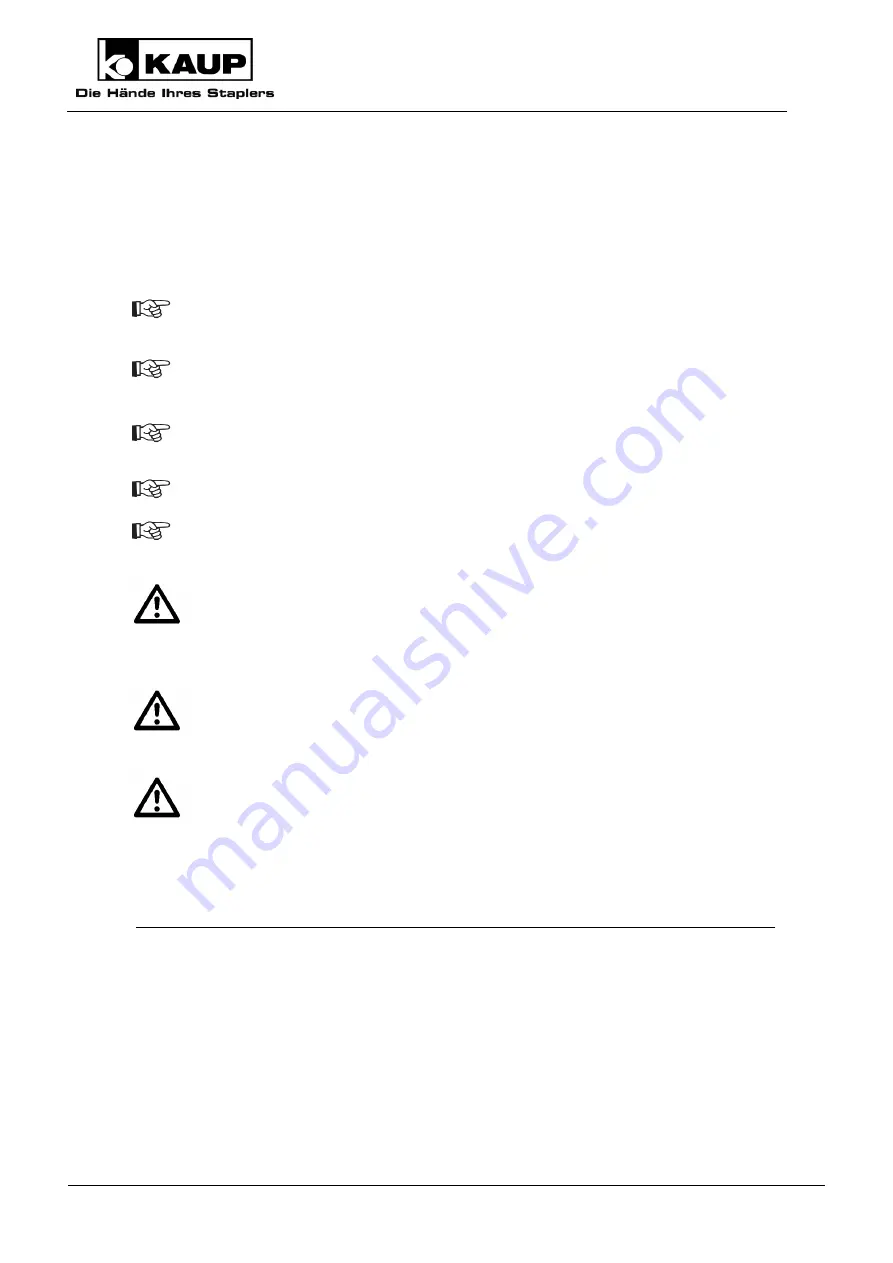
Operating Manual
14
Original Operating Manual
6.
Maintenance and servicing
6.1
General
Regular maintenance is essential to ensure reliable operation and long service life of the KAUP
attachment
.
Ensure that maintenance and servicing are performed by qualified and authorised
personnel only.
Lubrication and cleaning work on the attachment may also be performed by the lift truck
operator.
Perform maintenance and servicing work only when the attachment is parked securely
on a stable, level foundation. For installing and removing, it is recommended to use a
pallet to take the attachment. The attachment can thus be securely placed and
transported.
Pay attention to a sufficient load-carrying capacity of the lifting means.
Replace missing or defective warning signs on the attachment.
Do not use third party spare parts. Through poor quality or incorrect matching
they can result in a risk of accident. The EC Declaration of Conformity by the
manufacturer becomes invalid and you assume full responsibility in the case of
accident.
Use only original spare parts from the manufacturer.
The hydraulic system is under pressure. During work on hydraulic components
oil spurting out can cause injuries. Unload the system in accordance with the
operating instructions of the lift truck manufacturer. In the case of injuries caused
by high pressure oil, inform the works physician and seek out a specialist
immediately.
Screw connections can loosen due to vibration of the attachment. During routine
maintenance check that screw connections are correctly torqued and replace
screws which are visibly damaged.
Note the following tightening torques which are valid for screws with connecting surfaces according
to ISO 4762, ISO 4014, ISO 4032 etc.:
Screw / bolt rating
8.8
10.9
12.9
M6 thread
9,3Nm
14Nm
16Nm
M8 thread
23Nm
33Nm
39Nm
M10 thread
45Nm
66Nm
77Nm
Μ12 thread
77Nm
115Nm
135Nm
Μ16 thread
190Nm
280Nm
330Nm
Μ20 thread
385Nm
550Nm
640Nm