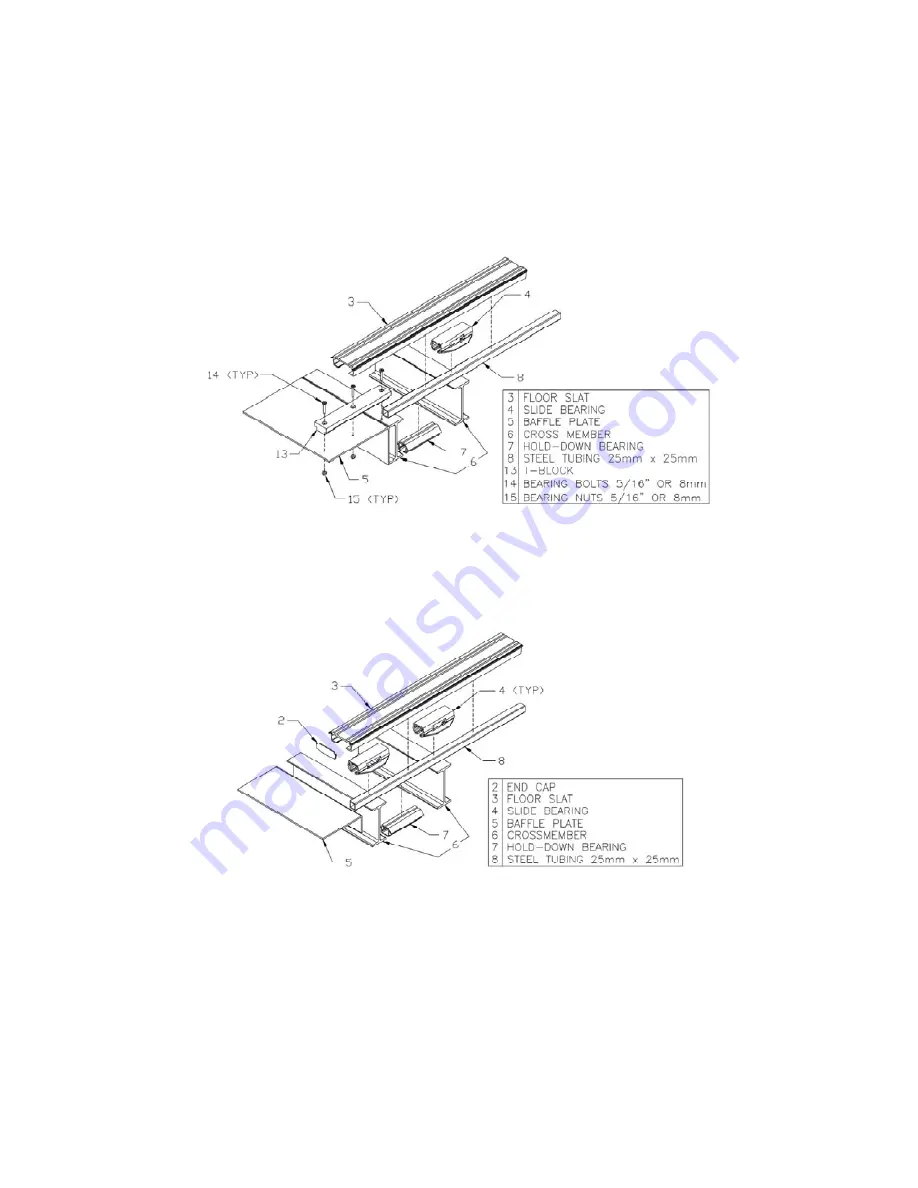
4) T-block.
A plastic T-block provides a sliding surface and prevents material from going
underneath slats/planks. T-blocks are not recommended for use with highly
abrasive materials.
5) NO end sub-deck
The absence of an end sub-deck is undesirable because it leaves no support for
ends of slats/planks.
NOTES:
The first three options include a wear pad bearing in the floor slats/planks.
The square sub-deck material can extend to 12mm from the doors for all options.
1. Install the selected end sub-deck following these instructions:
Summary of Contents for Running Floor II Metric
Page 31: ...Figure 38 Figure 37 50mm...
Page 40: ...25044 Figure 45...