact with the skin.
Ear defenders must be worn whilst the motor is running.
Kellfri is not liable for any modifications, changes or rebuilds carried out by customers.
Where the machine is used professionally, employers are responsible for ensuring that users of the
machine have theoretical and practical knowledge of the machine and that work is performed
in a safe manner. Stay informed by complying with work environment legislation; contact your
local work environment authority.
Summary of Contents for 35-HKK
Page 19: ...19 Table of contents Refit the sleeve FIGURE 5 FIGURE 7 FIGURE 6 3 Fit the wheels ...
Page 26: ...26 Table of contents FIGURE 1 TOW BAR ...
Page 28: ...28 Table of contents FIGURE 2 WHEELS AND SUSPENSION ...
Page 30: ...30 Table of contents FIGURE 3 CUTTING HEAD ...
Page 33: ...33 Table of contents NOTES ...
Page 34: ...34 Table of contents NOTES ...