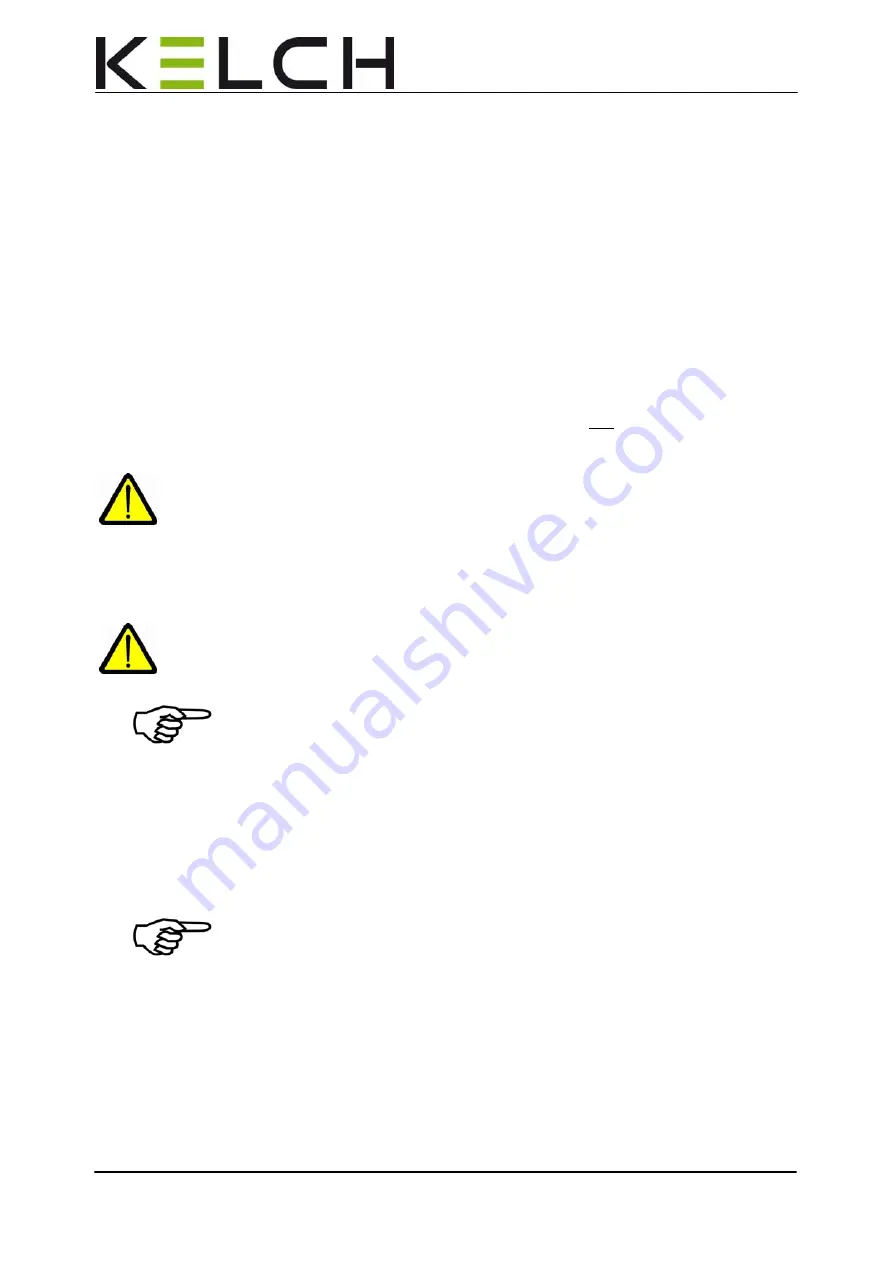
5. Maintenance and care
KENOVA set line V9xx(-S)
© Kelch GmbH 2014
Kelch GmbH · Werkstraße 30 · D-71384 Weinstadt-Endersbach · Tel. (+49)7151 20522 0 · Fax (+49)7151 20522 11 · [email protected]
Page 30
5.2 Inspection
To detect possible occurrence of damage in good time and ensure uninterrupted pro-
duction, a monthly visual inspection of the operational sequences is necessary.
5.3 Cleaning
Make sure that the functional parts on the appliance remain clear of swarf.
The functioning of the appliance can be ensured by regularly cleaning the appliance
using a soft, lint-free cloth and lubricating metal surfaces with a little preservative agent
such as silicone oil. A cold-cleaning agent is preferred for cleaning the machine compo-
nents
For conspicuous contamination, cleaning can also be carried out using commercial
glass cleaner.
Machine components, when delivered, are covered with a corrosion protection.
Chlorinated hydrocarbons such as PER, TRI or similar may not be used to clean ma-
chine components or remove the corrosion protection.
Caution!
Risk of damaging the appliance
Under no circumstances use a steam jet, water jet or compressed
air! Here, there is the risk that contamination and cleaning agent
can penetrate into the guides and seals. This can cause functions –
in particular safety functions, limit switches or measurement sys-
tems – to be disabled.
Caution!
Danger of fire
If benzine is used, the cleaning must take place outdoors and spe-
cial precautions must be taken.
Note!
The cleaning liquid that runs off must be collected and pro-
fessionally disposed of.
5.4 Maintenance
All roller bearings have sealed-for-life lubrication.
Any grease nipples that my still be present are standard elements on the corresponding
components. Further greasing is however not necessary because of the low loading.
We recommend having maintenance work carried out by KELCH specialists to enable
the expectations for long-term precision and outstanding quality to be met.
Note!
The yearly maintenance work may only be carried out by
Kelch GmbH specialists!
Pressure hoses and lines as well as their screw fittings are to be inspected for damage
at regular intervals and be replaced without delay – even at the slightest signs of dam-
age.
Summary of Contents for KENOVA set line V9 Series
Page 2: ......