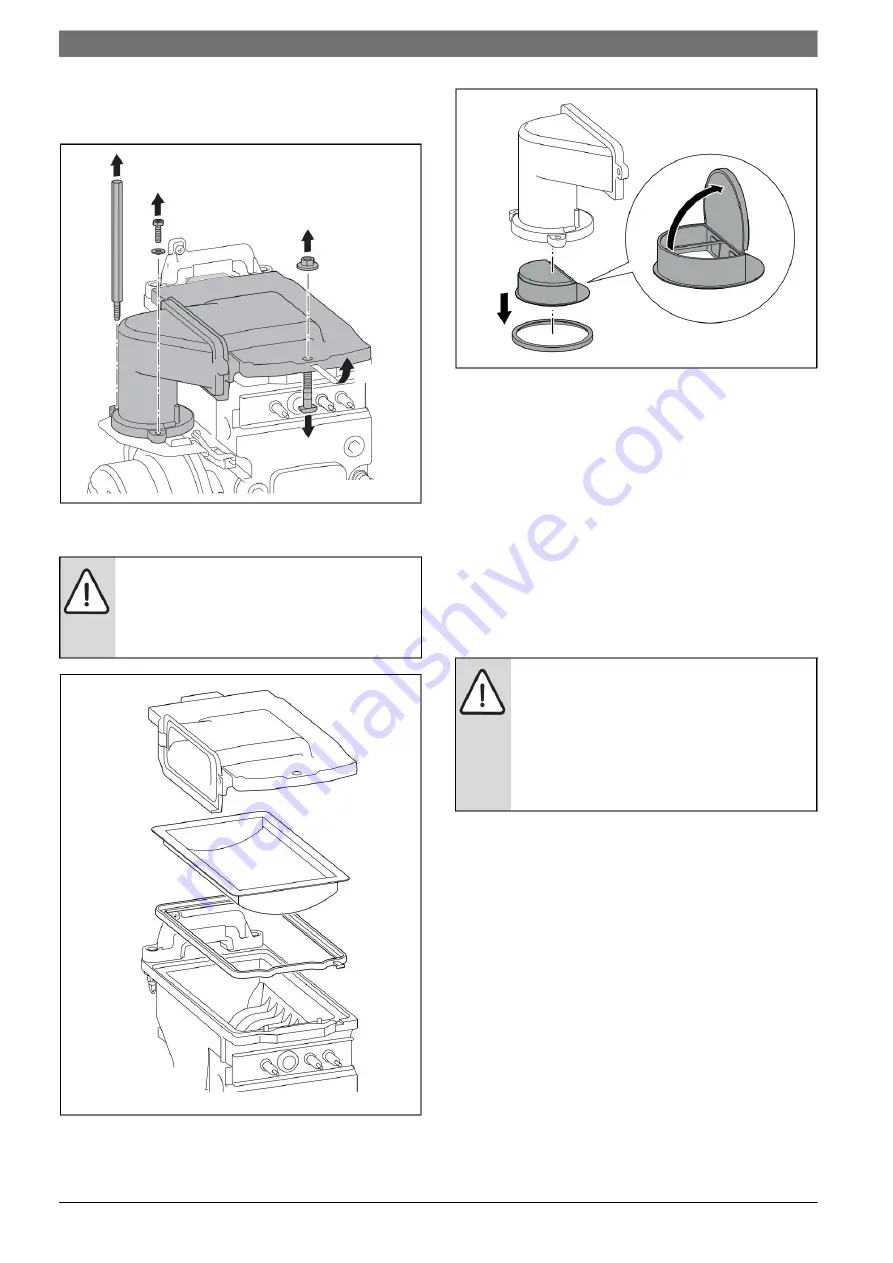
6720813046-66.1N
2.
1.
Cerapur GC9000iW
6720813052 (2016/10)
1.
1.
1.
2.
6720813046-65.1N
12.5 Visual inspection for general signs of corrosion
12.6 Clean and fill condensate siphon
12.4 Check the burner and non-return valve in the mixer
gen
6720813046-79.1N
ÿ Remove burner and clean parts.
fen.
Fig. 41 Remove burner cap
If the condensate siphon is not filled with water, escaping
flue gas can endanger people's lives. ÿ Before reinserting,
fill the condensate siphon with water. ÿ Check the seal
for gas tightness after installation
Fig. 43 Non-return valve in the mixing device
check.
ÿ Replace any corroded pipes. ÿ Also visually
inspect the burner, heating block, siphon, automatic air vent and all
couplings in the device.
Fig. 42 Remove the burner
32 | Inspection and Maintenance
ÿ All gas and water-carrying pipes for signs of corrosion
ÿ Unlock condensate siphon [1]. ÿ
Push the condensate siphon forwards. ÿ Take
out the condensate siphon downwards. ÿ Check
the opening to the heating block for continuity. ÿ
Remove and clean the siphon cover. ÿ Check the
condensate hose and clean if necessary.
ÿ Install non-return valve. ÿ Install
burner. ÿ Install burner cap with
mixing device. ÿ Check the gas/air ratio.
assemble follow.
ÿ Measure the CO/CO2 content (ÿ page 19).
check device ÿ
Remove burner cap with mixing device.
Final work:
CAUTION: Damage to the new seal. ÿ First
mount the new seal on the burner. ÿ Burner with new
gasket in reverse rows
ÿ Remove the check valve. ÿ
Check the non-return valve for dirt and cracks.
WARNING: Exhaust Poisoning .
Machine Translated by Google
Summary of Contents for Cerapur 9000i
Page 41: ...6720813052 2016 10 Cerapur GC9000iW 41 notes Machine Translated by Google...
Page 42: ...6720813052 2016 10 Cerapur GC9000iW 42 notes Machine Translated by Google...
Page 43: ...Cerapur GC9000iW 6720813052 2016 10 43 notes Machine Translated by Google...
Page 45: ...Machine Translated by Google...