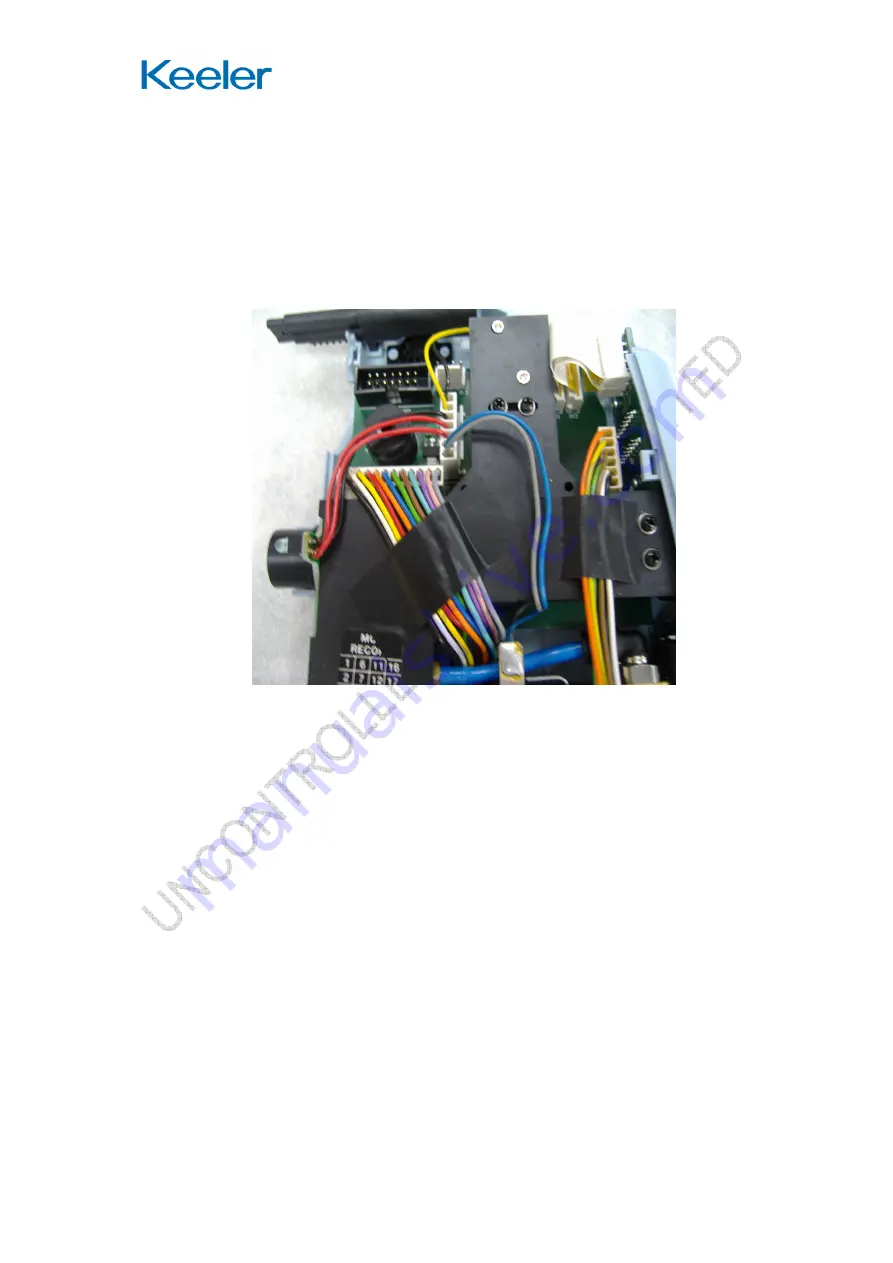
Intellipuff Service Manual
Page 47 of 51
Issue D 27/02/2014
EP59-12317
Main LED, Target LEDs Do Not Light and Solenoid Does not Fire
Suggested Solution:
1. Check for wire cuts and that the crimp terminals are not lose
2. Measure Voltage levels between the various PINS as shown in the
above PIN assignment table above.
Figure 5. PL1, PL2 & PL4 Connectors