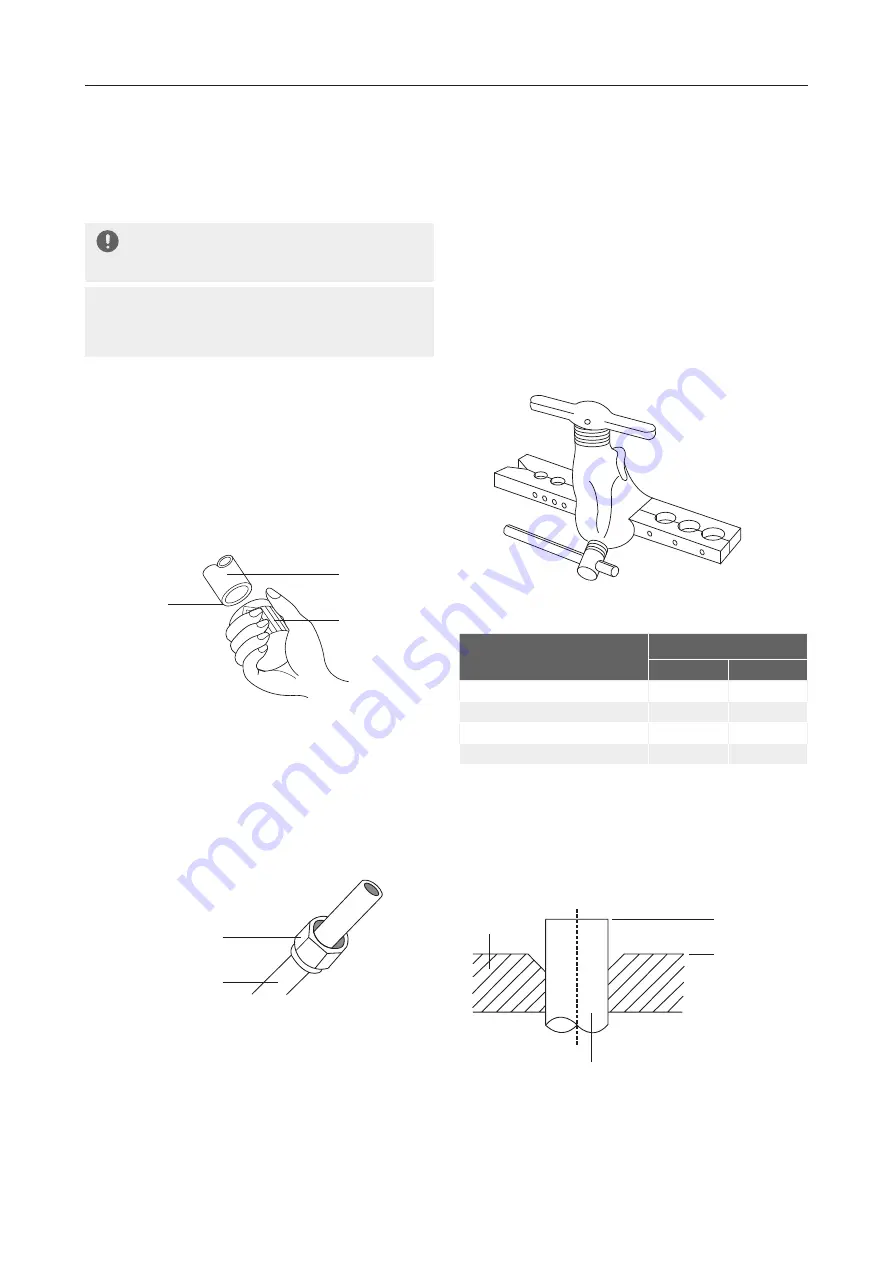
26
| Kaden Installation Manual
DO NOT DEFORM PIPE
WHILE CUTTING
Be extra careful not to damage, dent, or deform the
pipe while cutting. This will drastically reduce the heating
efficiency of the unit.
Step 2: Remove burrs
Burrs can affect the tight seal of refrigerant piping connection.
They must be completely removed.
1. Hold the pipe at a downward angle to prevent burrs from
falling into the pipe.
2. Using a reamer or deburring tool, remove all burrs from the
cut section of the pipe.
Step 3: Flare pipe ends
Proper flaring is essential to achieve a tight seal.
1. After removing burrs from cut pipe, seal the ends with PVC
tape to prevent foreign materials from entering the pipe.
2. Sheath the pipe with insulating material.
3. Place flare nuts on both ends of pipe. Make sure they are
facing in the right direction, because you can’t put them on
or change their direction after flaring.
4. Remove PVC tape from ends of pipe when ready to
perform flaring work.
5. Clamp flare form on the end of the pipe. The end of the
pipe must extend beyond the edge of the flare form in
accordance with the dimensions shown in the table below.
Flare connection size (A)
A (mm)
Min.
Max.
Ø 6.35
0.7
1.3
Ø 9.52
1.0
1.6
Ø 12.70
1.0
1.8
Ø 15.88
2.0
2.2
6. Place flaring tool onto the form.
7. Turn the handle of the flaring tool clockwise until the pipe is
fully flared.
8. Remove the flaring tool and flare form, then inspect the end
of the pipe for cracks and even flaring.
A
Flare form
Pipe
Pipe
Deburrer
Point down
Copper pipe
Flare nut
Summary of Contents for KSI Series
Page 44: ...kadenair com au...